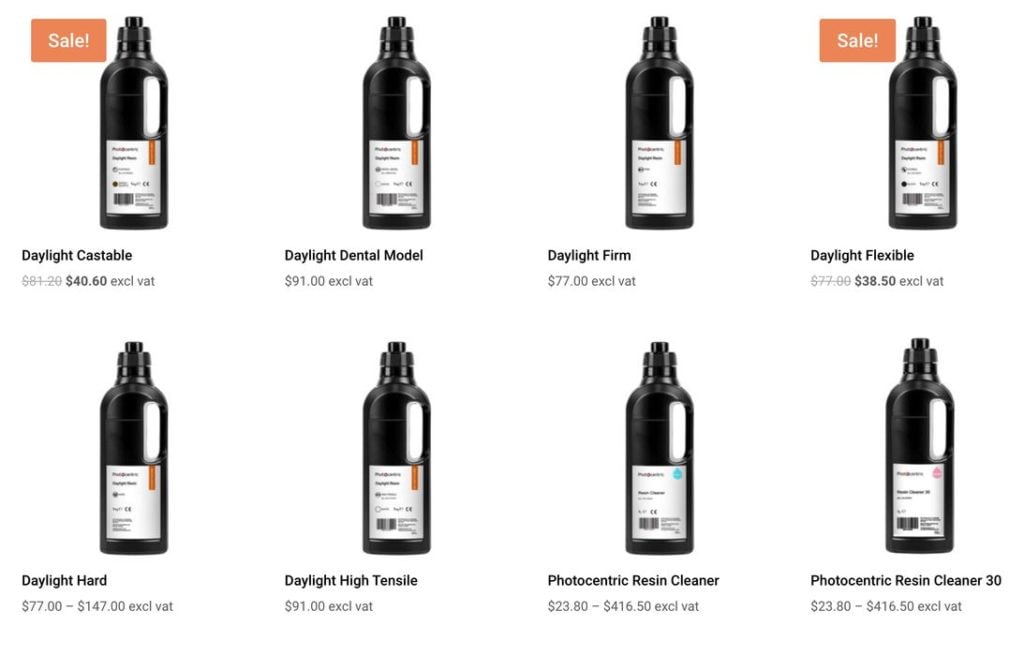
Daylight resin is a rare sight in the world of 3D printing today, but could it become more popular?
Photopolymer resins have been around a long time, and virtually all of them use UV light. Specifically they are tuned to respond (polymerize) when exposed to a very specific range of light frequencies.
The most typical frequency seen is 405nm, but there are a few more. Because of this resin 3D printer operators must ensure the resin they purchase matches the frequency requirements of their 3D printer. If not, prints will remain wet and lack structure. Well, theyâll have no structure at all.
Some years ago I ran across Photocentric, a company thatâs one of the few in the world that directly manufactures photopolymer resin. At the time they were launching their own brand of resin 3D printers, but they had an unusual characteristic.
They used something called âDaylightâ resin. As the name implies, this type of resin responds to typical daylight light frequencies rather than specific UV wavelengths.
Why use daylight frequencies? Years ago I obtained an answer from Photocentric:
âPhotocentric explained that their systemâs very low energy is very different from others who use âfar too much energyâ when blasting UV at the resin. For them, this is what fuses the solidified resin to the tank. In Photocentricâs approach, they use very little energy so the resin solidifies without fusing to the PFA tank. Thus, these inexpensive resin 3D printers should operate very fast, similar to the Carbon3D method. They call the method âDaylight Polymer Printingâ, or âDPPâ.â
Iâm no chemist, but I suspect the daylight resin responds to a wider range of frequencies than typical photopolymer resin.
Whatâs the advantage here, beyond tank adhesion? It turns out there are several. First, the light engine for solidifying daylight resin doesnât have to specialize in unusual UV frequencies. Instead itâs possible to repurpose all manner of conventional light equipment to do the job because they are already designed to emit daylight frequencies. This means it would be possible to develop resin 3D printers with far less expensive light engines, potentially reducing the price of the equipment, or making far larger devices.
Another advantage is the daylight frequencies are completely safe â we live with them everyday. On the other hand, lasers emitting specific UV frequencies can be unsafe in certain situations. In other words, a daylight resin 3D printer should be inherently safer than a UV resin 3D printer.
Thinking about this today made me ask the question, âwhy do we use UV frequencies?â
Is there some specific advantage to these specific frequencies? All light frequencies are sufficiently small to obtain high-resolution 3D prints.
I recall how the early desktop 3D printers used ABS filament, which we now realize is a terrible material for printing unless the machine includes a comprehensive thermal solution, which machines of the day did not.
Why was ABS chosen then? Because it was available: it appeared in every hardware store as âABS welding wireâ. That choice instantly became a widespread source of material for the new machines.
But over time everyone realized that ABS was too hard to print in many cases, and a switch to PLA and subsequently a raft of other unusual materials occurred. ABS is still there, but itâs not the default anymore.
Now Iâm asking myself whether UV resins were chosen long ago simply because they were available? Photopolymer resins have long been used in other industries: your dentist will use them to solidify fillings with UV light, for example.
Was the choice of UV resins made due to market availability?
Are we now at the âPLA Momentâ of resin 3D printing, where other material options begin to be considered by equipment and material manufacturers?
I donât think so, but in coming years such a change might happen when equipment manufacturers realize the advantages of daylight resin.