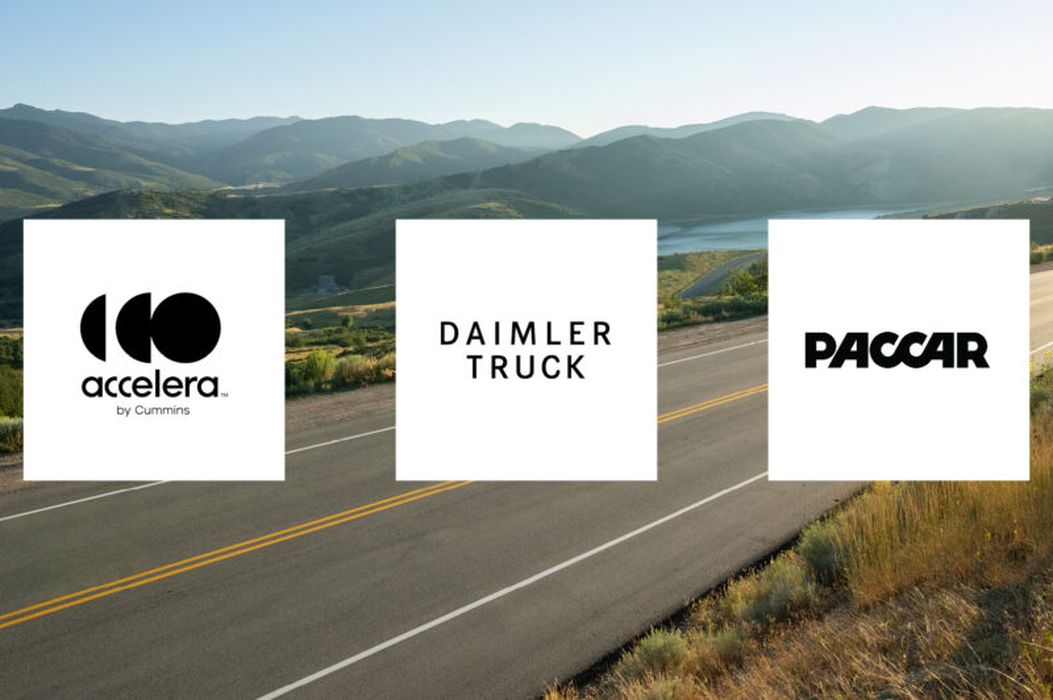
Charles R. Goulding and Preeti Sulibhavi anticipate a surge in electric truck production and how additive manufacturing can assist design and test new fleets more cost-effectively.
Major players in the commercial truck industry are making significant investments in electric vehicle (EV) technology and infrastructure. Diesel engine manufacturer Cummins, along with truck makers Daimler and Paccar, plans to open a US$2 billion battery plant in Mississippi in 2027. The plant will be the largest in the nation dedicated solely to commercial vehicle EV batteries, with an initial annual output enough to power over 40,000 medium- and heavy-duty trucks.
The Mississippi plant represents the companies’ big bet that the freight industry is ready to adopt alternative power sources as new emissions regulations make diesel trucks much more expensive. Sales of electric trucks currently make up a tiny fraction of the over 600,000 commercial vehicles sold annually in the U.S. and Canada. However, stricter state and federal rules on both emissions and sales targets will likely accelerate adoption.
The Mississippi Battery Plant
The 300,000-square-foot facility in Marshall County will produce lithium iron phosphate (LFP) batteries. Chinese battery maker EVE Energy is providing the LFP technology and materials, while also helping Cummins, Daimler, and Paccar develop domestic supply chains. Locating production in the U.S. will lower electric truck costs by improving battery availability.
The plant is expected to employ around 2,000 people. Cummins, Daimler, and Paccar will each own 30% stakes, with EVE Energy holding the remaining 10%. The companies plan to use the plant’s battery cells to assemble custom packs for their own electric truck drivetrains.
Accelerating Adoption of Electric Trucks
California will require 5% of heavy-duty tractors and 9% of other trucks sold in the state to be zero-emissions starting this year. Ten other states will phase in similar regulations over the next three years. The EPA is also considering new carbon emissions rules for trucks that would drive further electrification. Market forecaster ACT Research predicts electric trucks will make up 10% of U.S. and Canadian sales by 2027, rising to over 30% by 2030.
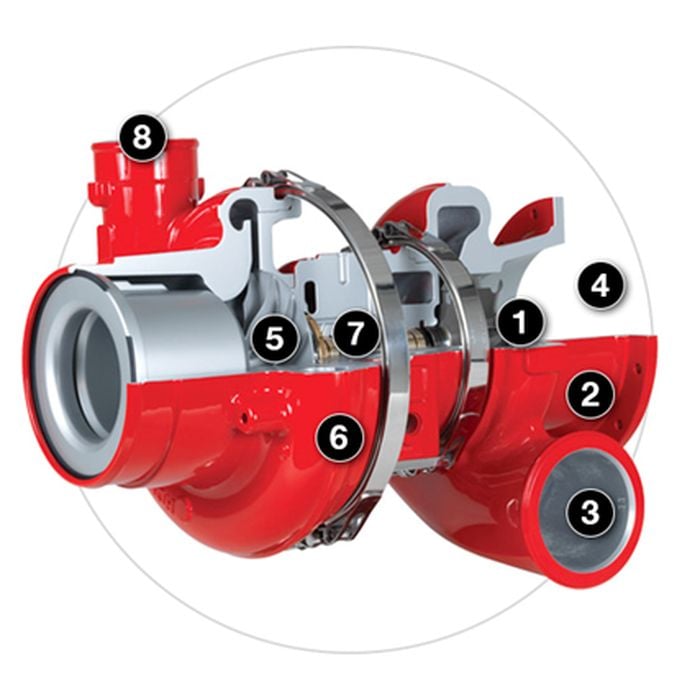
Major Players Push Forward
Cummins (US$54 billion revenue and employed 73,600 people globally in 2023) makes diesel engines for heavy trucks and other vehicles. While still focused on diesel, Cummins is expanding into electric drivetrains, fuel cells, and other alternatives through its Acceleron business unit. The Mississippi plant aligns with its strategy to provide the engines and powertrains customers want during the energy transition.
Daimler (US$176 billion in revenue and employed over 100,000 worldwide in 2023) leads North American Class 8 truck sales through its Freightliner brand. The German manufacturer is investing heavily in electric trucks, including the eCascadia and eM2 models. The Mississippi plant will allow Daimler to secure battery supply as electric adoption increases.
Paccar (US$32 billion in sales and had 31,100 employees in 2023) is the #2 North American truck maker with its Peterbilt and Kenworth brands. The Bellevue, WA-based company plans to begin selling battery electric Peterbilt 579s and 520 refuse trucks in 2023. The Mississippi plant supports Paccar’s target to offer only zero-emissions trucks in certain markets by 2040.
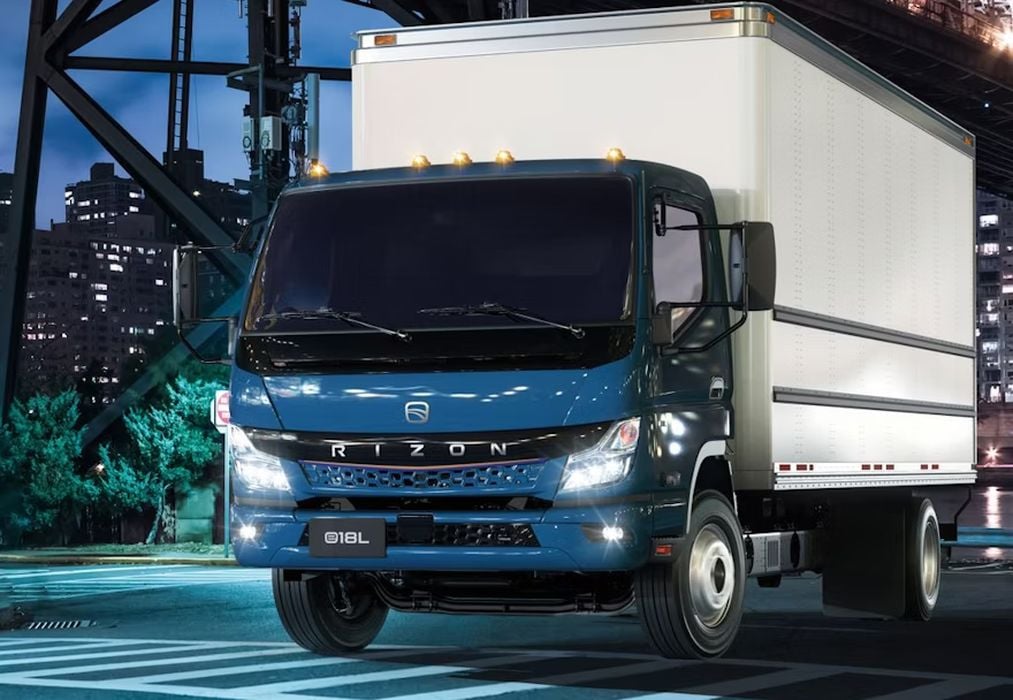
3D Printing Can Play a Role Tooā¦
We have previously written Fabbaloo articles on the trucking sector for Ford/Rivian and for Volvo trucks. While electric trucks grab headlines, Cummins, Daimler, and Paccar are all leveraging 3D printing technology as well.
Cummins uses metal 3D printing to prototype cylinder heads and manifolds. Printing prototypes cuts development time and costs versus traditional manufacturing methods. The company has also begun 3D printing some production parts like turbocharger housings.
Daimler employs polymer 3D printing to design full-size truck cabins, allowing engineers to test ergonomics and driver interfaces before tooling production. The ability to iterate CAD designs more quickly will prove useful as trucks become more automated.
Paccar prints prototype engine parts like oil pans and brake assemblies on industrial 3D printers. The digital workflow enables engineers to rapidly test component redesigns by printing new iterations overnight. Paccar is also exploring 3D printing metal parts directly on assembly lines.
Collaborating on EV technology will result in more communication between the engineers and technical experts at all three companies. Ideally, will include ongoing developments in automation and 3D printing.
The Research & Development Tax Credit
The now permanent Research and Development (R&D) Tax Credit is available for companies developing new or improved products, processes and/or software.
3D printing can help boost a companyās R&D Tax Credits. Wages for technical employees creating, testing and revising 3D printed prototypes can be included as a percentage of eligible time spent for the R&D Tax Credit. Similarly, when used as a method of improving a process, time spent integrating 3D printing hardware and software counts as an eligible activity. Lastly, when used for modeling and preproduction, the costs of filaments consumed during the development process may also be recovered.
Whether it is used for creating and testing prototypes or for final production, 3D printing is a great indicator that R&D Credit eligible activities are taking place. Companies implementing this technology at any point should consider taking advantage of R&D Tax Credits.
Conclusion
The massive Mississippi battery plant demonstrates Cummins, Daimler, and Paccar’s commitment to electric truck technology. Stricter emissions rules and state sales mandates will further spur adoption. At the same time, investments in additive manufacturing help manufacturers design and test the next generation of trucks faster and more efficiently. The results will shape the future of the global freight industry.