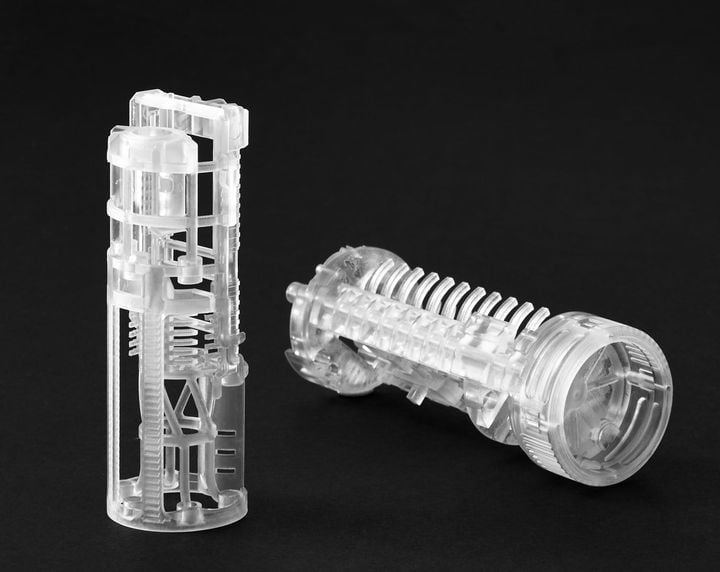
I’m reading a piece on Shapeways’ blog entitled “Will Additive Manufacturing Replace Conventional Manufacturing?” and have some thoughts.
At first glance, the question is preposterous: additive manufacturing can never replace traditional manufacturing. It’s too slow, too expensive and too complicated.
Or is it?
Stephanie Leonida says in the Shapeways piece:
“Despite the benefits of AM, there are various factors that hold back its full adoption as a standard manufacturing process, especially for mass production. As previously mentioned, although the technique is highly efficient at product design and redesign, the time taken to actually print the part required can be second best compared to what injection molding can achieve. For mass production, AM simply would not hit the mark.”
This is most certainly true at the moment, and I generally agree with the other points she makes in the story. However, I wondered what might have to change in order to alter that answer.
Barriers To Additive Manufacturing
The barriers to mass manufacturing use of additive are pretty well-known at this time:
- Speed: The production time per part is fantastically higher with additive approaches, as some purpose-built traditional devices can produce 100,000s of units per day
- Cost: The cost per part is notably higher with additive, although the break-even line is slowly shifting over time
- Material Choice: The choice of materials for additive production is significantly lower than for traditional approaches
I could argue that the first two barriers, speed and time, are really the same thing. Consider the acquisition cost over, say, five years, of a production machine that produces 1M units per week vs a slower additive system that produces 25,000. The acquisition cost per produced part over those five years differs by a ratio of 40!
Advantages Of Additive Manufacturing
And with those, you’d think there is no future. But there are the advantages of additive approaches:
- Complexity: Objects of arbitrary complexity can be easily produced, leading to post-production efficiencies and cost savings in some applications
- Flexibility: Production can start far faster as there is little to no setup time required, as opposed to traditional manufacturing.
Future Shift To Additive Manufacturing
Will this equation ever change? I think it could, but in different ways.
There’s first the obvious effect of technology progression. As time passes, we continually see more rapid additive solutions. A twelve-laser system works a lot faster than a two-laser system, or a higher-volume device can make more units per job, for example. Those incremental changes will continue to pile up over years, but that alone will not cause 3D printers to meet or even closely approach traditional manufacturing’s speed in my lifetime.
That speed increase will, however, increasingly light up low-volume production business cases. Depending on the scenario, the break-even point will continue to rise. When the cost is the same, the flexibility advantage of additive will tip the decision balance.
There are other things that might happen to alter the equation.
One might be the surprising development of new forms of 3D printing processes that could lead to massive speed-ups in production. I can’t say what they might be, because they haven’t happened yet. However, research continues all over the world seeking new ways to make objects.
One very promising approach is the volumetric 3D printing concept that several parties are now developing in their labs. This technology, if it works and allows for the use of suitable materials, could speed up production by perhaps 100X. That would move the break-even line far, far higher.
There are also certain to be developments in the materials area, where the breadth of material choice for use in additive will increase over time. Today’s catalog of possible materials will be much smaller than that of five years from now, and so on.
Another factor that could increase use of additive approaches is not a technology at all, but a behavioral effect. Today we are all accustomed to receiving parts in uniform designs and sizes.
This was a solution to a need early in the industrial revolution, where hand-crafted parts were generally not interchangeable. By making parts in standard designs, much utility was gained. Mass production approaches perfected this concept by doing so at scale.
But do we actually need uniform parts all the time? What if consumers became accustomed to personalized “parts” for their needs?
This effect might begin with 3D printed shoes, for example. But having experienced customization in one product, consumers might come to expect the same in other products. And a world full of consumers expecting customized products is a world that is just a few steps away from making most things in customized form.
I cannot say whether this reaction would occur, but it’s definitely something that we may see early signs of in today’s production.
Via Shapeways