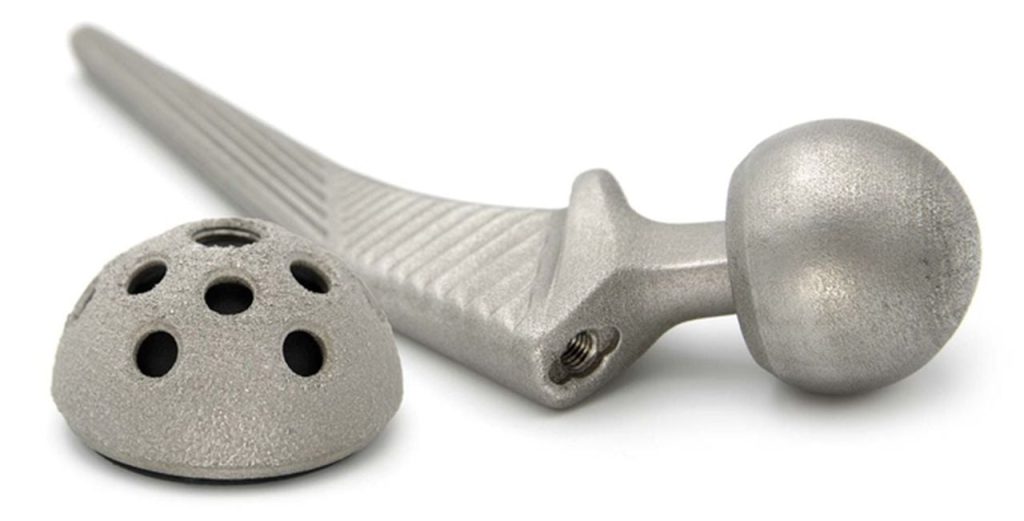
Charles R. Goulding and Preeti Sulibhavi look at the surge in medical 3D prints after the pandemic.
Due to the global Coronavirus pandemic, many people delayed their elective surgeries. Elective surgeries include hip and knee replacements as well as other procedures including cataract operations. This has led to pent-up demand for such procedures.
A recent Wall Street Journal article, published on November 14, 2022, covered this topic and highlighted how supply chain challenges and inflation are affecting the healthcare industry’s ability to meet this surge in demand.
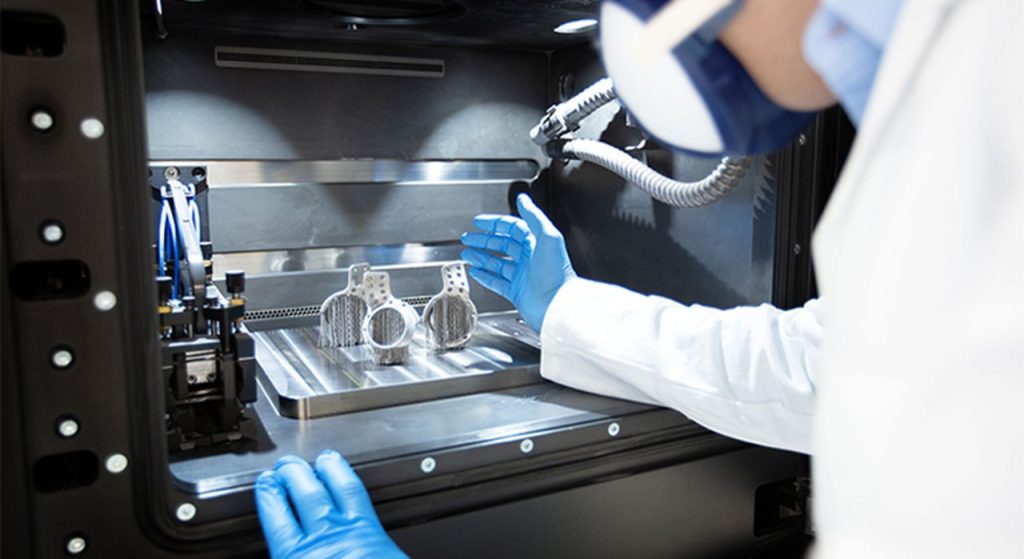
Titanium is one of the few metals accepted by the human body in terms of our bodies not rejecting the material as being “foreign.” Medical implant technology has developed vastly in recent years. One technology is set to transform the way we treat people. Medical implant developers require a manufacturing technology that delivers speed, individualization and the ability to produce customized, patient-specific, and complex designs. 3D printing, paired with materials like titanium, can help achieve these benchmarks. As the medical industry’s manufacturing technology of choice for life-changing solutions, 3D printing is the clear solution to overcoming these challenges.
Kajsa Björklund, Director Technical Operations at OssDsign. “Titanium, with its proven biocompatibility, is a natural choice of material for a medical application such as ours – and additive manufacturing makes it possible for us to design and manufacture unique implants for each and every patient in need of a cranial reconstruction”.
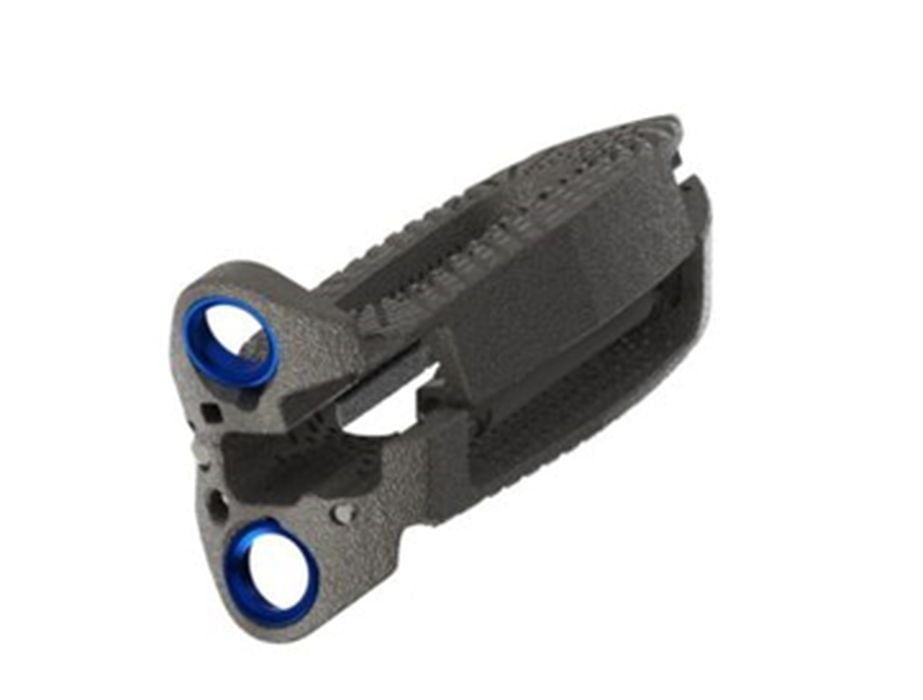
The WSJ article cited that supply chain shortages in the medtech industry have been adversely affecting sales for companies such as J&J’s Abiomed, Abbott and even Stryker, a maker of high-quality surgical equipment. We recently covered how J&J acquired Abiomed, which could effectively increase the usage of 3D printing in the industry.
We were struck by the candid way in which J&J’s medtech unit director, Ashley McEvoy, stated that the medtech industry has not been “pace setters relative to other industries,” in terms of logistics. In our view, expanded 3D printing capability is now a logistics planning tool.
“We’re all going through a major modernization in our supply chains,” Ashley McEvoy, continued. “We have not been pace setters relative to other industries. We’re going to have to get masterful at logistics.”
Stryker is known for its unique, customized and advanced systems for orthopedic and other medical applications. 3D printing is no stranger to the medtech giant, as it has recently launched the Monterey AL interbody system which is the latest addition to its 3D printed interbody device portfolio. Stryker is accustomed to creating porous materials using 3D printing. Its proprietary AMagine process uses additive manufacturing to create implants. Stryker in August announced the official opening of a 156,000-square-foot 3D printing facility in County Cork, Ireland, that will bring 600 jobs to the area.
Monterey AL includes both solid and porous structures. It uses Stryker’s proprietary “Tritanium” in-growth technology. Tritanium is a material that mimics cancellous bone to provide an environment favorable to bone regeneration and fusion. According to Stryker, data showed that undifferentiated stem cells grown on Tritanium exhibited osteogenic alkaline phosphatase with no need for growth factor supplements.
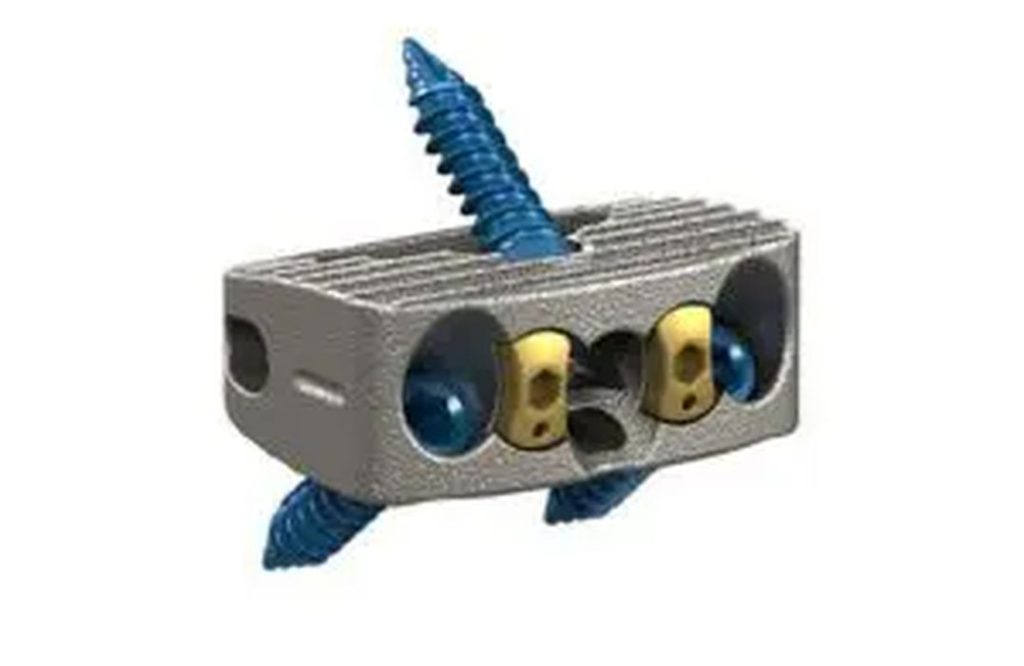
3D printing can help these medical device companies achieve their sales targets and meet the surge in demand for elective surgeries now. There are many reasons to believe that 3D printing can help circumvent supply chain shortages. Whether it is 3D printing’s expedient way of fabricating customized objects with complex geometries, or its flexibility with material selection, there are a myriad of ways the medtech industry can benefit from 3D printing.
The Research & Development Tax Credit
The now permanent Research and Development (R&D) Tax Credit is available for companies developing new or improved products, processes and/or software.
3D printing can help boost a company’s R&D Tax Credits. Wages for technical employees creating, testing and revising 3D printed prototypes can be included as a percentage of eligible time spent for the R&D Tax Credit. Similarly, when used as a method of improving a process, time spent integrating 3D printing hardware and software counts as an eligible activity. Lastly, when used for modeling and preproduction, the costs of filaments consumed during the development process may also be recovered.
Whether it is used for creating and testing prototypes or for final production, 3D printing is a great indicator that R&D Credit eligible activities are taking place. Companies implementing this technology at any point should consider taking advantage of R&D Tax Credits.
Conclusion
The medtech industry is seen as the future of manufacturing in America. 3D printing has been and will be a critical factor in the success of this industry in the US. Especially now, with inflation and supply chain shortages, 3D printing is becoming the clearer answer each day.