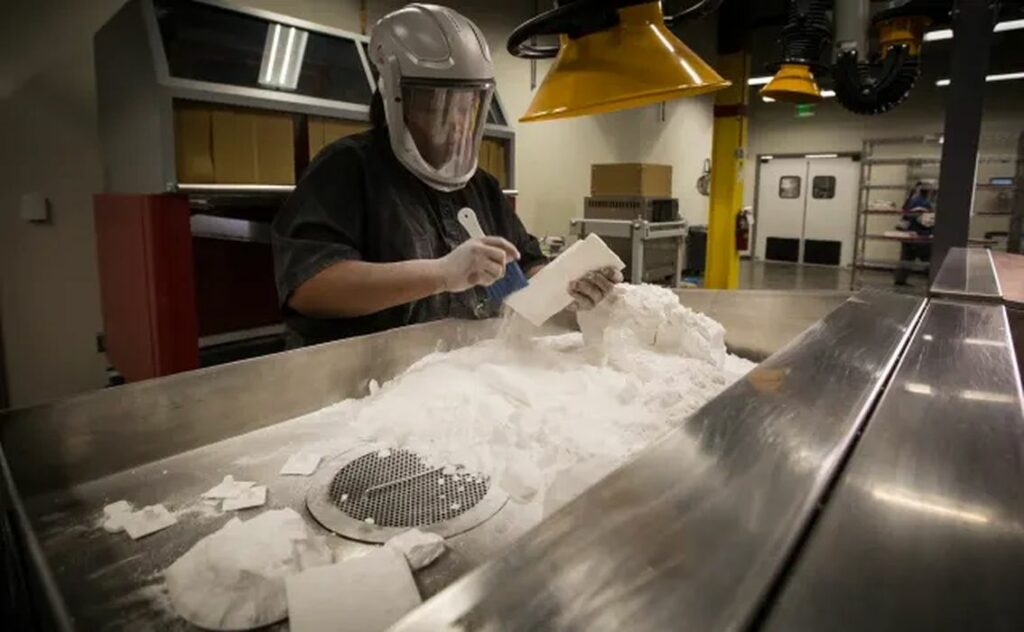
There are some common pitfalls to consider when selecting 3D printing materials.
For engineers and product designers looking to enhance their manufacturing processes by adopting or increasing their use of 3D printing, the importance of materials selection can’t be overstated. Yet with an array of options, selecting the best material for a given product can be daunting. For Protolabs 3D Printing Process Engineering Manager Jon Eric Van Roekel, materials advancement is what he’s most excited about for the industry.
“Materials advancement is the single most important thing to keep growing 3D printing,” Van Roekel says.
Choosing the Right Materials Primer
Proper selection of these advanced materials starts with asking questions about the target properties for the part’s end use. The main considerations are knowing the part’s desired tensile strength, its tensile modulus or stiffness, its elongation or ductility, the desired hardness, and heat deflection temperature. Various materials will have different ratings for those criteria and even the same material can perform differently based on its quality and how it was produced.
Various 3D printing companies like Formlabs and Simplify3D offer material selection guides for customers. Protolabs’ offering breaks material options down into the overarching categories of plastic, metal, and elastomer & liquid silicone rubber.
Stereolithography (SLA), SLS, Multi Jet Fusion (MJF) and Carbon Digital Light Synthesis (DLS) are the types of 3D printing processes used for plastic materials. Plastics are the most common material historically used in 3D printing, with material options such as ABS, nylon, polycarbonate, and polypropylene available.
Metal materials are typically used to manufacture products with 3D printing that are also produced through traditional processes like sheet metal fabrication or CNC milling. There’s been increasing interest in metal 3D printing for making things like circuit boards for consumer electronics and aircraft engine repair parts. Direct metal laser sintering (DMLS) is the process for metal 3D printing and uses materials like aluminum, cobalt chrome, copper, Inconel, stainless steel and titanium.
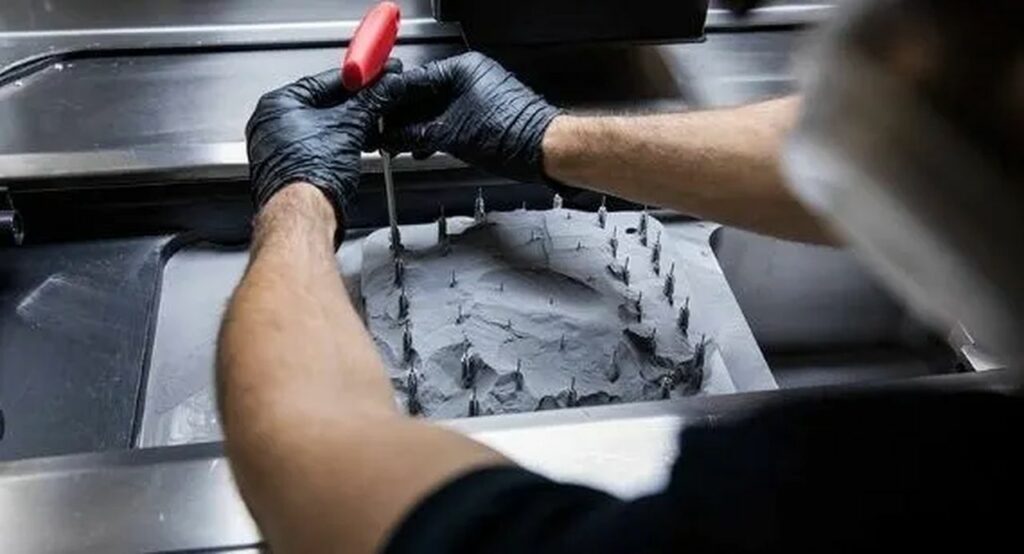
For elastomer and liquid silicone rubber materials, SLA, SLS and PolyJet 3D printing processes are utilized. Silicone, TPU and various digital photopolymers are typical materials within this category.
Each material is generally suitable for different applications and has its own advantages. For example, nylon’s tough but semiflexible nature makes it a good choice for electrical cord casings and functional part housings. ABS is also tough but less costly, making it a good option for toy parts and medical device prototypes. Meanwhile metals can be a good choice when more weight is desired or, in the case of aluminum, when high strength and lower weight is the goal. Silicone is a good material for both prototypes and end-use products as it is resistant to high temperatures and can also regain its shape following deformation.
Beyond Prototyping
3D printing has advanced far beyond a mere prototyping tool thanks to advances in materials due to work by prominent chemical companies such as Dow, BASF and Mitsubishi Chemical. In the past, additive materials had a reputation for being brittle and lacking UV stability, thus making them ill-suited to end-use products. However, material advances have broadened the range of 3D printing applications, especially for SLA resins.
Additionally, more unique materials have emerged such as carbon, which can increase strength with epoxy-like properties. Nylon thermoplastics with higher stability have also opened up more 3D printing end-user applications such as speaker housings in high-end vehicles. In the world of metals, the emergence of various high-performance temperature-resistance alloys has largely been driven by demand from the aerospace industry.
“It’s really about validating and understanding the range of properties you should get with a given material like nylon or a specialty metal like titanium or stainless steel,” says Van Roekel. “It’s about understanding the range of properties exhibited by the materials.”
Some companies like Protolabs develop their own internal data sheets for materials due to discrepancies in the industry between what manufacturers claim about a material and how it actually performs.
For example, a customer might decide that titanium is best without understanding that the titanium they purchase isn’t going to be 100 percent wrought but rather will be an alloy containing elements like silicone and magnesium. This can give rise to minor differences in the manufactured materials, which could result in end-use products not performing quite as anticipated.
Read the rest at ENGINEERING.com