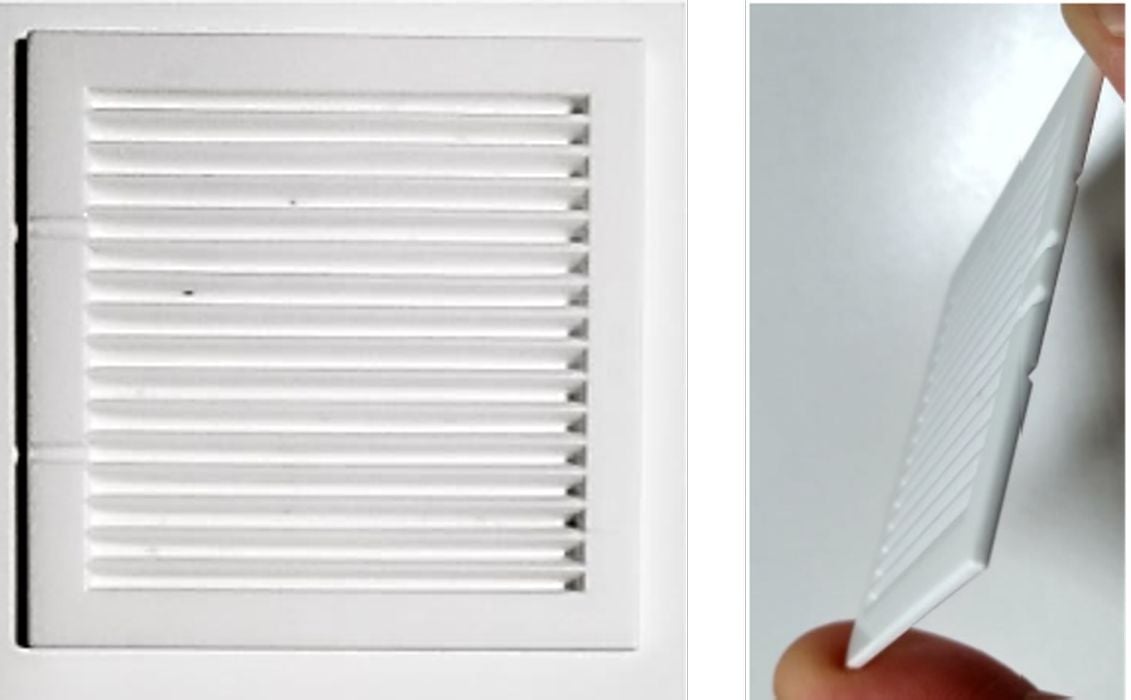
3DCeram is participating in a rather interesting green project to produce hydrogen.
The French company has been developing ceramic 3D printing solutions for at least 15 years, and their current product set includes seven different ceramic 3D printers, as well as multiple ceramic materials to print in them.
Theyâre participating in the HyP3D project, a European initiative to develop methods of producing âgreen hydrogenâ.
Wait, isnât there just one kind of hydrogen? Itâs the simplest molecule, after all.
It turns out there are different classifications for hydrogen based on the method of their creation. âGreen Hydrogenâ is hydrogen (yes, that same molecule) that was produced with entirely green and sustainable processes, such as renewable wind or solar power.
There are two other classifications. One is âBlue Hydrogenâ, which is produced using liquid natural gas (LNG). The LNG aspect might at first sound not so environmentally friendly, but hear me out. The LNG, or methane, is exposed to hot steam, which produces hydrogen and CO2. The CO2 is captured and stored, taking it out of the environment.
Then thereâs âBrown Hydrogenâ. Thatâs made directly from coal, and the process to do so releases both CO2 and CO into the atmosphere. Brown hydrogen is the bad one of the three.
Itâs important to know what kind of hydrogen is being used in an environmental project. For example, if someone said âweâve got a hydrogen-powered trainâ, you also have to ask where they go their hydrogen from. If itâs brown, then whatâs the point? CO2 is still released.
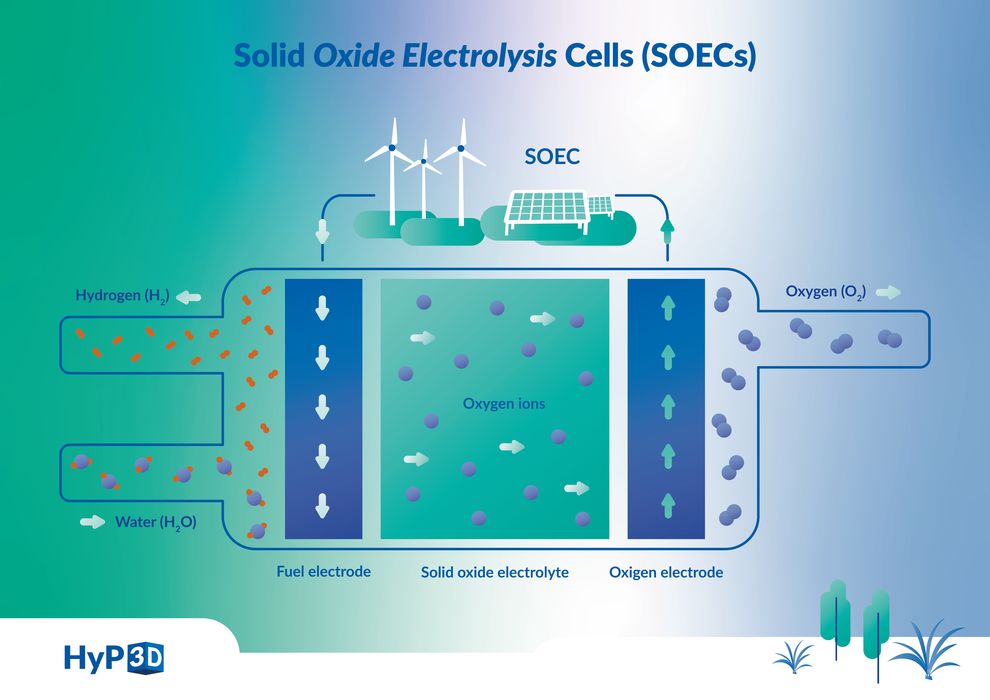
Back to the HyP3D project, which hopes to develop a way to efficiently produce green hydrogen using the solid oxide electrolysis cell process (SOEC).
The key to SOEC is to produce 3D printed SOEC cells that offer high efficiency and scale. The project hopes to be able to offer power output of 2.14kW within a mere 630 cubic centimeters.
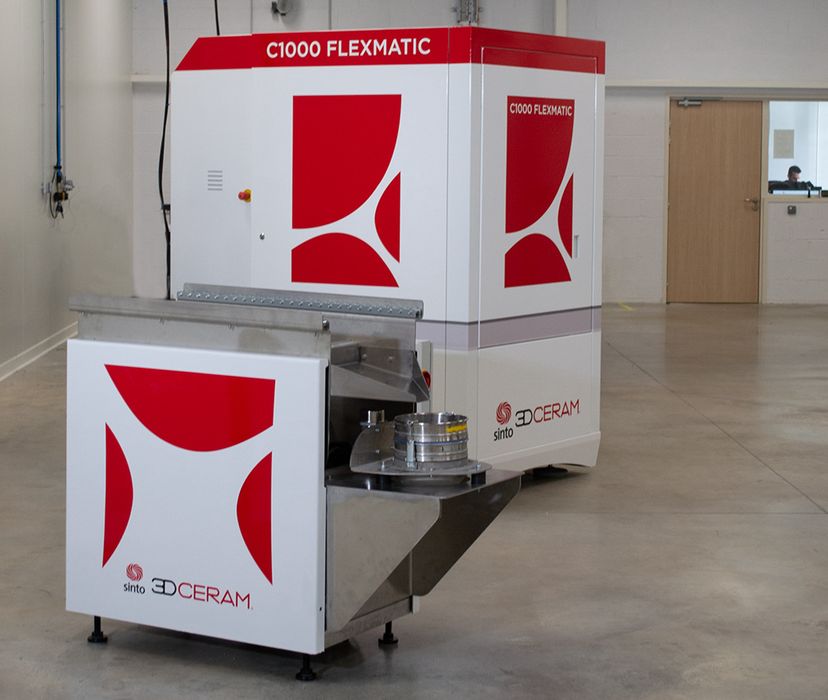
3DCeram will be working on the project to determine materials, printing parameters and post processing activities. They intend to use their existing C1000 Flexomatic system to do the printing.
This is yet another project demonstrating the achievement of a new function that could not be done without the use of advanced 3D printing technology.
Via 3DCeram