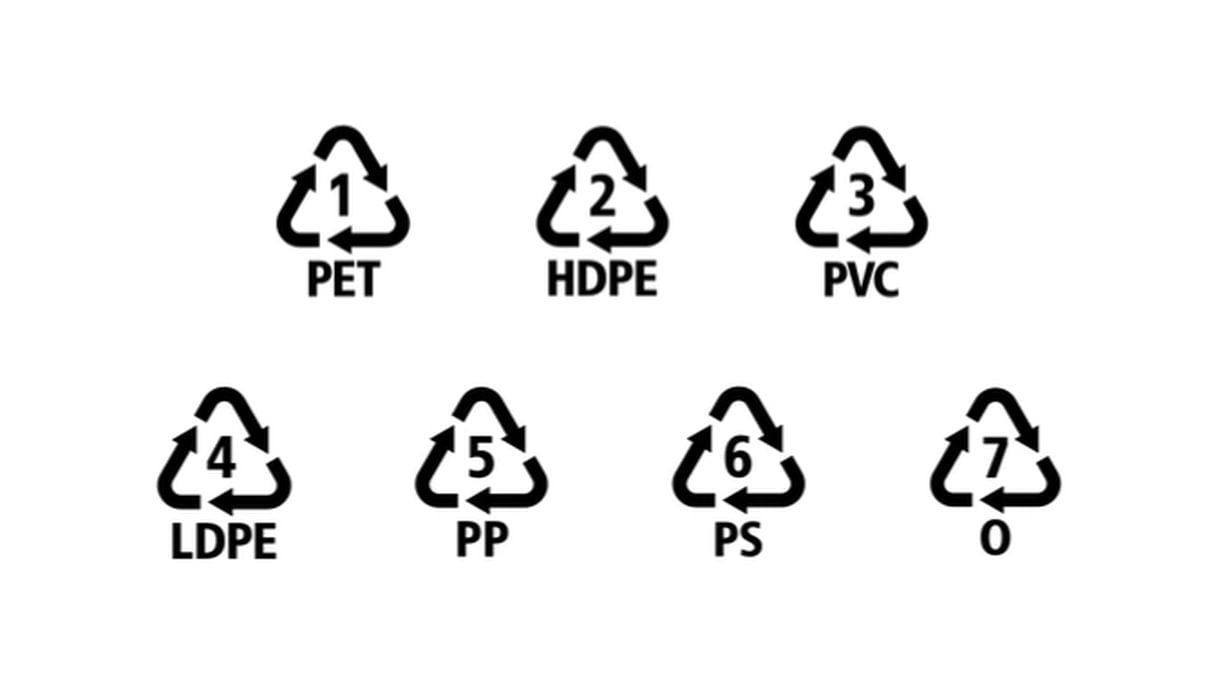
I’m increasingly disturbed by the pile of waste 3D prints I am generating, and I have an idea that might help recycle them.
Most 3D prints are not easily recyclable anyway; PLA, the most common 3D print material, is touted as being recyclable, but there are so many obstacles in the way.
The primary problem is that basically every print is made of slight different material and colors, making it difficult for recyclers to collect identical material to re-make into filament.
Yes, you could just batch it all together and make a kind of “Frankenstein” filament, but it wouldn’t really work. Today’s FFF 3D printers rely on input filament of the highest quality and chemical consistency to obtain those good results. Bad filament in, bad prints out.
The other problem is collection. If you hope to recycle thermoplastic into filament, where do you find it? The only practical approaches I’ve see so far are ventures that, for example, collect only Pepsi bottles. These would by definition have the exact same PET material.
Then I look at my pile of waste prints and sigh. There’s little alternative but to send them to the landfill.
If I were to put them in the recycling bin they would also end up in the landfill. That’s because plastic objects are inspected at the recycling center and sorted according to the material. If an object’s material can’t be identified, it goes off to the side and back to the landfill.
But wait, how, exactly is the material determined? Do the workers at the recycling plant wear special glasses that highlight certain plastics?
Nope, they instead look for specific recycling symbols embossed on to plastic parts.
At top are some of the common symbols they’d be looking for, as plastics are officially classified into broad categories. Note that these labeling systems might differ in other jurisdictions, but the principles are the same.
Note there is no symbol for “PLA”, although it could fall into “Other”. While 3D printers use a lot of PLA, it seems to be a tiny portion of plastic use overall.
I envision my trash prints showing up at the recycling center and they’re flipped around looking for one of these symbols. There are none, and the item is shunted over to the landfill.
That’s why recycling prints won’t work.
But wait, what if these prints DID have these symbols?
It would certainly be possible to emboss symbols like this onto 3D prints, we do that sort of thing all the time on our 3D models.
No one ever does that because it’s too hard. We don’t have the embossed figure ready to apply to our models.
What if we did? What if 3D printer slicing systems included a simple feature that would stamp a recycling symbol on a model before slicing? For many models this would be easy to apply to the bottom of the print.
I propose that those building 3D print slicing systems include a feature to easily apply recycling stamps to print jobs.
These symbols could not be applied to the 3D model files themselves, because we don’t know what material will be used to print them. It might be ABS, or it might be HDPE. Or PP. Or all of them in several jobs. That’s why the slicer must be the step where the symbol is applied.
It could even be a feature to nag the user to apply a stamp before proceeding with exporting the GCODE file. The stamp selection could be automatically done by examining the material used for slicing, too.
For most prints — being in PLA — the stamp could be #7, but I do occasionally print in PET, PP and PS (as ABS or ASA).
If this were available, I would use it. I could then look at my enormous box of waste prints and actually feel good pouring it all into the recycling bin.
How about it, software developers? Could we include a recycling stamp feature in future 3D print slicing software?
Kerry, in the 3D printing of solid-state batteries, today we are applying the concept of Powder to Powder. We can
apply a semiconductor mentality and as software developers could include a recycling stamp feature in our 3D print slicing software designating the category of the to-be-recycled battery?
This is game changing and huge ESG cookie point for our unique 3D printing process,