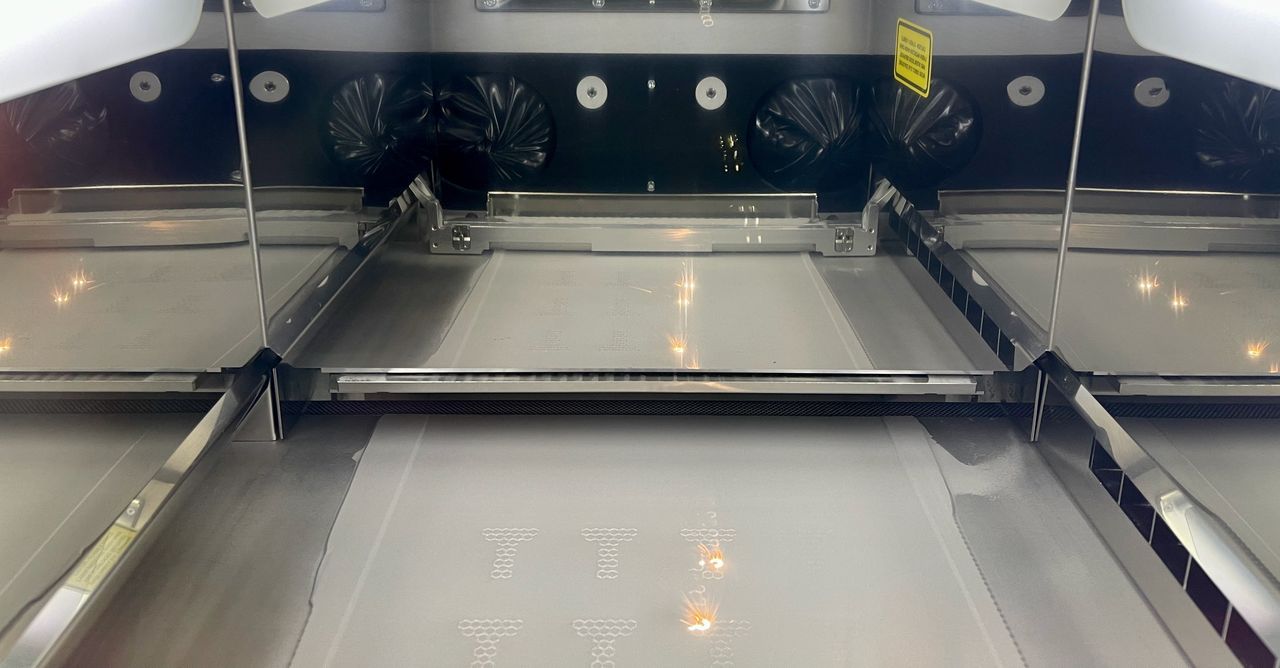
New research demonstrates the viability of acoustic monitoring for detecting porosity in laser powder bed fusion.
In-process monitoring is the key to 3D printing quality parts and to production that scales into true additive manufacturing (AM). While thermal imaging is the most obvious way to monitor certain types of 3D printingāsuch as laser powder bed fusion (LPBF)āacoustic monitoring is beginning to show promise, as well.
Roland LogĆ©, head of the Laboratory of Thermomechanical Metallurgy at the Ćcole polytechnique fĆ©dĆ©rale de Lausanne (EPFL), says his teamās research shows that acoustic monitoring is not only viable, but potentially superior to thermal imaging. As lead researcher Milad Hamidi Nasab explained in a press release, “The synergy of synchrotron X-ray imaging with acoustic recording provides real-time insight into the LPBF process, facilitating the detection of defects that could jeopardize product integrity.”
In essence, the researchers combined operando X-ray imaging with acoustic emission measurements, using the Swiss Light Source for the former and an ultra-sensitive microphone positioned inside the build chamber for the latter. By using an adaptive filtering technique to process the acoustic signals, the researchers were able to connect defects with their acoustic signatures.
Melt Pool Monitoring
The interactions between lasers and powder beds inside metal 3D printers are incredibly complex, with the melt pool fluctuating between solid, liquid and vapor phases. As a result, variables such as the angle of the laser or the geometry of the metal powder can sometimes lead to inter-regime instabilities within the melt pool, in which it shifts between conduction and keyhole regimes. Itās the latter type, specifically an unstable keyhole regime, that leads to porosity.
The EPFL researchers found an increment in the acoustic signal amplitude when the regime changed from conduction to keyhole, which they correlated with a change in laser absorptivity. By correlating between the acoustic signals and the x-ray images, the researchers were able to design a filtering algorithm that can predict melting regimes with a time resolution of 100 µs.
Read the rest of this story at ENGINEERING.com