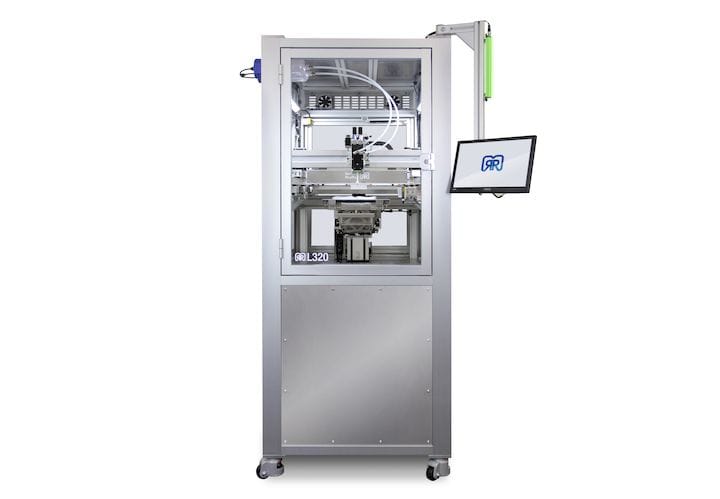
I spoke with German RepRap’s Andrea Berneker to learn how they have been deploying their silicone LAM process.
The LAM process, or “Liquid Additive Manufacturing” process is a unique method of 3D printing silicone material. Their popular L320 3D silicone printer uses LAM to enable production of complex silicone parts.
LAM involves the use of dual extruders: the material is stored in two separate reservoirs, and then is mixed at the time of extrusion. A heating pass then confirms the chemical reactions to properly form the silicone on each layer.
LAM allows a designer to produce relatively complex silicone shapes, which in traditional manufacturing are quite limited in geometry. Typically gaskets or similar rudimentary shapes are produced, but LAM could allow for the production of far more complex designs.
This moment in the Silicone Journey seems quite analogous to a time years ago when thermoplastic 3D printer manufacturers were faced with potential clients that, while interested in 3D printing, were struggling to figure out how to best use it.
At that time the thermoplastic vendors organized educational programs, case studies and even specialized vertical application units to help guide their clients to fully leveraging the technology. In many cases you can’t know what to do unless someone inspires you with examples.
That seems to be the case with silicone at the moment, as Berneker explained German RepRap has application specialists on their sales team. These folks are “very educated” in advanced silicone design, and are able to show clients complex examples that can “hint” at new creations.
One of the most typical design innovations that can take place with silicone is to use interior channels. This is not something that would normally be considered for an injection-molded silicone part, and so designers must be made aware of the option, as well as many other possibilities.
Berneker says the sales process for LAM machines can be lengthy, even up to a year for a client to make a decision on purchasing equipment. This is likely due to the mental transformation that must take place: “Why buy a machine that will make the same parts we make now?”
Instead, these clients have to think: “We need a machine to make DIFFERENT parts than we previously made!”
Evidently it takes considerable time for that thought to solidify in the minds of many clients, and that’s not surprising. The step into fully-leveraged 3D print design is quite challenging and even after a company “gets it”, they then have to creatively identify a possible application for their clients.
And then convince them, too.
But I believe the effort is worthwhile. The thermoplastic and metal 3D printer manufacturers went through that process and today we find an increasing number of industries using 3D printing on a daily basis, some for end-use part production.
The transformation takes years, but everyone will be better off afterwards.
Via German RepRap