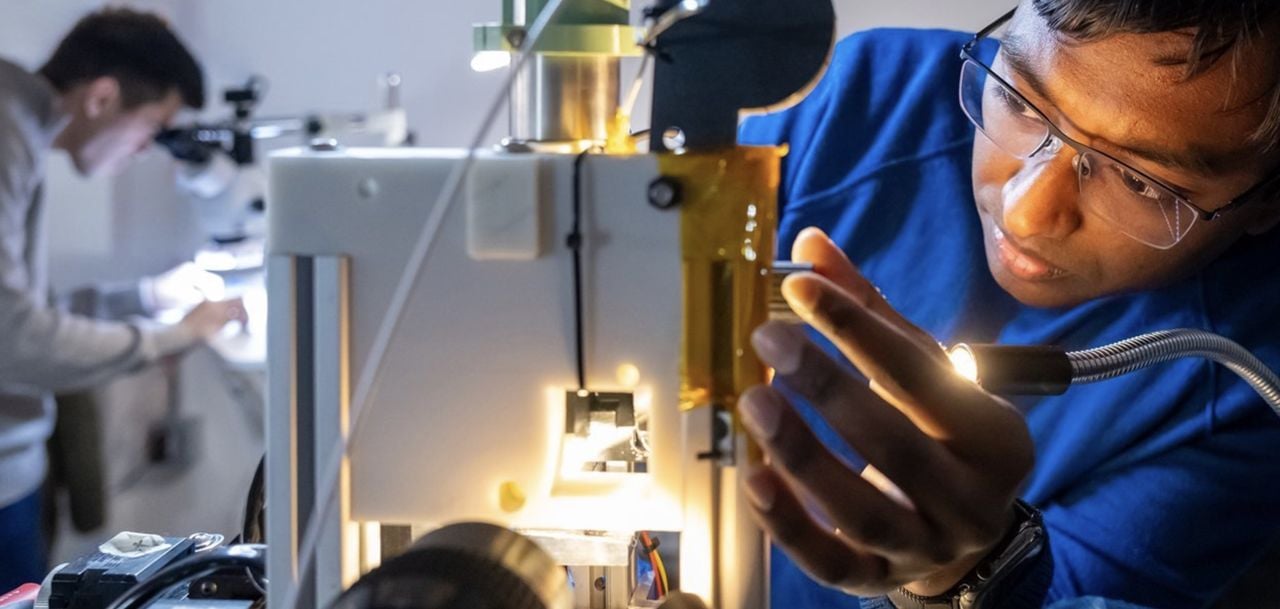
There’s a new metal 3D printing process coming from Fluent Metal.
Haven’t heard of Fluent Metal? That’s because they are a new startup company that was founded by the former Chief Designer at Desktop Metal, Peter Schmitt. The goal of the company is to develop a scalable, affordable and safe metal 3D printing system.
There are, of course, many existing 3D printing systems. Many involve use of powder, which while producing high resolution objects, also poses a number of safety handling challenges. Others involve two-steps, in which objects are printed “cold”, and then sintered afterwards. Finally, there are processes that use welding wire to robotically deposit coarse extrusions of metal.
Fluent Metal’s approach is nothing like any of these. Instead, it’s a liquid metal approach.
It’s somewhat reminiscent of inkjet 3D printing, where tiny nozzles selectively deposit (usually) binder onto powder. However, in Fluent Metal’s systems the droplets are not binder, but instead are liquid metal!
Somehow Fluent Metal has discovered a way to have tiny nozzles drop liquid metal on demand, fed by standard metal wire.
The implication here is that there is NO POWDER! That immediately eliminates all kinds of safety protocols, hazards and handling challenges. This will dramatically reduce the cost of operating the system, since most LPBF operations spend considerable amounts on safety and handling.
Fluent Metal’s system is intended to operate in parallel, meaning there would presumably be a row of deposition nozzles that would sweep across a print bed. These would selectively drop metal that would near instantly freeze solid. This would be similar to binder jetting, except that the object produced would be final, and no sintering would be required.
This approach is eminently scalable, as you need only add more nozzles and lengthen the print bed. It might be possible to build very large metal objects in high resolution with this process.
It’s also sustainable, as the droplets are almost entirely used to produce objects. Unlike most other processes that generate considerable waste, the Fluent Metal approach is quite sustainable.
However, we don’t really know much more about the system at this point. Fluent Metal has not provided any specifications, such as resolution. Nevertheless, the process appears to be very promising.
One other point of confidence is that the company has secured notable investments from several parties, totaling US$5.5M. They’ll need a lot more to build up the company, but that’s a very good start and appropriate for this stage of their development.
I’m looking forward to seeing further announcements from Fluent Metal, particularly when they launch their first machines.
Via Fluent Metal