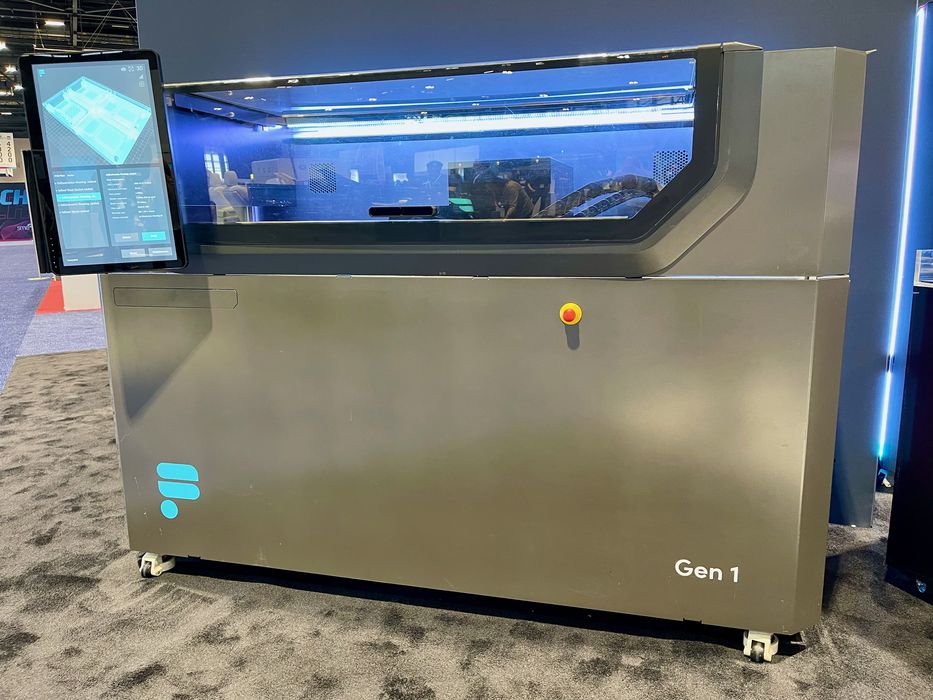
There’s been an impressive amount of progress at Foundry Labs since our last check-in.
This innovative company from New Zealand is working on a truly unique way to create metal 3D parts by combining 3D printing and casting technologies into what they’ve dubbed “digital metal casting”. To get an idea of how this breakthrough process works, let’s take a closer look:
- First, a design for a metal part is conceived and the corresponding mold is crafted, consisting of two separable halves.
- These molds are 3D printed utilizing a binder jet process with ceramic powder, resulting in what are called “green” parts.
- These green molds are then placed into a microwave device for curing. Though they are brittle post-cure, they can handle high temperatures.
- Designed to bolt together, these molds form a void inside that corresponds to the original part.
- After bolting, the mold is positioned upright with metal ingots placed on top where the sprue is expected.
- The entire assembly is put back into the microwave for a high-temperature treatment that melts the ingots. This molten metal then flows into the void via gravity.
- A vacuum aids in eliminating any trapped air bubbles.
- Post-melting, a gas is used to quench the mold, bringing it back to room temperature in a mere 30 minutes.
- Finally, the part is extracted from the mold, the sprue is trimmed, and voila! You have a fully solid metal part in as little as five hours.
- As the folks at Foundry Labs like to quip, “you can get metal parts before lunchtime”.
Foundry Labs’ Growth and Future Plans
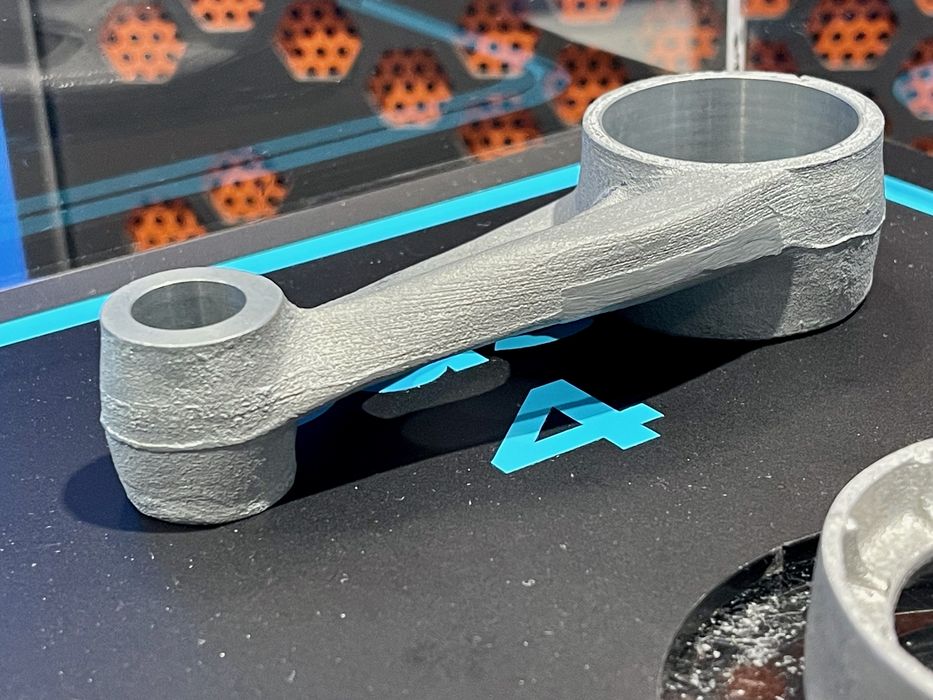
In just half a year, Foundry Labs has been industrious indeed. We previously covered their “Gen 1” system. They have since developed an upgraded “Gen 2” and are already focusing their efforts on a “Gen 3” iteration. The latter, notably, is intended to be the mass-produced, production version that will be available to clients.
What’s more, the company has taken a major step by launching a demonstration center in Fremont, California. This allows US-based businesses to thoroughly investigate their groundbreaking technology and see how it can be integrated into their operations. Companies could even try to print their own metal parts using the system to assess part quality and get a feel for the usage process.
Foundry Labs faced significant challenges while establishing the Fremont center, apparently due to the microwave component of their device. They had to navigate complex regulations around equipment importation but were eventually successful in getting their Gen 2 device installed for use.
A Unique Approach to Metal 3D Printing
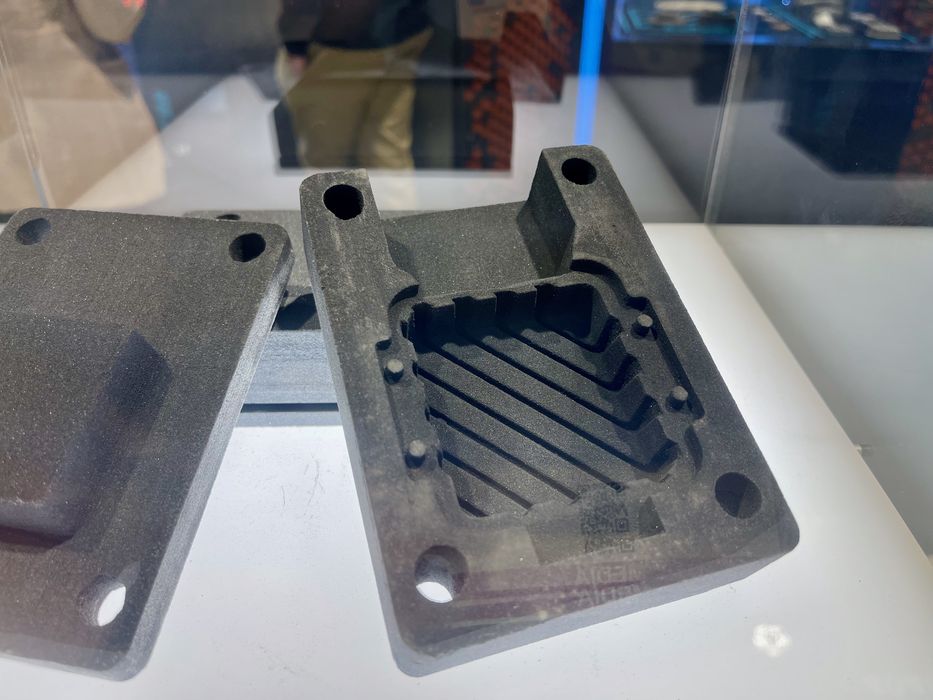
Emphasizing their commitment to integrity, Foundry Labs is currently refraining from accepting pre-orders. Instead, they prefer to finalize the development of their technology and equipment before proceeding with customer orders. At this stage, they are accepting letters of intent from interested parties and plan to start accepting pre-orders later this year, with shipping anticipated in mid-2024.
With their unique and highly capable process, Foundry Labs brings something fresh to the world of metal 3D printing. We’re sure there will be many customers eager to explore their system.
Via Foundry Labs