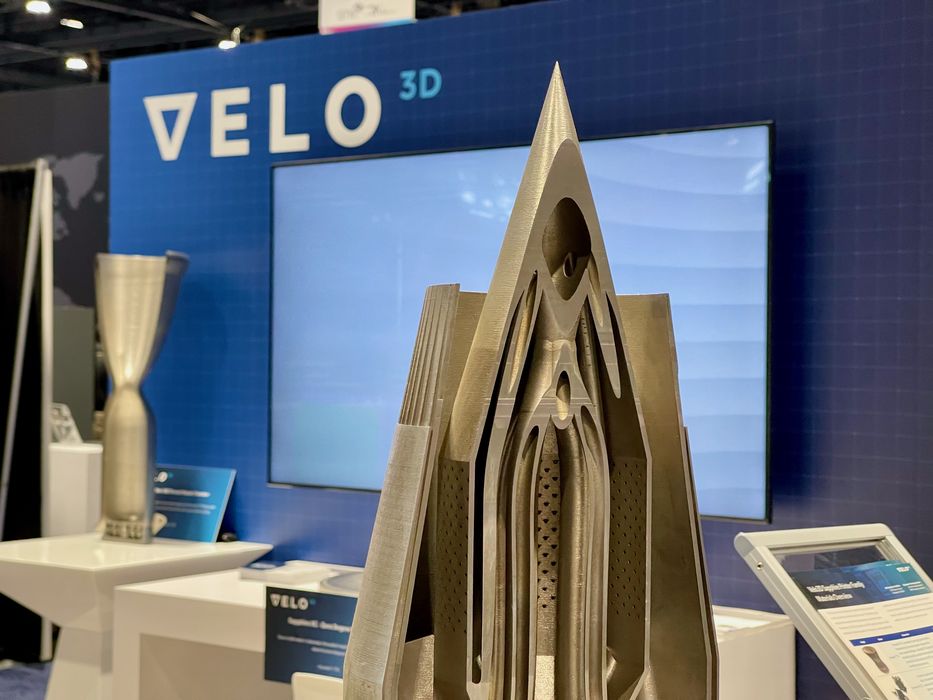
Velo3D is one of the leading providers of metal additive manufacturing equipment, and we caught up with them recently.
While the company’s valuation is certainly the most volatile in our weekly 3D print leaderboard, their technology is not. Their system is quite unique among metal LPBF systems in that it requires almost no support structures due to their recoating technology. This vastly simplifies the post processing required for parts produced on their Sapphire systems.
It seems they’ve been quite busy over the past while. We learned of the following:
They’ve introduced a new metal material, Aheadd CP1, which is a high performance aluminum-iron-zirconium alloy that includes no volatile or rare earth elements.
Velo3D has tuned their systems to both improve part strength and increase production throughput. The systems can 3D print thicker layers, up to 0.1mm, which offer more strength.
They’ve partnered with PhysicsX, an UK-based AI company that produces a system that recreates actual physics. This enables customers to explore solution envelopes to increase part performance in ways not previously possible.
The story behind their relationship with PhysicsX is interesting. Velo3D first worked with them to solve a technical issue: soot was building up on the cameras of the Sapphire equipment over time. The solution turned out to be a flow of argon gas that keeps the cameras clean. Their experience with PhysicsX on this project led them to partner with them on a more integrated basis for customers. PhysicsX is now a member of Velo3D’s Technical Partner Program, along with other providers.
We were told this integration is, for now, separate from Velo3D’s job slicing system. However, I got the impression that it might be more deeply integrated in the future.
The company has worked with a number of notable customers, including SpaceX. One of their more recent examples of successful use of Sapphire technology has been with F1 racing, where their equipment was used to 3D print highly sophisticated metal heat exchangers.
Another example is the use of M300 tool steel to produce tooling for manufacturers. The idea is to produce the required tool, but include tiny channels within the structure. These would be used for cooling by circulating a fluid while the tool is used in hot production environments.
This approach dramatically lengthens the usage lifetime of the tool, and thereby changes the financial equation: it could be less expensive in the long run to 3D print an advanced tool than cast multiple conventional tools, because the 3D printed versions don’t wear out.
I’m always impressed with Velo3D’s technology, and I often wonder why investors sometimes fail to see the potential of their equipment.
Via Velo3D
Kerry Stevenson’s insightful article on Velo3D’s advancements in metal additive manufacturing technology is a testament to the rapid evolution of 3D printing. The introduction of the high-performance aluminum-iron-zirconium alloy, Aheadd CP1, is a significant stride in the industry, especially considering its composition excludes volatile or rare earth elements.
The collaboration with PhysicsX is another fascinating aspect, as it opens up new possibilities for enhancing part performance. The application of AI in solving technical issues and improving production processes is a promising direction for the future of manufacturing.
The examples of Velo3D’s technology application in F1 racing and tooling production are impressive. They highlight the potential of 3D printing in creating sophisticated, durable tools that can withstand high-temperature environments, thereby increasing their lifespan and cost-effectiveness.
As a fellow enthusiast in the 3D printing industry, at Spider3D ( https://www.spider3d.co.il ), we share the excitement for these advancements and look forward to seeing how Velo3D’s technology continues to shape the future of manufacturing.