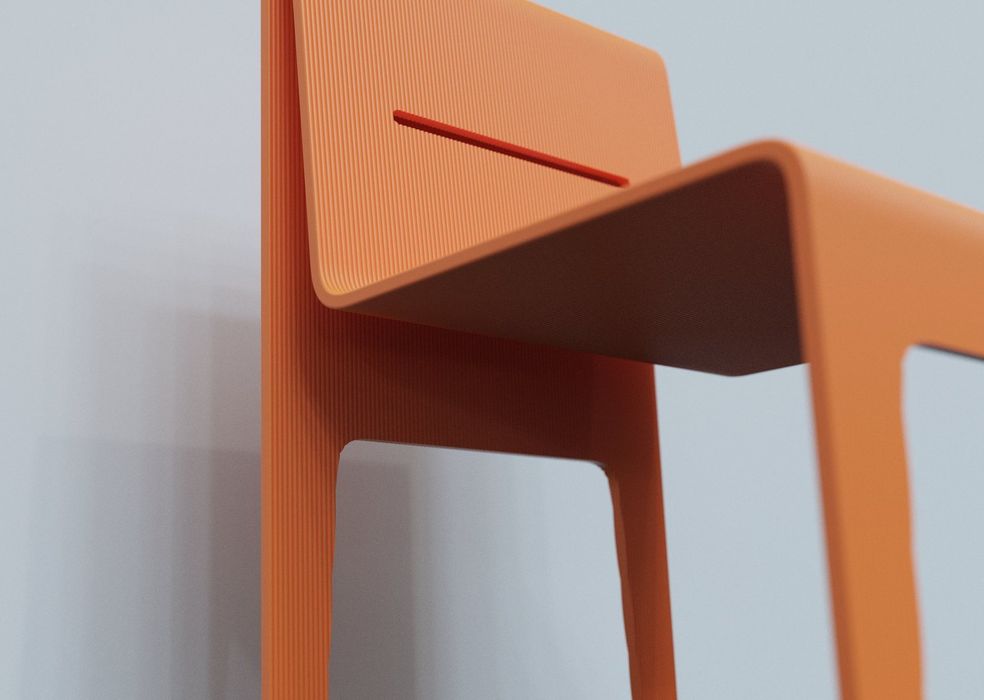
A new 3D print-based furniture venture has launched: Haddy.
The Florida-based operation has developed a scalable method for producing eco-friendly furniture using 3D print technology. They can print full-size furniture items using robotic extrusion technology.
Exploring the Team Behind Haddy
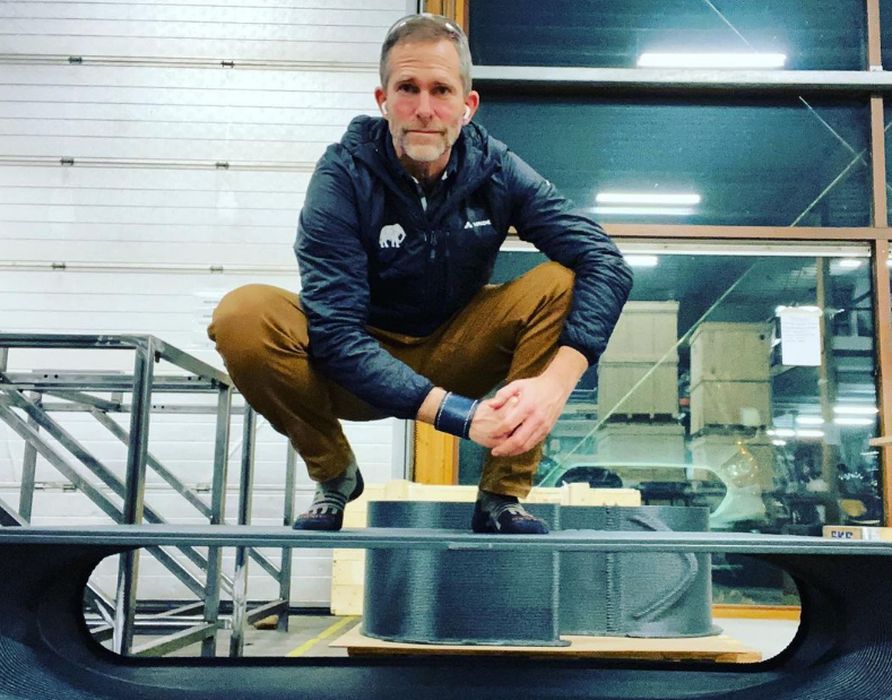
A look at the team members of the new company shows that many of them came from the now-defunct Local Motors, which was among the first to explore the idea of 3D printed cars and vehicles. In fact, the founder of Local Motors, John B. (Jay) Rogers, is also the co-founder of Haddy. The small team includes engineering, IT, materials science and design expertise, just what you’d expect for a firm producing 3D printed furniture.
Haddy’s Technology for Eco-Friendly Furniture
The technology used by Haddy is extrusion using robotic arms, as provided by CEAD, one of the company’s partners. This technology enables easy production of large objects — including furniture.
I’ve frequently seen this style of 3D printed furniture: coarse-layered, clean and simple design. However, those sightings were always of an experimental or demonstrative nature. Here, Haddy is commercializing this concept.
The Circular Economy Concept at Haddy
A key concept for Haddy is the notion of a circular economy. All of their products will be made from recyclable materials, and it seems the intention is to convert used 3D printed furniture back into materials that can then be printed into new furniture styles. All of their materials are said to be “100% reusable composite”.
Haddy explains:
“Using a hybrid process of additive, subtractive and assembly with robots, we are harnessing digital manufacturing for positive impact on the planet. Circularity, for the planet is designed into all of our products, from factory to customer and back again. Our materials, stay in a closed-loop process, new things from old things. Keeping them out of the landfill and giving them new life.”
Haddy’s MicroFactories and Local Production
Another concept from Haddy is something they call “MicroFactories”. These appear to be a drop-in design for a 3D print factory that can be placed in local environments to produce furniture. The idea is to reduce transport costs by making products locally.
Haddy apparently also uses non-3D print making technologies, as they discuss materials such as metal, wood, leather and marble on their website. It’s not clear how this is done, but one video shows a CNC mill in operation.
Much of the furniture in the West is made overseas, but it may be that the Haddy MicroFactory concept could turn that equation around and financially enable local production of furniture.
According to information in the St Petersburg Catalyst, the company hopes to hire 25 new staff and operate eight robots onsite.
This is a very interesting concept, as it would appear that Haddy has done the numbers and determined that this approach could be successful.
Challenges for Haddy: Design and Acceptance
Two challenges I see for the company would be design and acceptance.
Will customers resonate with the peculiar style of 3D printed furniture designs? We’ve seen this style of item previously, but so far it hasn’t caught on to the mainstream. However, it may be that Haddy’s design team can come up with attractive designs for customers.
The other challenge could be acceptance. The MicroFactory concept requires local entrepreneurs to take on the concept and operate them. Will they? That depends a lot on how Haddy will make them available to local partners, either through a franchise model or other mechanism.
This is a fascinating project and I’m interested to see how it plays out.
Via Haddy and St Petersburg Catalyst (Hat tip to Tuan)