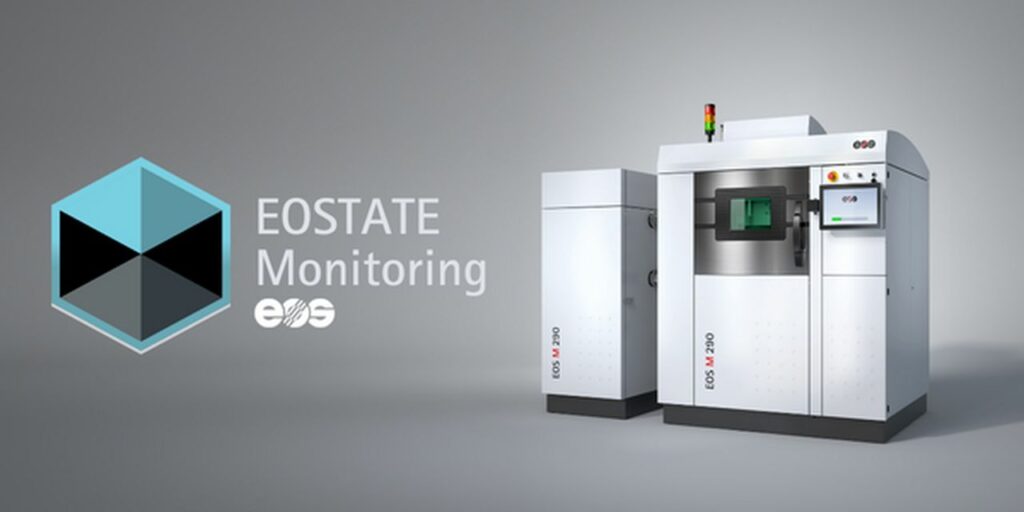
EOS has made arrangement with the Oak Ridge National Laboratory for collaboration on advanced 3D printer research and development.
The deal appears to involve EOS supplying ORNL with a new EOS M 290 metal 3D printer equipped with the company’s EOSTATE MeltPool monitoring system.
EOSTATE MeltPool includes sensors that are aligned with the laser path, which are capable of monitoring thermal activity in real time during print operations. The idea is to keep track of where heat flows occur in order to understand what’s happening at a detail level in the print.
That’s very important because today’s metal 3D printers typically produce production parts. Production parts must meet quality standards, as they might be used in critical applications. This is quite different from polymer 3D printing, where the majority of parts are still for prototyping or other non-production applications.
The key to quality in a metal 3D print is to ensure the material properly crystallizes, and that happens at a microscopic level as a result of the thermal profile created during the print job. By monitoring the thermals, it’s possible to at least determine if there is a likelihood of a bad part being produced.
But could more be done? Might it be possible to correct deviations from the expected thermal conditions at the moment they occur?
That could be the result of the arrangement between EOS and ORNL. The arrangement is to have ORNL researchers working on this and other aspects. EOS explains:
“ORNL is developing and testing its own inspection techniques to identify new methodologies and approaches for quality assurance in additive manufacturing.”
Dr. Ankit Saharan, Senior Manager, Metals Technology at EOS, said:
“As additive manufacturing continues to generate greater levels of appeal for mass production, there is a growing requirement to ensure quality, and build upon one of the greatest strengths of 3D printing which is the capability to monitor parts as they are being built, layer-by-layer. If we can improve quality control processes to the point of making adjustments to builds in real-time, as anomalies are detected, that will save organizations time and energy while improving overall quality control.”
It appears that ORNL will leverage several detection processes from EOS, including EOSTATE MeltPool Monitoring and EOSTATE Exposure OT (optical tomography) EOS methodologies.
This arrangement is to last for two years, and hopefully will result in new quality control regimes that could be implemented by EOS in future equipment.
That could be of great advantage to EOS and their clients, as any step to increase part quality will be very welcome. The cost of a part failing the quality test is equivalent to a print failure, and that is both expensive and time consuming. A new and advanced quality control process from EOS could effectively lower the cost of producing metal parts, and that in turn will lead to more applications.
Via EOS