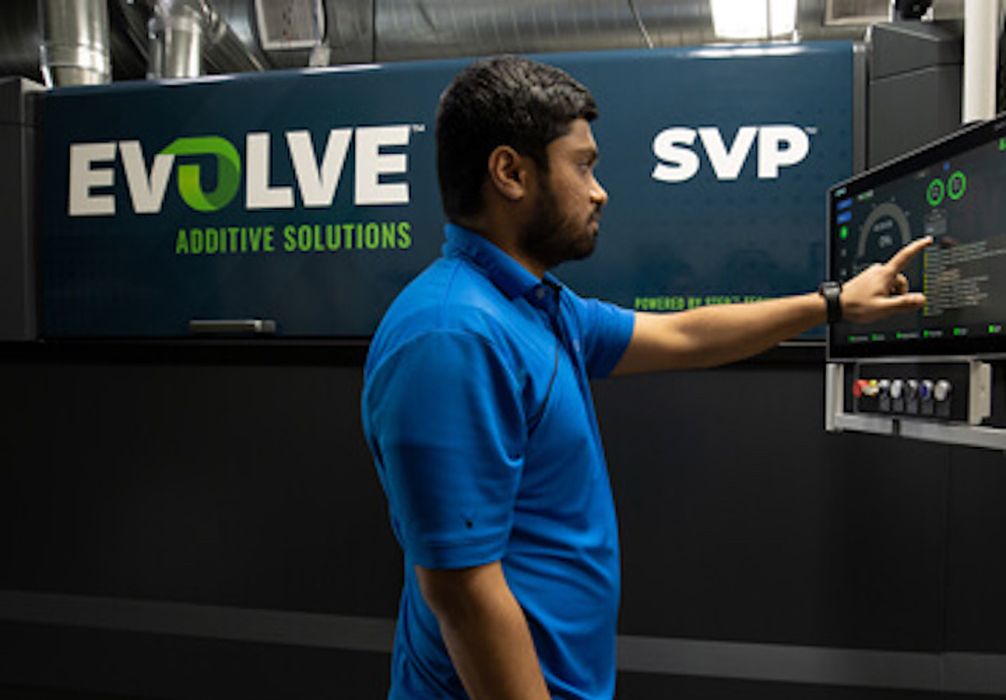
Startup AM company Evolve Additive has now shipped its first commercial STEP system.
“STEP”, or “Selective Thermoplastic Electrophotographic Process”, is the company’s proprietary 3D printing process, and it’s quite unusual.
It’s a powder-based process that is quite reminiscent of 2D printing, and it also has multi-material capability.
Inside a STEP 3D printer you’ll find electrophotographic drums and belts, quite similar to a traditional photocopier. However, the technology works somewhat differently.
A drum is selectively electrostatically charged, and this allows it to “pick up” powder that sticks to the drum. The drum rolls over a belt that eventually carries the “layer” of powder to the build zone, where it is rolled onto the growing object. A heat treatment is applied, along with another roller to press the material together. Eventually, the part is completed.
It’s much like a photocopier that’s printing in place, over and over.
However, there’s more complexity to Evolve Additive’s solution. In their explanatory video, (which inexplicably cannot be embedded here), there are many more belts, drums and rollers than you might expect.
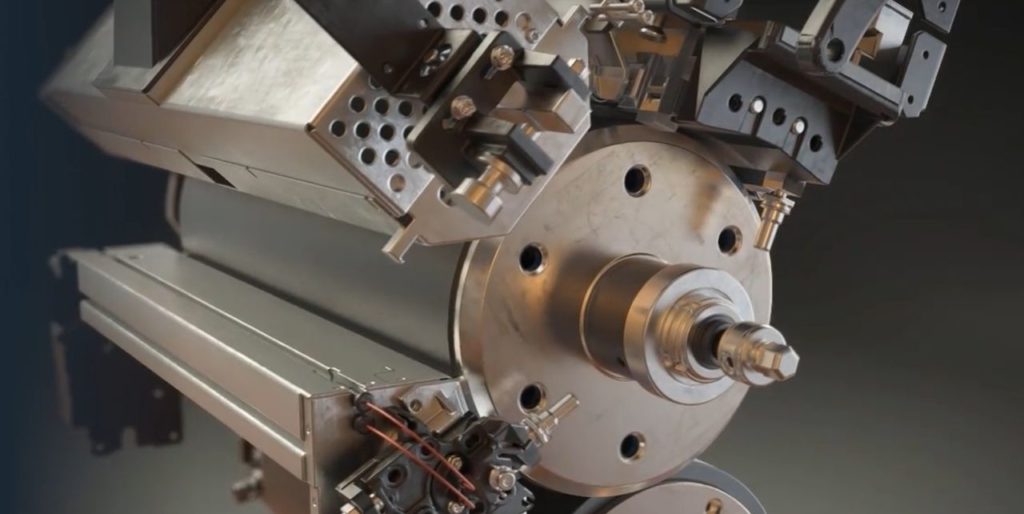
The reason for all this hardware is that the STEP system can handle up to FIVE different powders at once. Again, this is similar to 2D color printing, where colors are produced by CMYK powders. However, instead of ink, STEP uses ABS, TPU and other thermoplastic powders.
For example, STEP can use one model material powder and one support material powder. This allows 3D printing of complex geometries, just like many other 3D printing processes.
However, it’s also possible to involve more materials than just two, and in theory STEP should allow four model materials and one support material.
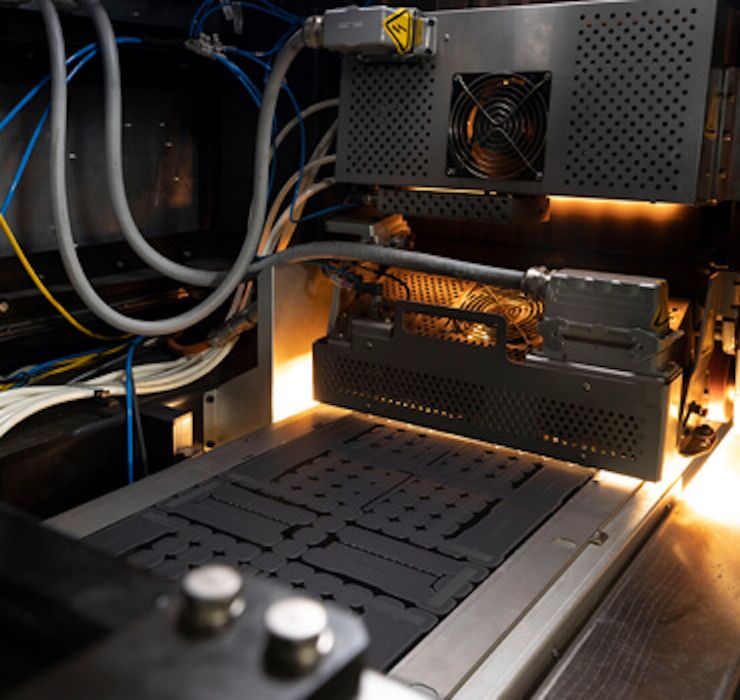
STEP works because it uses closed-loop technology. As you might suspect, the alignment of the belts and drums is absolutely critical. To do so, Evolve Additive prints a small mark that’s used to track the layer as it passes through the system. The machine automatically adjusts to compensate for any unexpected motion, making it possible for the system to work quite accurately even at high speeds.
And that’s perhaps the biggest advantage to STEP: speed. The electrophotographic process is well-understood in the 2D industry, and has led to extremely high-speed paper printing equipment. In fact, Evolve Additive actually uses a Kodak NexPress print engine, which is normally used for high-speed paper printing. Of course, the system is modified for 3D production.
Evolve Additive published a rather detailed PDF white paper describing how STEP works, and it’s a good read for those interested in more details.
For materials, Evolve Additive seems to be focusing on ABS, but they also mention nylon and TPU in their documents. Depending on the electrostatic capabilities of different material powders, it might be possible for a STEP system to use quite a variety of materials. However, it looks like they’re starting with ABS.
This week the news is that they’ve shipped their very first STEP unit, the SVP (Scalable Volume Production) system, to a “global customer”.
Evolve Additive explained:
“The SVP system will be used for large scale volume manufacturing production. The customer’s application includes use of multi-color capabilities, a wide range of materials and Evolve’s proprietary software. Unlike traditional lead times of 3-months+ with injection molded parts, (design release to first article inspection), the SVP platform system can manufacture parts within hours, not months, resulting in faster time to market which is critical to this client along with the requirements of superior part quality and cost savings. The solution also provides flexibility to their manufacturing floor in the form of on-demand production ability.”
Here are some of the more interesting specifications for the SVP device:
- Layer size between 0.010-0.025mm
- Horizontal voxel area of 600 dpi (0.042mm)
- Build volume of 600 x 300 x 100 mm
- 3.3 seconds per layer
- Two-material standard, but Four-material option (one being support)
If that 3.3 seconds per layer is true, then it would appear they could print a full build volume in less than four hours. That’s impressive speed, particularly when you realize no post-processing is required, other than removing the support material.
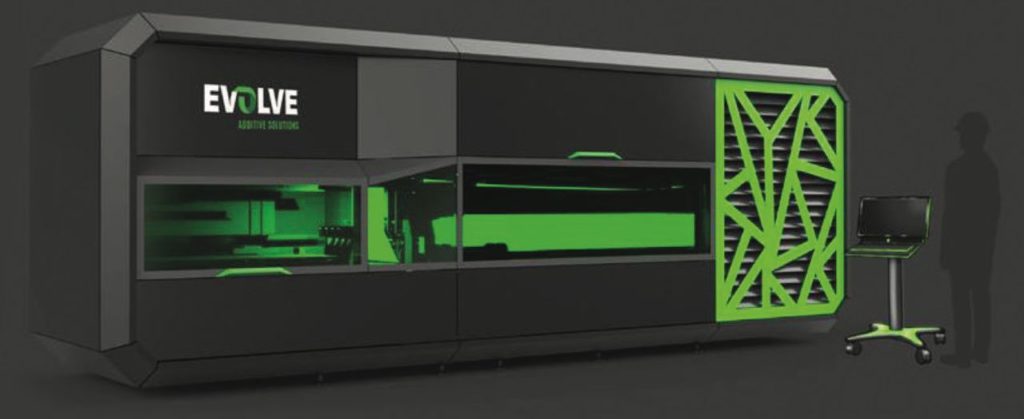
Note, however, that the SVP is a large device. It weighs a huge 3500kg, is six meters long, requires 120 amperes of power, chilled water supply, and a compressed air supply. This is an industrial device.
The STEP technology sounds quite promising, and in theory it could be scaled up to much larger sizes. This could make it an attractive option for manufacturers seeking ways to handle low-volume production jobs.
Via Evolve Additive