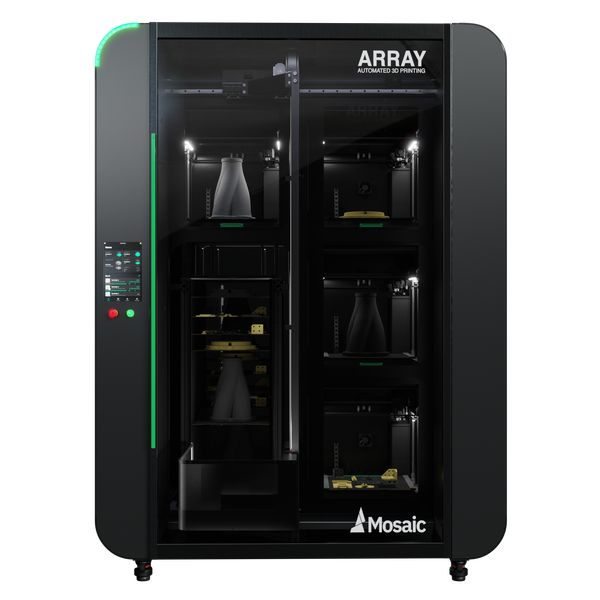
In discussions with Mosaic Manufacturing I learned more about their revolutionary “Array” 3D printing factory.
If you haven’t heard, the Toronto-based company suddenly announced a series of products that vastly altered their position in the market, which we described earlier. From a manufacturer of 3D printing accessories (the Palette), they are now the maker of industrial 3D printers. Quite a leap!
Mosaic Array Production
The Array is a fascinating device, and it seems Mosaic Manufacturing put quite a bit of thought into its design. The story is that some three years ago they commenced design of the system, which has remained a complete secret until the big announcement today.
Why make such a massive leap in products? Evidently their Palette device was the original driver.
The Palette is a standalone device that sits between a single-nozzle FFF 3D printer and spools of filament. The Palette examines GCODE to detect when color changes are required. It then accesses up to four attached spools and literally cuts and splices a custom filament on the fly for the 3D printer to use. The cuts are spaced perfectly to effect instant color changes throughout the print job.
Many Palette users are hobbyists who use the system to print multi-color objects. However, Mosaic Manufacturing also observed another use for the Palette: filament management. They had several industrial and professional clients who would use it as an easy way to switch spools without incurring much labor cost.
After some further investigation, Mosaic Manufacturing determined there was an opportunity to capitalize on this concept, and that was the genesis of the Array.
Mosaic Array
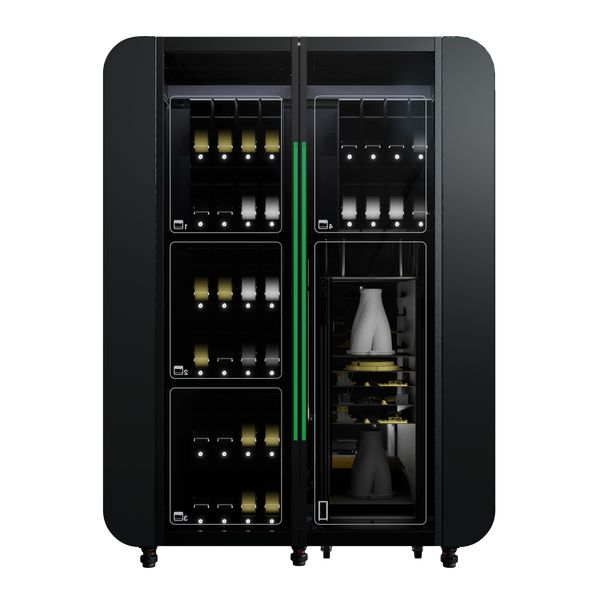
The Array is essentially an automated 3D printing system. It includes:
- Four large-volume, high-temperature Element 3D printers
- Embedded Palette X units on each printer allowing up to eight filaments per nozzle
- A robotic system to load and remove print plates after job completion
- A movable cart to accept completed print plates
- A rear spool stowage area containing 24 Material Pods, each holding a filament spool
- A load of fresh print plates, apparently several dozen per Array
- Canvas software to dispatch jobs from a queue submitted by multiple users requesting printing services
Mosaic Array Operation
In operation, the prints are dispatched by Canvas, and then run on a specified 3D printer. During printing any filament from the attached eight spools can be used without operator intervention. This means not only multi-color, but also support materials, different material types, etc. The key here is that no intervention is required.
After the job completes, software directs the robotic system to pick up the print plate — which is a powder-coated spring steel plate — and place it “cafeteria tray-style” in the pickup cart. Note that the “trays” can be placed “two deep” in the cart.
Mosaic Manufacturing says the system is designed to allow for a MINIMUM of 72 hours continuous operation without requirement for any human operator. At the conclusion of the run, an operator can roll away the cart full of completed print plates for final post-processing.
A good way to think about this is that the Array is a “black box”: you toss some print jobs at it, and it runs until it completes them all or runs out of capacity. That capacity turns out to be the number of plates you can store in the cart.
Mosaic Array Capacity
There’s a very curious effect with the cart concept. You might recall that the build volume of the Element HT 3D printers is 355 x 355 x 355 mm. This means a random print job might build objects that are as high as 355mm. In that case the plate slots in the cart would have to be spaced at least that far apart vertically.
But it turns out that’s not how it works. Mosaic Manufacturing recognized that print jobs will have wildly varying heights, and assuming all jobs will be 355mm tall would waste a tremendous amount of space in the cart.
Instead they designed the robotic system to account for varying heights, and so it stacks the cart with plates at varying levels to optimize storage. For example, if you had many print jobs with “low” objects, the Array could stack many more completed plates in the cart.
The implication here is that the the Array can run unattended for far longer than the 72 hours mentioned above, and typically would do so because few would be printing 355mm objects all day long. It’s likely the Array can run for many days, perhaps even a week without interventions.
Mosaic Array Materials
I learned some other interesting trivia about the Array system:
It’s possible to swap Material Pods while the Array operates, essentially eliminating the possibility of running out of material, which is already unlikely. This would only occur if you had a specialty filament with few spools in the 24 allocated.
The filament is provided by Mosaic Manufacturing in sealed, dried form, as one would expect. After opening the package, the filament spools are placed directly into the Material Pod where they will remain dry.
Mosaic Manufacturing sells and measures filament quite differently. While most providers specify by weight, here they use cubic centimeters. This is actually more representative of what you’ll get from the purchase, as some materials have radically different densities. However, this measurement scheme could make operation a bit challenging for new Array users. Currently they’re intending on selling spools for the Array in 700cc and 1500cc forms (about 2kg in weight).
The print plates are not all the same. Mosaic Manufacturing intends on producing several different types that are optimized for specific materials. Presumably the robotic software will match the plate type to the job to ensure proper operation.
Mosaic Array Cost
Array buyers will be charged US$59,999 for a standard configuration, but there are some options. While each Element 3D printer will offer a heated chamber, it will be possible to select non-HT hot ends if they are not required. You can also obtain different quantities and types of print plates.
Coming sometime in late 2022 will be a scaled-up version of the Array, called “Array Production”. It’s basically the same thing except that it will have 24 3D printers instead of only 4. It will come with multiple carts and a heck of a lot more print plates. It’s targeted at operations needing to produce larger volumes of parts.
One type of usage that could be quite popular is university engineering labs, where there are mobs of students needing to submit jobs for 3D printing. The new Canvas software will be able to handle multi-user submissions and centrally dispatch jobs appropriately to the highly flexible Array system. The ability for students to select from many different types of materials will be highly desirable for them and the system’s operator, who won’t need to switch any spools.
At the moment Mosaic Manufacturing has placed a couple of Array units at friendly customers where they are undergoing evaluation. The intention is to offer the Array to the public late this year.