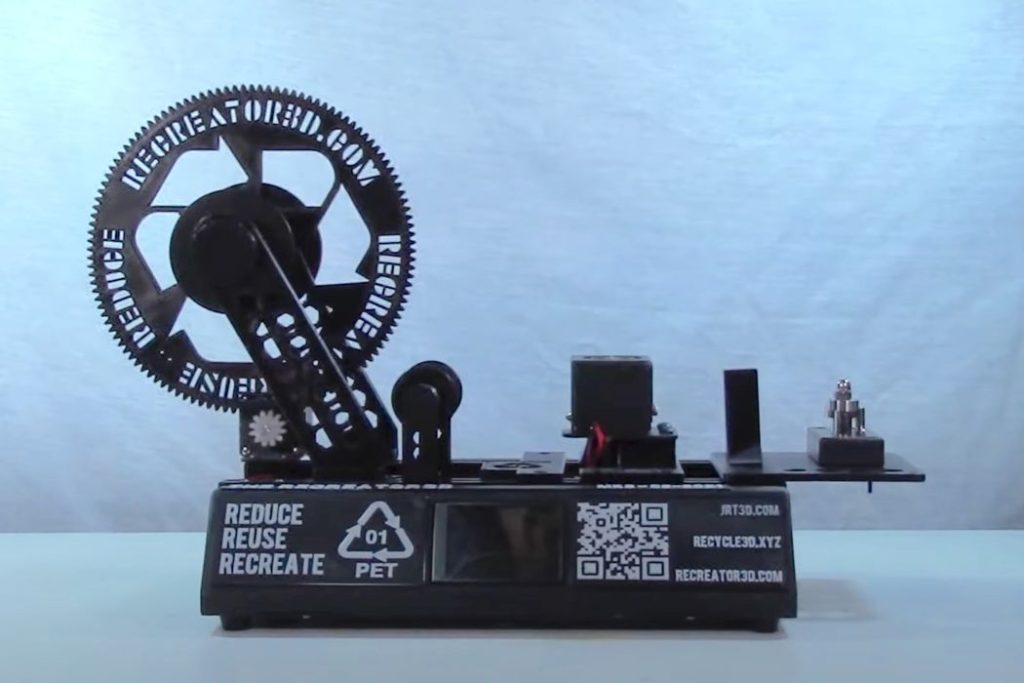
I’m looking at an interesting open source hardware project, the ReCreator 3D.
The project is one of several small-scale initiatives to provide a more sustainable solution for 3D print materials. In short, it’s a machine that can transform a waste drink bottle into 3D printer filament.
Drink bottles are ubiquitous, and many people use one or more every day. The empty bottles pose a significant source of consumer waste, and often end up in landfills. Many jurisdictions, however, offer recycling programs where bottles can be returned and reprocessed.
That’s possible because the bottles are almost universally made from PET thermoplastic, a commonly used 3D printer material when in filament form.
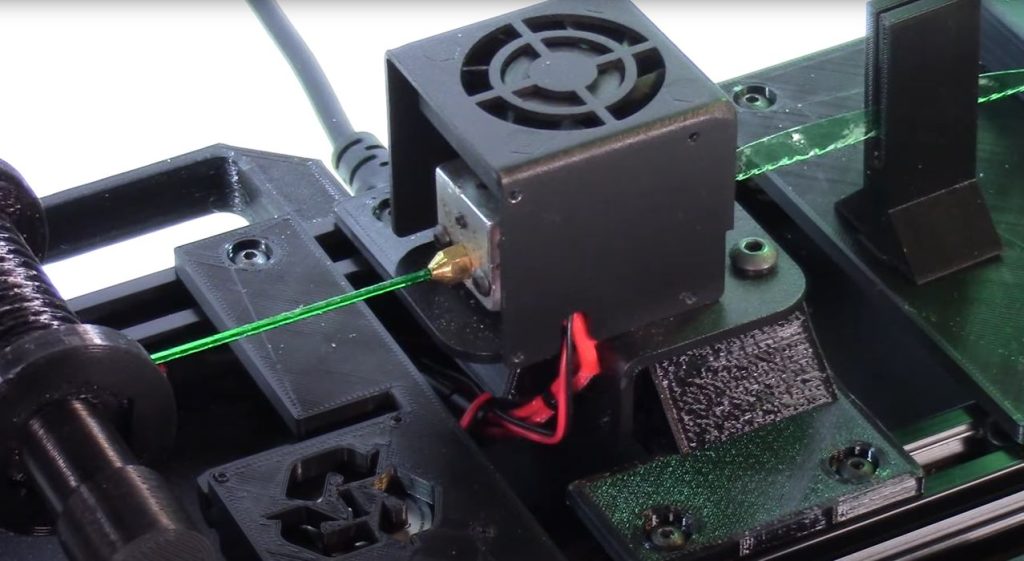
The ReCreator 3D is a device that accepts a drink bottle and peels off a strip while rotating. The strip is pulled into an extruder where the PET softens and becomes proper 3D printer filament.
The system is provided as a kind of conversion kit for leftover desktop 3D printers, which, by coincidence just happen to include a hot end, extrusion system and system controls that could be re-used for the “pultrusion” process.
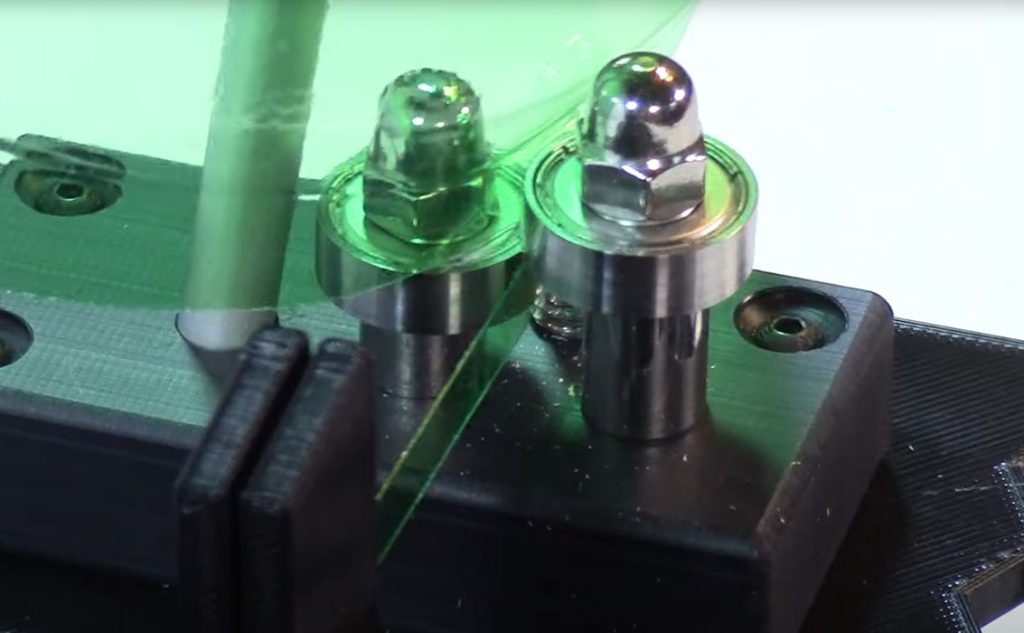
A pair of bearings slice off a precise width of drink bottle as the bottle is rotated. This presumably ensures a more or less consistent amount of material to enter the hot end. However, the system works only for the “middle” part of the drink bottle, because the top and bottom have different geometries and can’t be sliced evenly. Nevertheless, a portion of the bottle does indeed become 3D printer filament.
Here’s a short video showing how the system operates, once built:
The ReCreator 3D site provides a couple of different versions of the ReCreator 3D, with one being designed for adapting the popular Creality Ender-3 3D printer. The main site includes documentation, advice and the STL files for the required parts. Printable files are also provided on Printables and GitHub.
It seems to be a fairly straightforward build, although there are plenty of steps to complete. This video shows how to build the bottle cutter portion:
It would appear one could use the ReCreator 3D to produce PET filament for 3D printing at low cost: the machine doesn’t cost a lot to build, and the raw materials for filament, leftover drink bottles, cost nothing.
While I am very supportive of any initiative to increase sustainability in any dimension, I do have some concerns about this device.
The problem is that today’s 3D printers expect high quality filament in order to reliably produce quality objects. Many commercial filament providers have disappeared simply because they offered lousy filament. Many times I’ve seen apparent 3D printer problems “suddenly disappear” after switching to better filament.
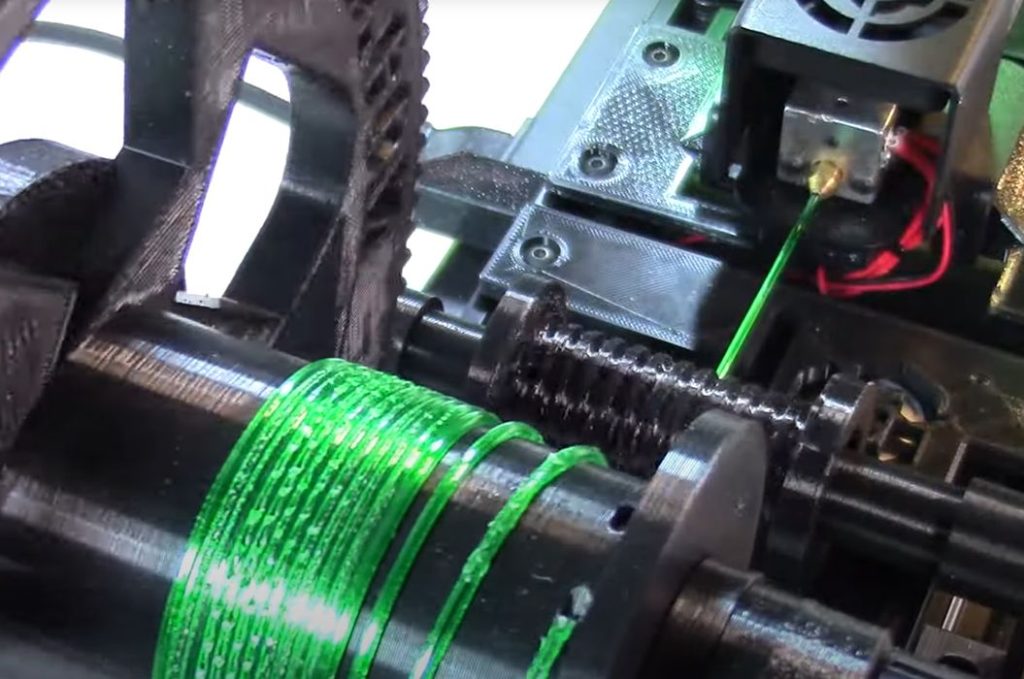
Does the ReCreator 3D produce high quality filament? I don’t believe it can, as the best commercial filaments employ multiple laser sensors continually measuring filament diameter, real time feedback controls to moderate pull speeds, long water baths to slowly cool the filament while maintaining geometry, drying systems, and very precise thermal controls throughout. None of those are present on the ReCreator 3D, and the videos appear to show visible but slight irregularities in the produced filament at times.
However, the filament produced can no doubt be used in certain printing situations, so long as the 3D printer operator is aware of the constraints and possibility of quality & reliability issues. You don’t always need the best filament, it just makes life easier and print quality better.
Another challenging aspect to the ReCreator 3D concept is that the drink bottles must be extensively cleaned before use in the system. This is to remove any contaminants that would pollute the chemistry of the filament, and include labels, label glue, and the bottle’s original fluid contents.
To give you an idea of what it takes to clean a bottle, this four minute video takes you through the process:
The cleaning process makes perfect sense, but my question is, how many 3D printer operators would actually do all that work to obtain a small <100g coil of filament? With high quality filament prices dropping below US$20 per kg, it seems like there could be a perceived cost – benefit issue for many folks. There’s also the issue of the consumables used to perform the cleaning, which themselves create waste.
It would seem that the ReCreator 3D is best for technically-capable individuals that truly want to contribute to sustainability on their own terms. However, that is likely going to be a relatively small portion of 3D printer operators.
My thinking is that recycling of materials is probably more efficiently done in central processing centers, where large quantities of bottles can be made into full, 1kg spools. These can then be marketed just like non-recyclable spools, leaving the choice to the buyer. It’s a lot easier for someone to decide to buy a spool of recycled filament than it is to build a machine, clean bottles and make one’s own filament.
That said, the ReCreator 3D adds yet another way for 3D printer operators to increase their sustainability profile, and it should be an option alongside centralized recycling options.
Either way, we’re going to have to use a lot more recycled materials when 3D printing.
Via The ReCreator 3D