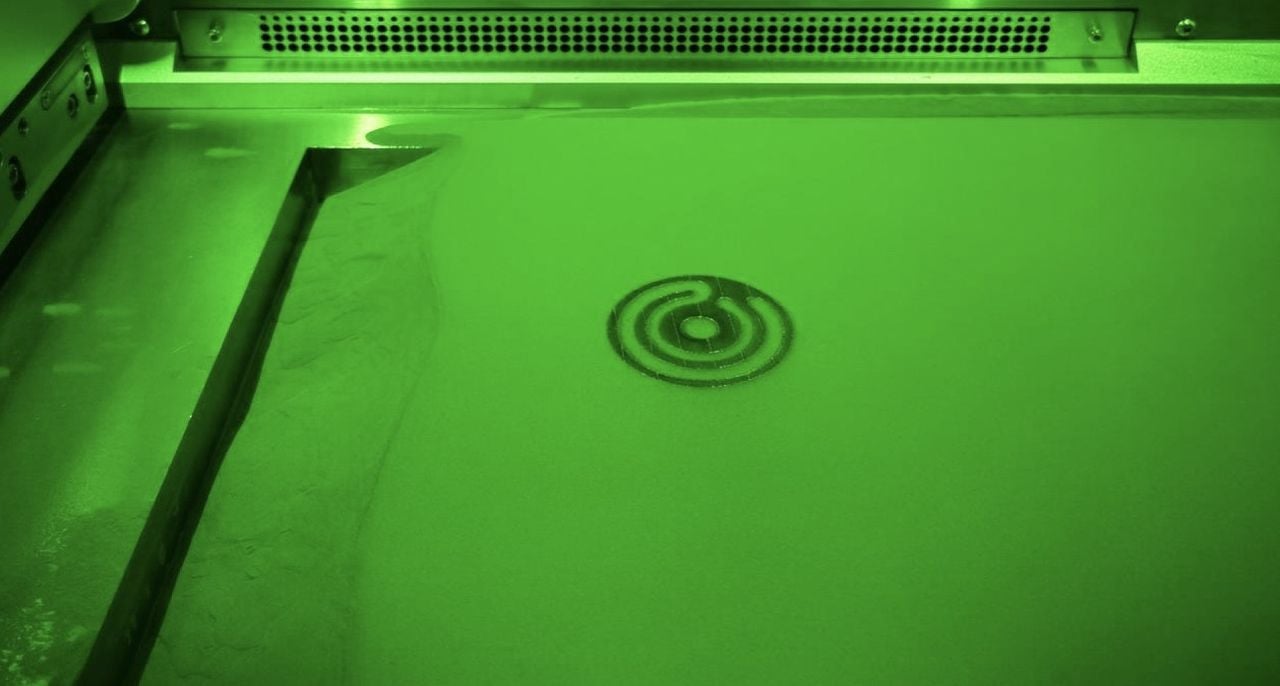
Eplus3D introduced a very interesting metal 3D printing feature they call “One-Click Positioning”.
The need for this feature is derived from challenges facing those using hybrid metal manufacturing processes and equipment. A hybrid setup usually is composed of a metal 3D printing element combined with a CNC milling element.
Such hybrid equipment can be used to produce production-ready parts with a two step process. The 3D printer element deposits several layers of metal, but due to the technology the surface quality is usually terrible.
That’s where the CNC milling element takes over, as it can quickly smooth the layers to the precise dimensions and surface quality required. Typically this is done every few layers of 3D printing.
Hybrid 3D printing uses far less metal material than would be used in a typical CNC-only process, but results in pretty much the same part.
These hybrid systems have also been used to “add” material to existing parts. In other words, a metal part is placed in the machine and the 3D printer will deposit metal on selected portions of its surface. Then the CNC mill will smooth it out, just as it does when producing a new part.
But there is a key problem: when you place a part into the machine, how, exactly, does the machine know where it is? This is critical information because the 3D printer toolhead and CNC mill must move to the exact locations in 3D space to deposit and mill the added material.
Eplus3D explains the problem in more detail:
“The most critical and difficult step is how to accurately position the additive layer information to the existing pre-form. The working area should completely coincide with the substrate, otherwise misalignment will occur and for example cooling channels that run through both areas of the final part won’t achieve the desired function. The misalignment of complex parts is likely to cause the parts to fail to meet the design requirements, that is, effective hybrid manufacturing with a dimensional tolerance of less than 0.1mm.”
That is indeed a difficult problem, and without a solution, this type of hybrid manufacturing is essentially impossible for most complex parts.
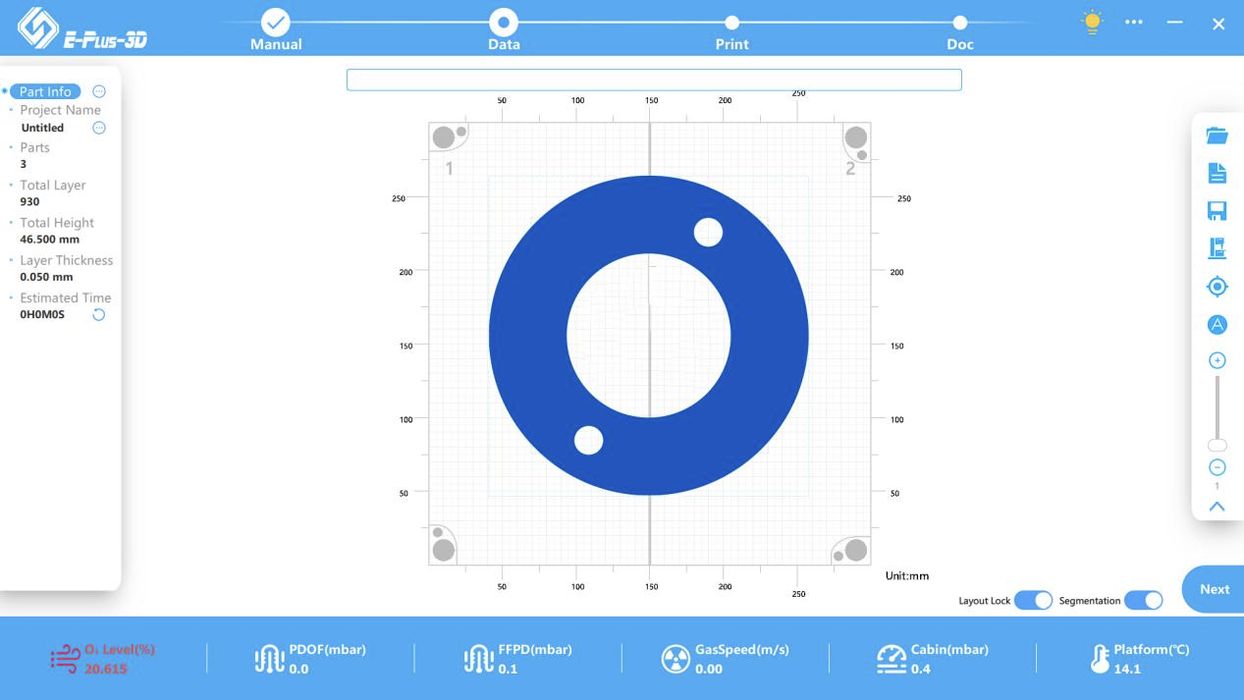
However, Eplus3D’s “One-Click Positioning” does this automatically. They explain:
“The software automatically calculates the position information of the parts to be hybrid manufactured by collecting the images of the parts and obtaining the contour map of the parts, then returns the position information of the parts to the printing equipment to realize intelligent hybrid manufacturing and improve the efficiency and accuracy of parts.”
This is a very important feature, as it will allow hybrid operators to almost literally toss a part into the machine and begin printing & milling. That should encourage increased use of the technology for the production of metal parts in the future.
Via Eplus3D