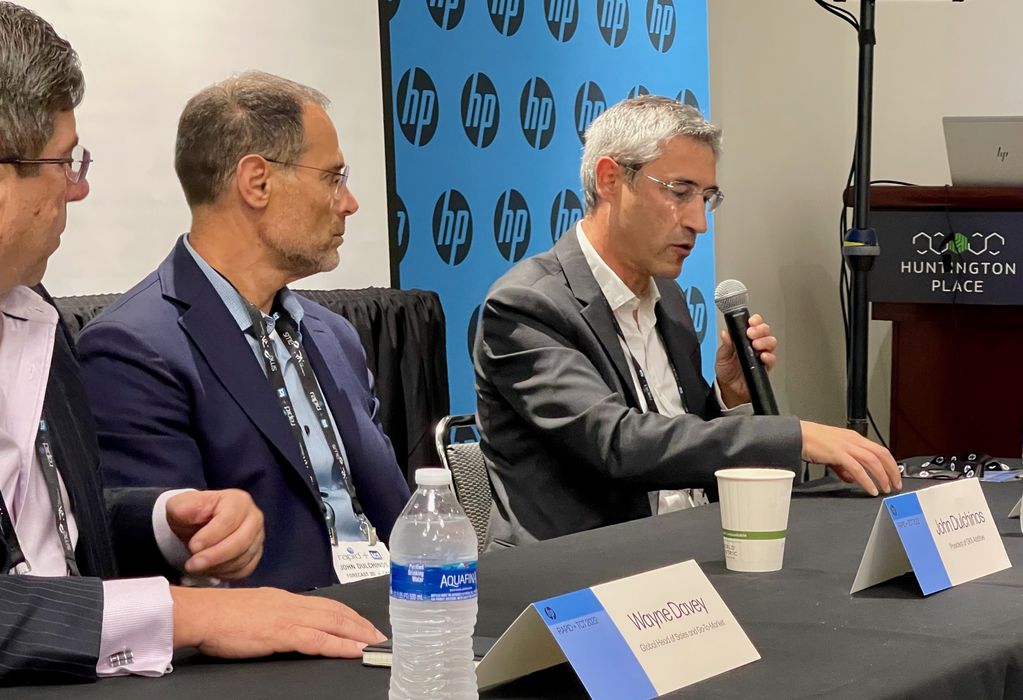
I sat in on a discussion with HP executives and users to learn more about the company’s work with industrial additive manufacturing.
HP has a very long history in 3D printing, although some may think they are relatively new on the scene. In fact, they were marketing rebranded Stratasys equipment more than ten years ago, enabling them to quickly enter the space and gain knowledge.
That knowledge was later transformed into their own 3D print technology, MJF, which is targeted at production manufacturing. HP has since announced a series of machines, each offering different capabilities. They now offer equipment that can produce low volumes of polymer parts, even in color, and soon will offer metal 3D printing capabilities.
But making the equipment available is only the first step. You have to have buyers and users of the equipment, too. That seems to be the stage of HP’s evolution, where they are working with contract manufacturers and manufacturers directly to persuade them of the advantages of their MJF process and additive manufacturing in general. It seems at the moment HP is focusing on the automotive industry.
HP’s largest installation of MJF gear turns out to be at GKN Additive, located in Carlsbad, California. Apparently they have around 40 MJF machines, the largest single concentration of HP 3D printers on the planet.
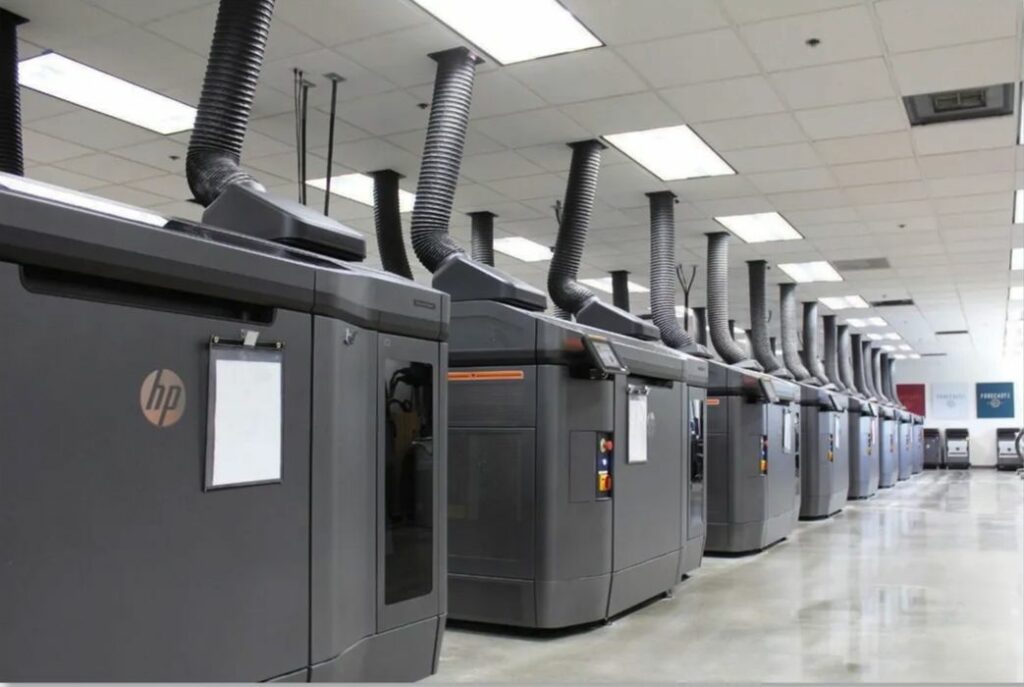
HP’s Global Head of 3D Printing Solutions Go-to-Market, Wayne Davey, explained:
“There are not yet many times AM is the whole solution for an application, but increasingly it is part of the solution.”
As an example, Davey related a scenario that recently occurred at GM: a late-in-the-process design change to a rear spoiler closeout seal threatened to hold up the delivery of up to 30,000 vehicles. This delay would have been caused by waiting for the traditional manufacturing process to get up to speed to produce the new seal design. That’s not a good scenario.
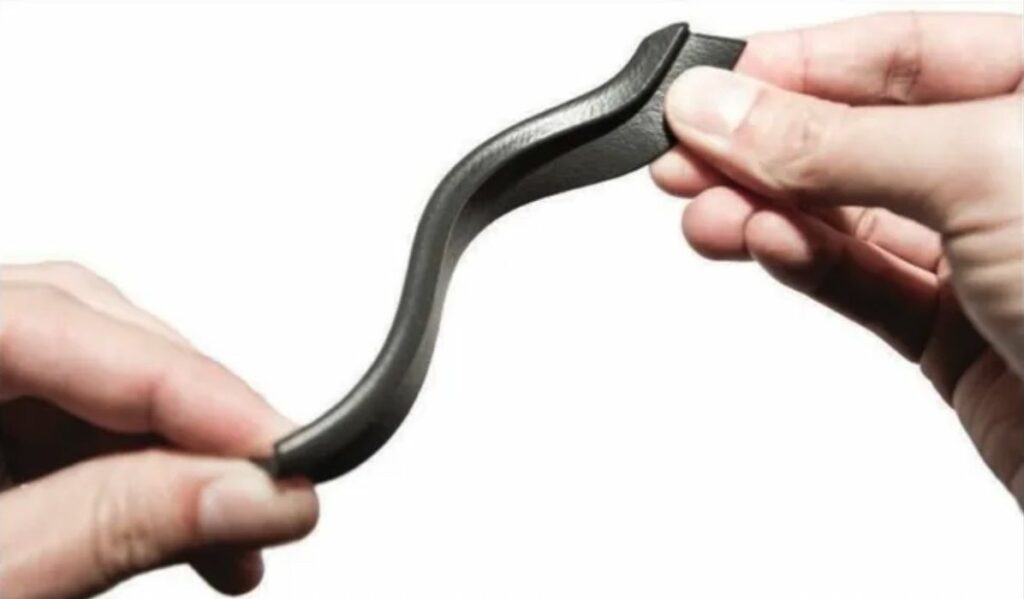
The solution was to switch to additive manufacturing, at least for GM’s immediate needs. They contracted with GKN Additive to quickly produce and post-process the necessary redesigned seals using HP’s MJF equipment. The results were comparable to normal injection molded parts, and allowed GM to continue shipping the vehicles on time. Meanwhile, GM could establish traditional manufacturing for the new seal in parallel with the emergency 3D prints.
These emergency parts were no doubt more expensive per unit to produce than with traditional methods, but they got the job done on time.
It seems to me that in this scenario, speed trumped cost, but to use even more additive technology in the future, costs will have to com down in order to persuade more manufacturers to use the technology. GKN Additive’s President John Dulchinos said:
“Companies want finished parts, not printed parts. The next generation of binder jet technology will be a huge step to delivering cost savings. We’re cutting the number of manufacturing steps to get near net shape parts.”
While speed is important, quality is mandatory. HP’s Ramón Poster said that it’s always quality over speed.
Poster pointed out the challenges of metal manufacturers to transform their operations into additive:
“Some companies don’t have huge investment capital around to transform themselves. They have to schedule the scaling, and this has investment implications.”
For many of these companies, the best initial option would be to contract work to a third party that has the equipment and expertise to perform additive production. Davey added:
“It’s hard to buy a fleet of 3D printers for time limited project.”
Dulchinos believes this could be the future, saying:
“We purchased twelve machines without having a customer application for them, but these customers slowly started to arrive. Our challenge is more about having the agility to ingest a wide variety of customer applications. This requires different skills, processes and software to achieve.”
Indeed, the transformation to additive is extremely challenging, and use of a third party contract manufacturer can often be the right decision. Later, when a company is more experienced and confident of the approach they could consider their own in-house operations. HP definitely realizes this and is addressing that market.
Via HP and GKN Additive