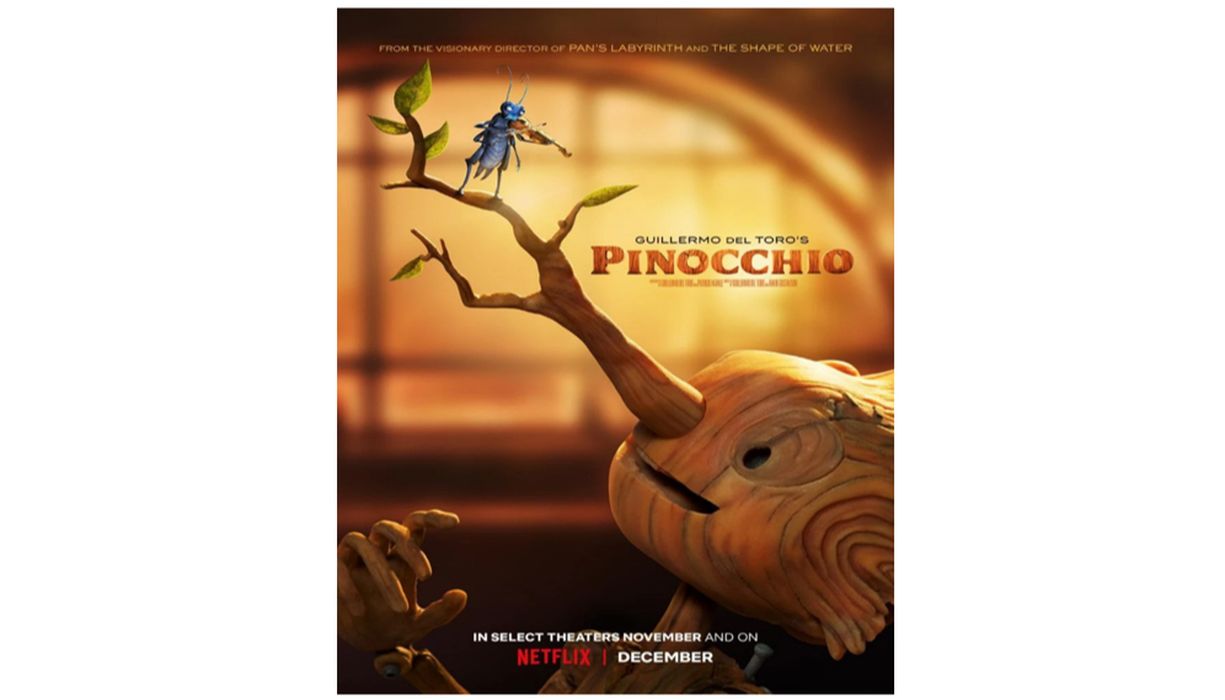
Charles R. Goulding and Preeti Sulibhavi reveal how 3D printing technology played a big part in the production of Guillermo del Toro’s “Pinocchio”, soon to be released on Netflix.
Years of stop-motion innovation and 3D printing are behind the high-quality designs in Guillermo del Toro’s interpretation of the childhood classic, “Pinocchio.”
Most of the puppets in del Toro’s “Pinocchio” were operated through mechanical gears in their heads. And, this Pinocchio, is the first metal 3D printed puppet, according to the film’s animation supervisor, Brian Leif Hansen. Just 10 or 15 years ago, this film could not have been made due to the void in technology necessary for creating complex-designed puppets.
The team spent a year and a half prototyping Pinocchio, before even making the first production model of the puppet. Eventually, more than 20 puppets were fabricated to ensure enough inventory during film production.
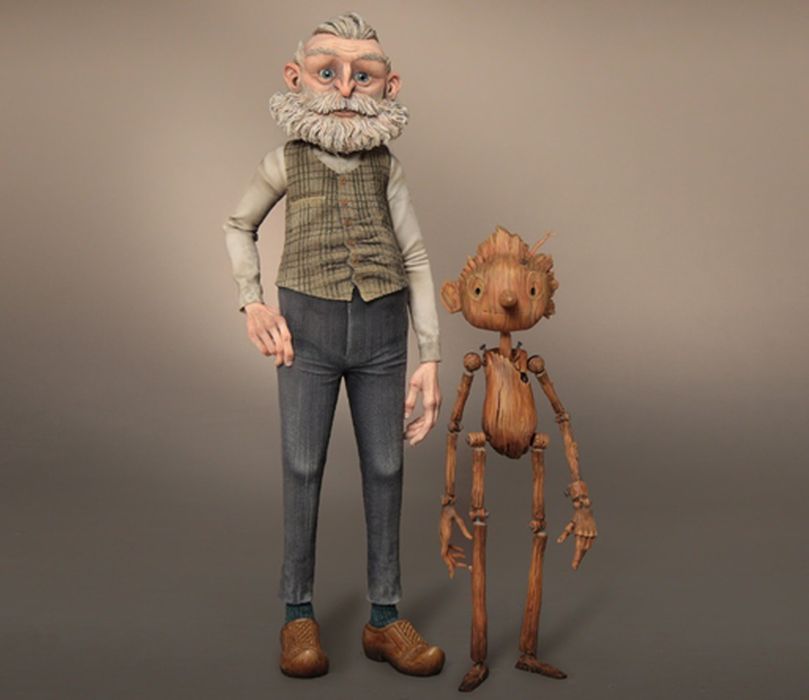
The Geppetto and Pinocchio production puppets, which were made from 2019 to 2020, are tightly controlled through components inside the puppets’ heads (likened to the inner workings of a Swiss watch). Geppetto (depicted above) was made from steel, foam latex, silicone, resin, fabric, fiber, plastic. 4 x 4 ¾ x 14″ (10.2 x 12.1 x 35.6 cm). And, Pinocchio was fabricated using 3D printed resin, 3D printed steel, steel, silicone, paint. 4 x 3 x 9.5″ (10.2 x 7.6 x 24.1 cm).
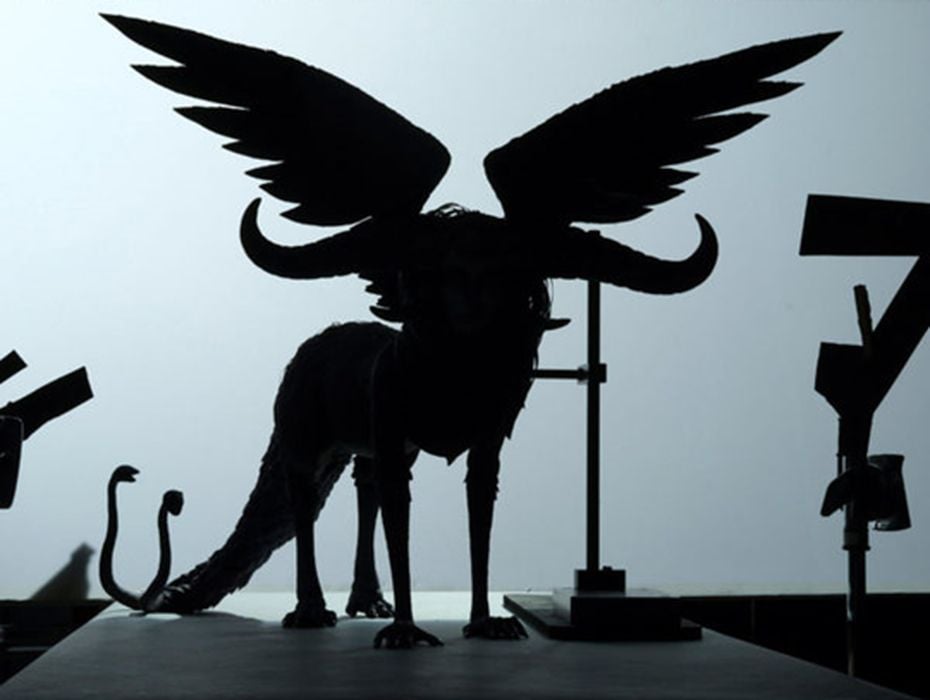
The ShadowMachine death production puppets were made using rigging, from 2019 through 2020. 3D printed resin, 3D printed steel, steel, silicone, fabric, and paint were all utilized for these.
Mackinnon & Saunders created this oversized cricket production puppet also with rigging, in the same period. 3D printed resin, steel, silicone, paint, as well as printed eyes were involved in fabricating this.

There was an exhibit that features del Toro’s Pinocchio at the Museum of Modern Art (MoMA) in New York City as well. People can’t seem to get enough of these classic characters.
The Research & Development Tax Credit
The now permanent Research and Development (R&D) Tax Credit is available for companies developing new or improved products, processes and/or software.
3D printing can help boost a company’s R&D Tax Credits. Wages for technical employees creating, testing and revising 3D printed prototypes can be included as a percentage of eligible time spent for the R&D Tax Credit. Similarly, when used as a method of improving a process, time spent integrating 3D printing hardware and software counts as an eligible activity. Lastly, when used for modeling and preproduction, the costs of filaments consumed during the development process may also be recovered.
Whether it is used for creating and testing prototypes or for final production, 3D printing is a great indicator that R&D Credit eligible activities are taking place. Companies implementing this technology at any point should consider taking advantage of R&D Tax Credits.
Conclusion
There are several life lessons to be learned from Pinocchio. Whether it is bravery, compassion or commitment to the truth, Pinocchio is a beloved fable for many reasons. Now, the 3D printing industry has another reason to love this story, as del Toro’s interpretation could not have been made without 3D printers.