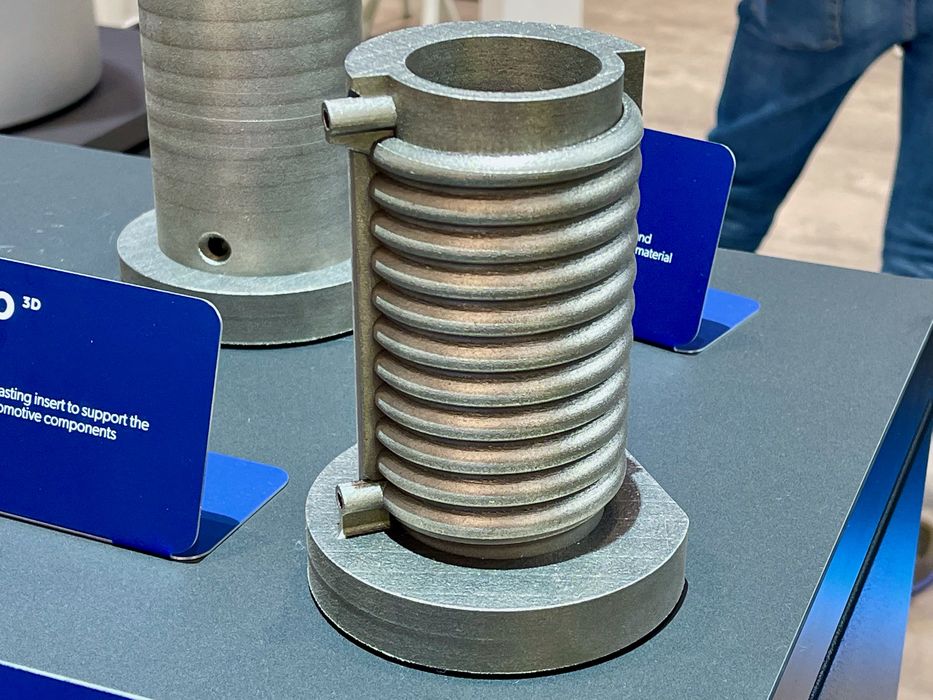
I had a discussion with Velo3D and learned of a very interesting application for metal 3D printing.
3D printing is often seen as an alternative to injection molding services, as it provides more geometric freedom. But in this application, itās possible to make injection molding better.
Injection molding involves creating a solid metal mold into which hot, liquid polymer (or metals) are injected. After a cooling period, the material solidifies and can be removed from the mold.
This is a relatively rapid way to mass produce identical parts that has been used for many decades, but thereās one issue: cooling.
The material does have to remain in place for a period of time to properly solidify before removal from the mold. If not, then the part could be distorted as its soft body will sag when removed from the mold.
Over repeated injections, the thick metal mold will accumulate heat and eventually have to be left alone to cool. That effect also can slow down production.
Yet another thermal problem exists: as the mold is repeatedly subjected to heating and cooling cycles, it eventually begins to break down, and cracks can occur after a certain number of cycles.
Velo3D apparently has been working with clients building specialized molds that provide additional cooling that could resolve all of these issues.
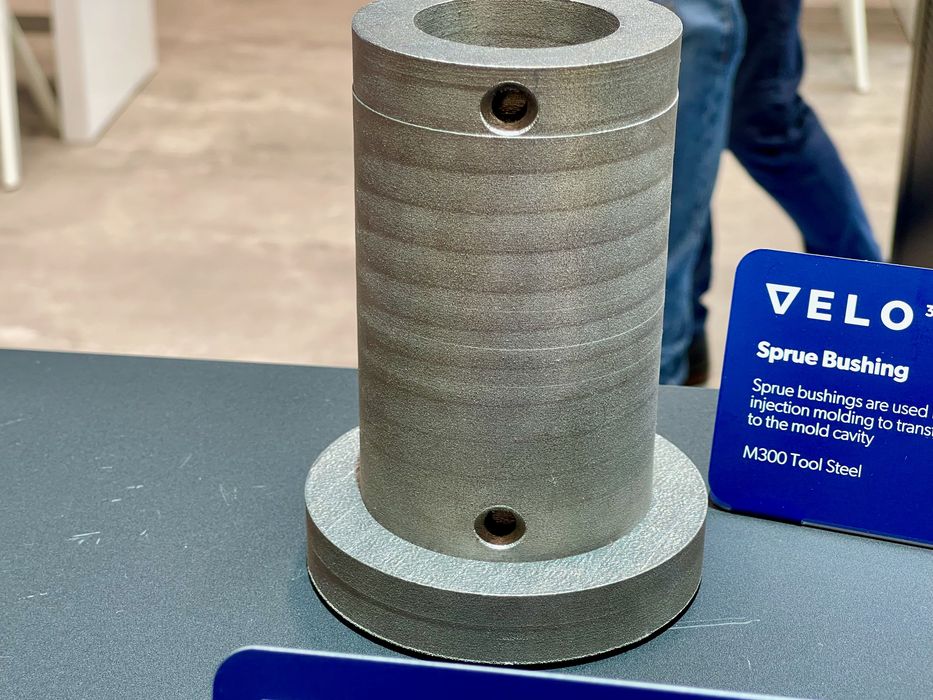
This is achieved by 3D printing the mold, but including in its design a series of small integrated channels through which cooling material can be applied. These integral cooling channels can keep the mold at a relatively stable and safe temperature, in spite of injections of hot material. The channels can be located inside the mold quite close to the void, enabling maximum chilling.
The cool mold helps to cool down the injected material at a more rapid rate, as the cooling fluid can pull heat from the material. That makes that part of the process a bit faster.
The mold will not require major cool down periods, because itās always kept cool.
Finally, the mold should last a lot longer because of more stable thermal conditions. That means there is less cost tied up in mold making, which is a significant expense in the process.
Velo3D is uniquely able to produce these complex metal injection molds due to their ability to 3D print metal parts (mostly) without support structures. You can imagine trying to pick out support structures deep inside one of those integral cooling channels ā it would be essentially impossible. However, Velo3Dās 3D printing process can apparently produce them quite easily.
This is a very interesting application of metal 3D printing that I am certain many injection molding operators have not seen. However, if their competitors catch on, they may also adopt this unique hybrid approach to injection molding.
Via Velo3D