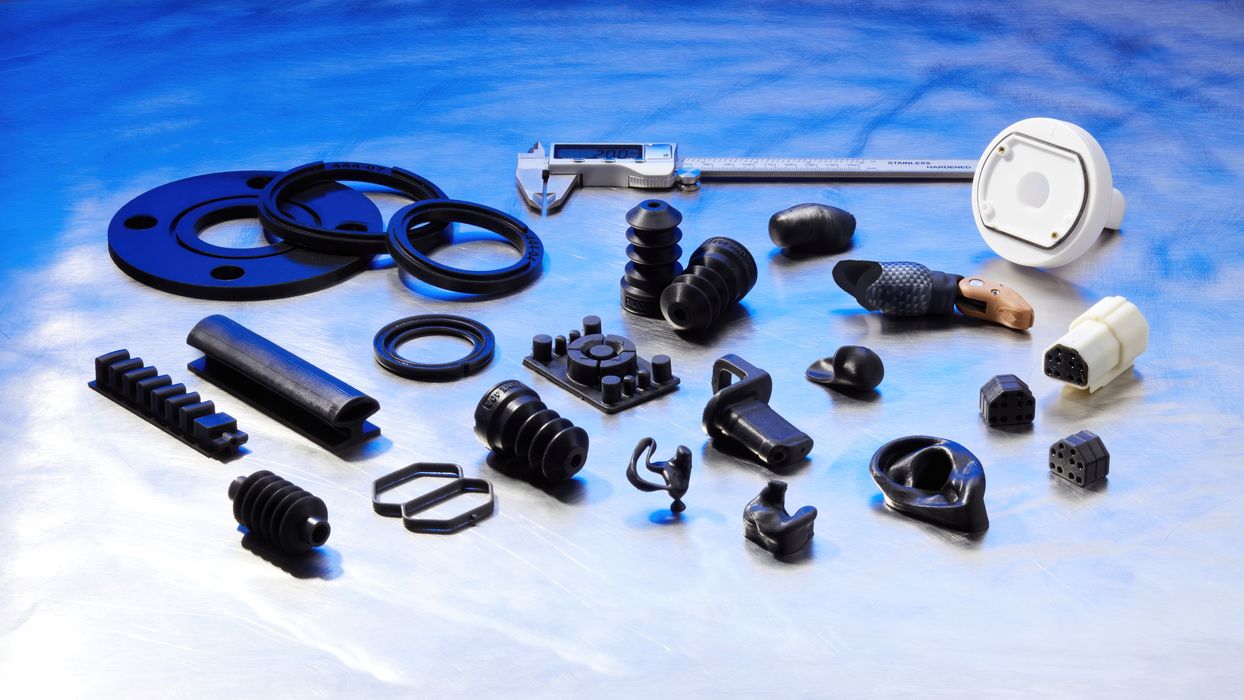
Formlabs announced two new and interesting resin materials and SLS packaging.
The company’s flagship Form 3 systems now boast some 45 different resin materials, making them one of the most versatile platform for 3D print production. The material catalog addresses the needs of multiple industries, ranging from mechanical parts to dental applications.
The new materials are Silicone 40A and Alumina 4N.
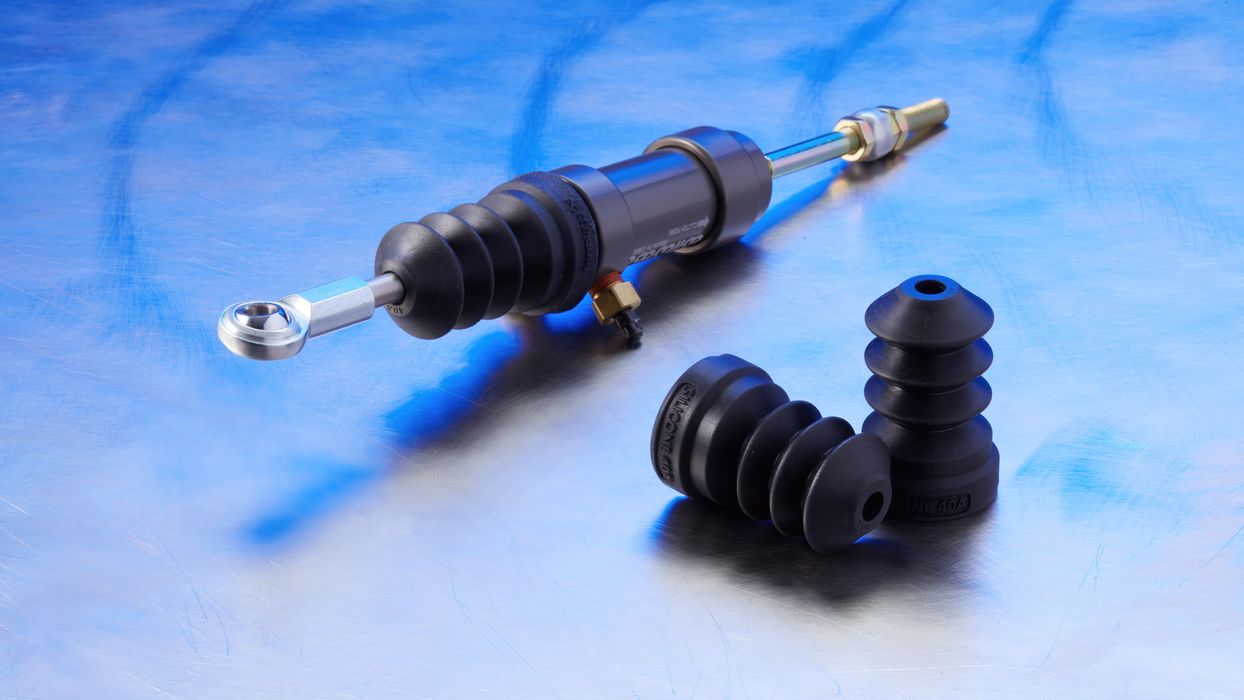
Silicone 40A is a flexible material that when printed mimics the performance of molded silicone. However, because this material is 3D printed, it’s possible to produce geometries that are not possible with molding approaches. Formlabs has developed a new method they call “Pure Silicone Technology” for this purpose, which is currently patent-pending.
Formlabs explained that Silicone 40D parts can be repeatedly stretched, bent, or compressed without losing their mechanical properties. This makes the resin ideal for certain applications requiring heavy-duty flexible parts.
It should be quite interesting to see what new applications can be developed by 3D printing silicone versus traditional molding.
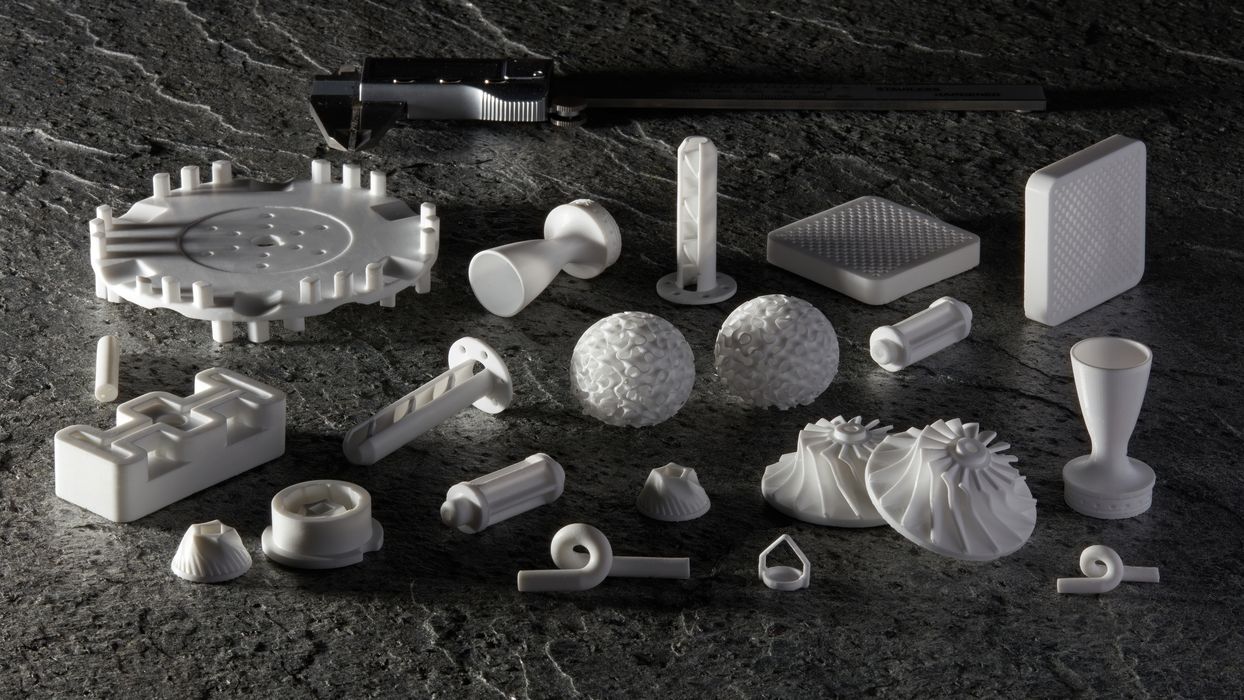
The other new material, Alumina 4N, is actually a ceramic resin. After post processing, parts will have a 98.6% relative density and 99.99% purity. These ceramic parts will be ideal for use in applications that require extreme thermal or chemical resistance.
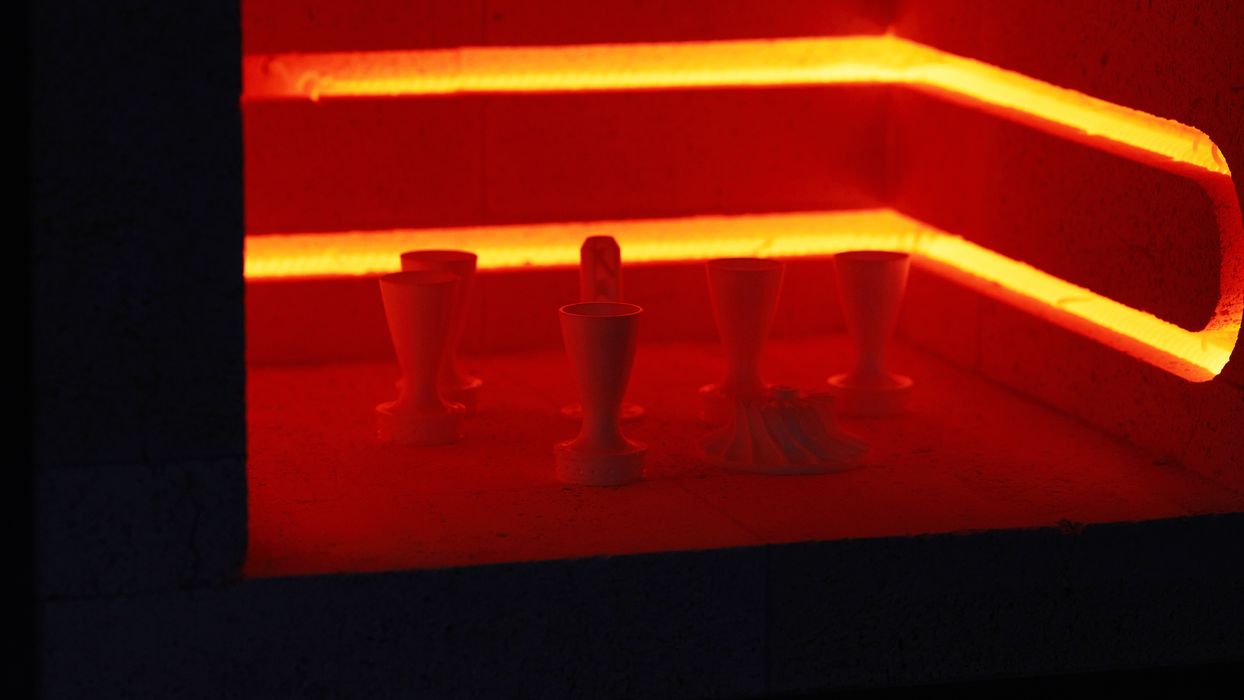
As the silicone material allowed for new geometries, so does Alumina 4N. There should be many more ceramic applications possible with this material on the Form 3+ platform. Formlabs said their system is by far the least expensive solution that can produce ceramic 3D prints, and that’s likely true based on my understanding of the ceramic 3D printer market.
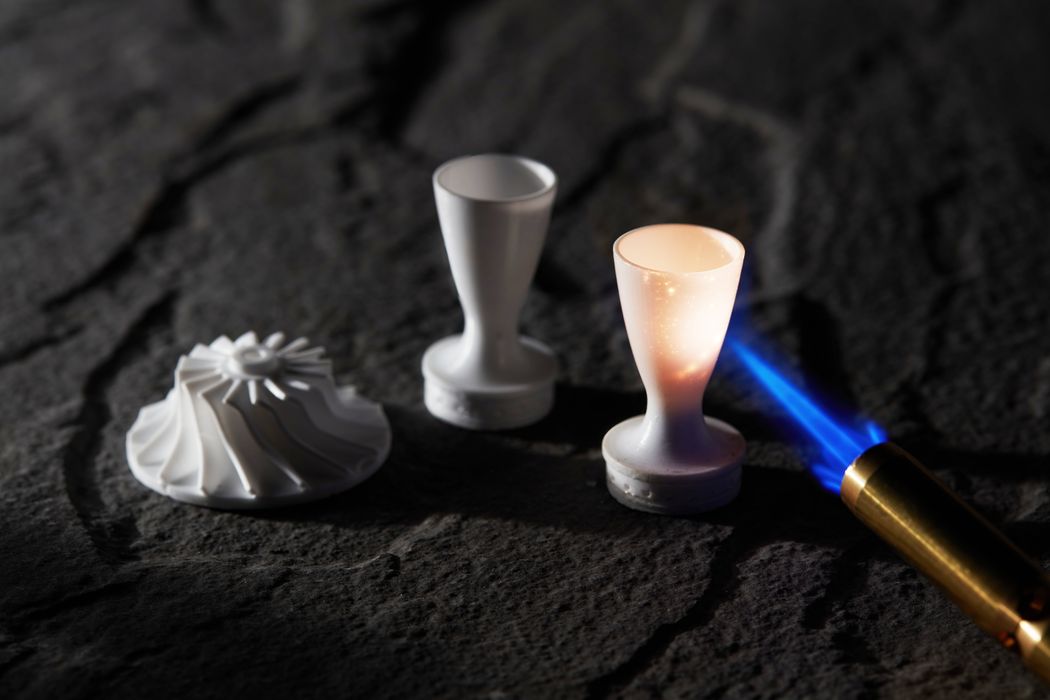
Formlabs co-founder and CEO Max Lobovsky explained:
“So much attention in the additive industry is focused on hardware, but materials are just as essential for delivering on our mission to create user-friendly, cost-effective 3D printing solutions so that anyone can make anything. That’s why we continue to innovate relentlessly in the material space, creating high-performance materials that unlock new possibilities in manufacturing, healthcare and other industries. With Silicone 40A and Alumina 4N, we’re combining the flexibility and efficiency of 3D printing and the performance of silicones and ceramics, at a price point that anyone can afford. We’re thrilled to both expand our ecosystem and make our Fuse 3D printers more accessible so our customers and new users can truly create anything at an affordable price.”
I’m looking forward to seeing new ceramic and silicone applications.
The company also announced new solutions for their Open Platform system that allows for the use of third party resins in their PreForm software. The new resins include dental biocompatible materials, and should be available in October.
Finally, Formlabs also announced a new packaging for their SLS system, the Fuse 1+. The new “starter package” is priced at US$25K and includes not only the printer but also the Fuse Depowdering Kit for low volume production.
Via Formlabs