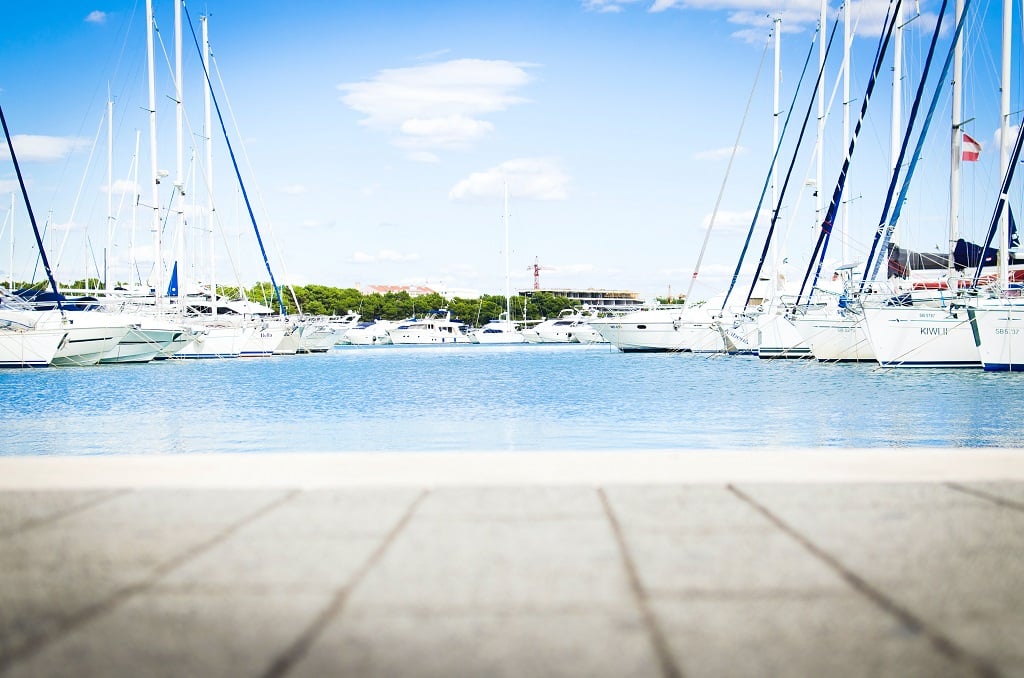
3D printing has penetrated a range of sectors and industries to a point where it is being adopted by mainstream organizations in their manufacturing processes. However, one sector that has been left behind in this adoption is the maritime industry.
There are a string of reasons why the industry has been slow in adopting 3D printing technology, such as the sheer size of the vessels, heavy regulations, and the need for compatible materials. But now we are seeing a positive trend in the industry for the adoption of 3D printing technology.
A Sea of Potential
The maritime industry is responsible for 90% of global trade. It is a crucial cog in the trade wheel. The industry is facing significant challenges, from regulations to aging vessels to overcapacity. These challenges make it all the more important to reinvigorate the industry with new technologies and processes to make it more agile and profitable.
The maritime industry includes ship manufacturing, shipping companies, logistics companies, ship repair, maintenance companies, and port authorities. All these individual entities, at some level, are exploring the use of 3D printing.
There are a stream of applications for 3D printing in the maritime industry, such as product innovation and customization, spare part manufacturing, on-demand manufacturing, and much more.Ā
Letās take a look at how 3D printing impacts the maritime industry and specific areas where the technology could be leveraged.
Innovation and Product Development
In every industry, 3D printing helps in rapid new product development. Engineers can innovate, create new and efficient designs, test their designs, and iterate rapidly to develop superior products.
3D printing enables affordable and faster product development with a range of materials. This pace helps in saving huge amounts of costs. This can also help in developing customized parts for specific applications at a fraction of what it cost previously.
Repair
Ships and vessels regularly need maintenance and repair operations. Certain 3D printing technologies like directed energy deposition (DED) are used not only to build new objects but also to add material onto existing parts. In case a certain part is scratched or cracked, 3D printing can be employed to fill those cracks with a compatible metal material. If the crack is too big to be filled, engineers can use 3D scanners to scan the missing part and 3D print a part that accurately fits. The process is relatively cheap and fast, and this capability would not be possible in any traditional process.
3D Printing at Ports and On-board
Traditionally, the production of parts and components required for servicing any vessel is done inland and supplied to the required location, like a port or a dock. In such situations, the logistics and repair can take weeks. In cases where a vessel needs emergency repair while at sea, the vessel has to dock at the nearest port. During such situations, a vessel may remain stuck at the port for weeks while the necessary part is manufactured and shipped to the site.
This delays the shipment and can lead to greater losses to all relevant stakeholders. To avoid such costly situations, companies are exploring options to install a 3D printer on-board. With a 3D printer on-board, any part can be manufactured on-demand and installed to avoid dire consequences without affecting the delivery timelines.
Opportunities lie in exploring options like installing a 3D printer on-board or establishing 3D printing hubs at ports.
Customization
Another important aspect of 3D printing is its capability to rapidly create customized parts. 3D printing offers complete design and manufacturing freedom, so any part, no matter how complex, can be 3D printed. This customization allows manufacturers to build more efficient, durable, and cheaper parts that also use less material and generate less production waste.
Spare Parts
The maritime industry spends billions of dollars on spare parts and repairs annually. More than 50% of vessels are more than 15 years old, and the need for spare parts increases every year. Moreover, the spare parts are limited and finding them can be difficult, time-consuming, and costly.
To address these inefficiencies, 3D printing is the ideal solution to serve the vessels better, faster, and cheaper. By 3D printing spare parts on-demand, the costs of carrying inventory will be reduced while at the same time the spare parts will be available for every requirement in as many quantities as required. Potential applications for spare part manufacturing are being explored in many sectors, like consumer appliances, oil and gas, defense, aerospace, and other manufacturing sectors.Ā
Case Studies
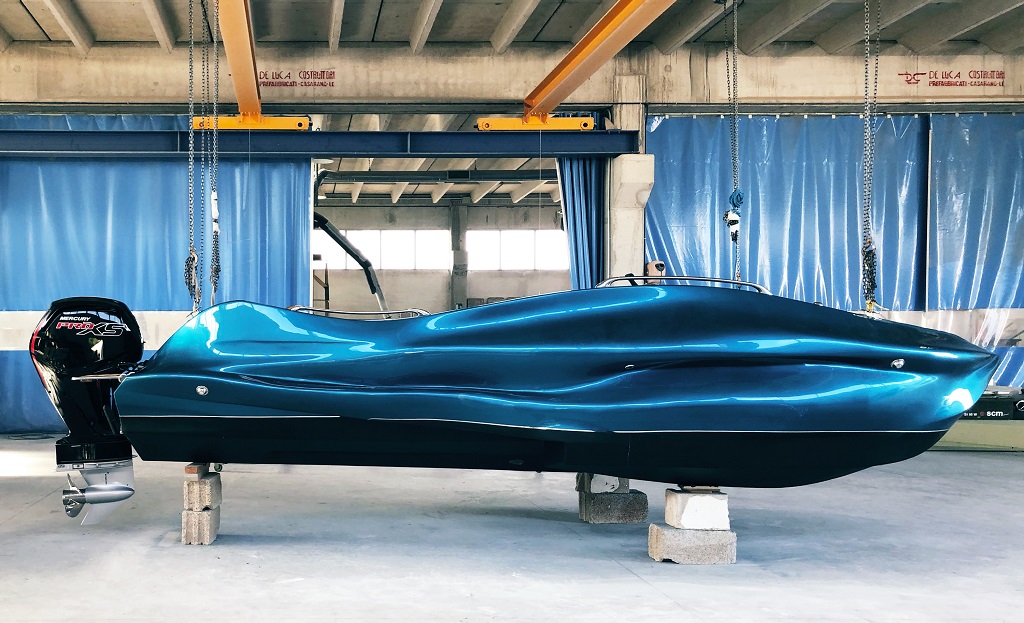
While in theory 3D printing technology seems to be a perfect fit for the maritime industry, here are some recent case studies that show how it is being incorporated around the world.
Spare Part Manufacturing
Last year, Wilhelmsen and thyssenkrupp entered into a collaboration to establish a 3D printing joint venture focused on the maritime industry. The venture will re-examine and optimize the production and delivery process of 3D printed spare parts for the unique demands of the maritime market.Ā
As part of an exclusive early adopter program for 3D printed marine spare parts, Wilhelmsenās Marine Products division revealed that six customers have already signed up for the program to begin utilizing on-demand 3D printing. This will help the customers to eliminate physical inventory, storage, and distribution.
According to Abhinav Singhal, Director of thyssenkrupp Innovations, āWe are already seeing a very positive response from our maritime customers on the additive manufacturing adoption. They are realizing the benefits from faster lead times, reduced costs, and having more resilience in their spare parts supply chain. This is going to be a true game-changer for the maritime industry.ā
Along with the collaboration with thyssenkrupp, Wilhelmsen continues to work with Ivaldi Group on a number of 3D printing software applications.
Repair of Turbocharger Nozzle Rings
Tru-Marine, a turbocharger specialist, revealed in 2015 that it developed a proprietary additive manufacturing process to repair turbocharger nozzle rings. Through the process, the company claims the damaged nozzle rings can be reclaimed to a ālike-newā condition in a fraction of the time required by conventional repair methods.
The company states that it achieves near-perfect densities of greater than 99.5 percent. This can be done using multiple metal alloys or exotic materials to improve the physical properties.
3D Printing a Yacht Hull Mold
Thermwood Corporation, an Indiana-based company that develops, manufactures and distributes technology-based products, used its LSAM technology to 3D print a yacht hull mold measuring 51 feet. This massive hull showcases how only a single mold may be needed for the manufacture of larger vessels.
MAMBO the 3D Printed Fiberglass Boat
At the Genova Boat Show 2020, Moi Composites, a startup that 3D prints products with composite materials, showcased its capabilities by 3D printing an entire boat, MAMBO, from fiberglass.Ā