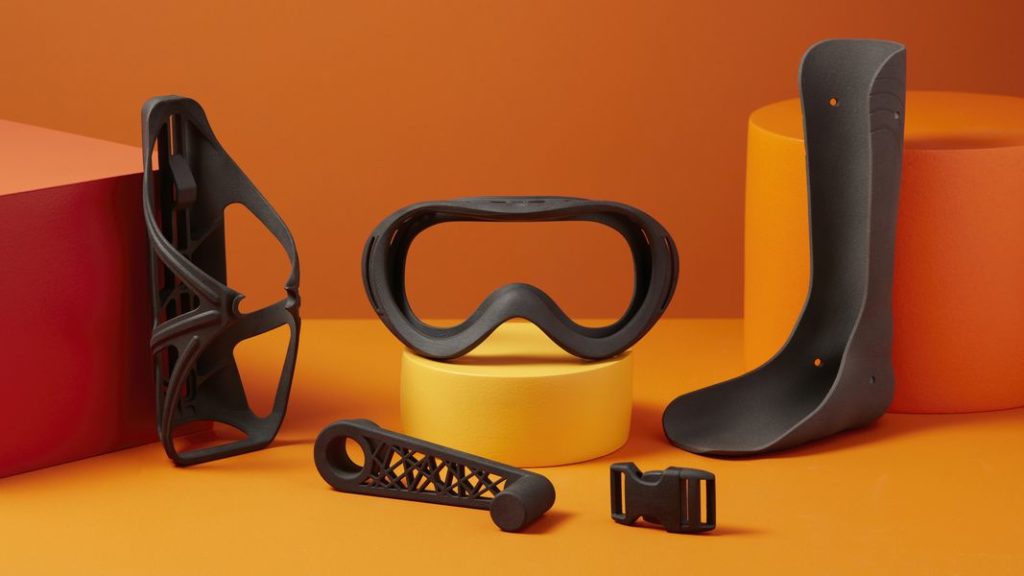
Formlabs announced a new nylon material for their Fuse 1 system, Nylon 11.
After several years of development, Formlabs finally launched the Fuse 1 to the public earlier this year. The machine uses the SLS process, in which a laser selectively fuses layers of thermoplastic powder to gradually form objects.
There are several advantages to the SLS system, with the two most notable being the ability to produce true end-use parts due to the strong materials used, and secondly the ability to 3D print complex geometries without the need for support materials: the support is provided by nearby unfused powder. You can even 3D print stacks of objects within the full build chamber, from top to bottom.
When the Fuse 1 emerged, it came with but a single material: Nylon 12, a popular SLS material. This substance is known for its strength and ability to withstand thermal shock, making it ideal for use in mechanical applications.
But I wondered whether Formlabs would add different materials to the Fuse 1 portfolio, as the more materials available, the better. Each application can potentially have different needs for engineering properties.
My fears were unfounded with todayâs announcement, when Formlabs released information about the second material for the Fuse 1, Nylon 11.
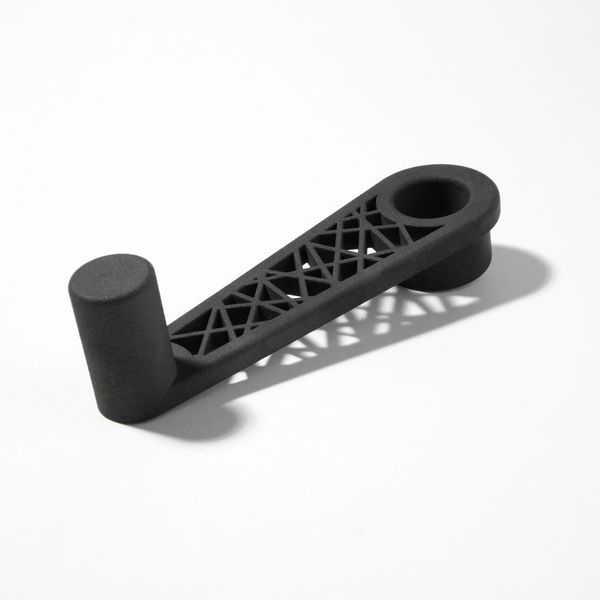
Nylon 11 differs from Nylon 12 in that it is less rigid. In fact, objects 3D printed in this material can be bent or withstand impact forces far greater than Nylon 12.
This means itâs an ideal material for production of parts that have flexible elements, like hinges, snaps, clips, and the like. This type of part is frequently produced on other, more expensive SLS systems, but until today could not be done on the much more inexpensive Fuse 1 system.
Formlabs explains some of Nylon 11âs benefits:
âWhere Formlabsâ Nylon 12 Powder is a versatile material that provides high detail and dimensional accuracy, Nylon 11 Powder is ideal when durability and performance are essential.Nylon 11 Powderâs ductile, strong, and flexible qualities suit end-use parts that must be able to take impact and handle wear and tear over time, including snaps, clips, and hinges. Nylon 11 Powder is also designed for use in manufacturing, production, engineering, and product design.â
They suggest these applications could be unlocked by the new material:
- Impact-resistant prototypes
- Thin-walled ducts and enclosures
- Robust jigs and fixtures
- Replacement parts
- Prosthetics and orthotics
One question I have about the second material is use of two materials on one Fuse 1 system, a question that up until today was moot. On FFF systems itâs easy to swap materials by changing the spool, but this is usually not the case on SLS systems. These systems have ducting systems to collect loose powder, meaning the powdered material is spread over certain interior portions of the machine.
If you want to âjust change the powderâ, you might end up inadvertently mixing the new powder with some of the previous powder unless the machine is completely cleaned out. Based on my rudimentary understanding of the Fuse 1, I suspect this might be challenging.
The result could be that the best course of action for using a second material on the Fuse 1 is to dedicate a second machine to that material. That way you would not have to clean out the machine, which is probably a difficult task.
Dedicated machines for specific materials is not an uncommon practice, and is often done in many workshops. This may be the case with the Fuse 1.
While this is the second material for the Fuse 1, I have a suspicion it wonât be the last. There are many possibilities for even more materials based on the SLS materials offered by competing systems. Some possibilities might include:
- Composite powders, combining nylons with glass or carbon fiber that could provide very strong parts
- Elastomer powders, which could produce flexible parts
- Non-conductive materials for electrically sensitive applications
- Castable powders for creating industrial molds
- Colored materials, although this may be challenging due to the strength of the Fuse 1âs light engine
But thatâs just some speculation. Weâll have to stay tuned to see what Formlabs actually releases for their third material.
Via Formlabs