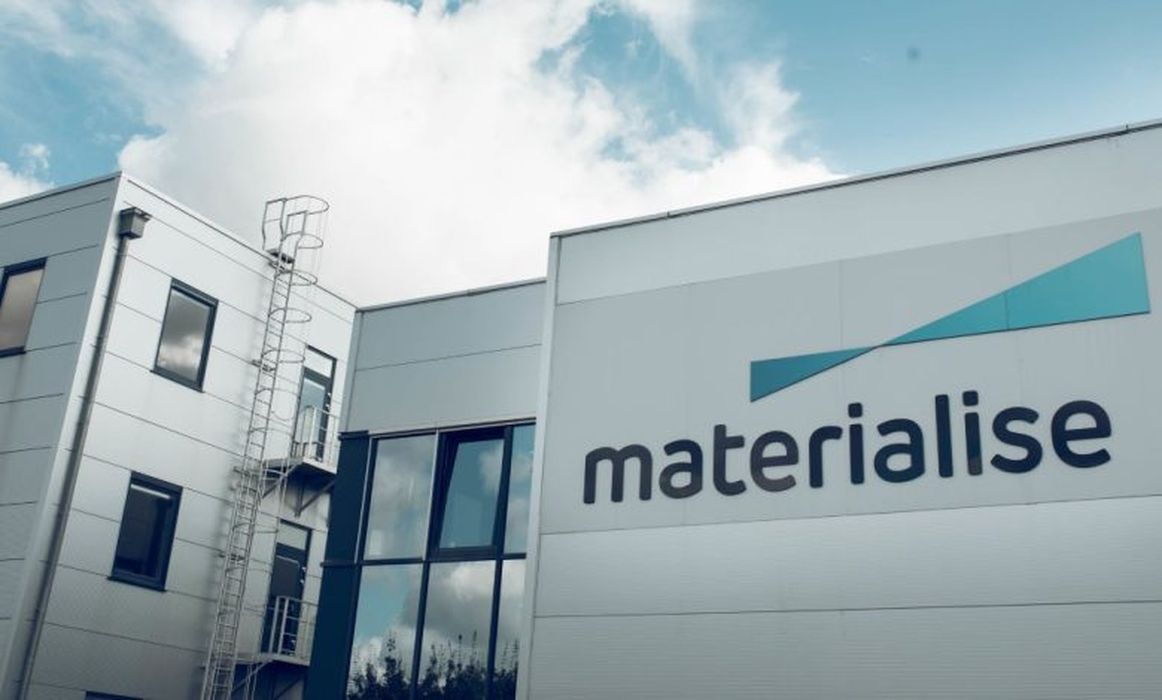
Materialise Process Control, released in collaboration with Phase3D and Sigma Additive Solutions, enables quality control using data gathered during the 3D printing process, and the Build Processor Software Development Kit (BP SDK) connects 3D printers with software for data preparation.
Materialise, a global leader in 3D printing software and service solutions, has collaborated with both Phase3D, a Chicago-based startup creating real-time inspection technology for powder-based AM, and Sigma Additive Solutions, a software companyproviding in-process AM quality assurance software. The companiesâ collaboration is focused on providing process monitoring for metal 3D printing, through Materialise Process Control â a newly released software solution that enables manufacturers to introduce quality control using data gathered during the 3D printing process. Materialise has also introduced its Build Processor Software Development Kit (BP SDK) â a platform connecting 3D printers with software for data preparation, such as Materialise Magics.
Materialise Process Control
Materialise Process Control enables users to identify defective parts before they are sent to post-processing and quality inspection. It provides access to technology-agnostic process monitoring for metal AM and makes it possible to combine data from different monitoring systems.
Materialise collaborated with Phase3D and Sigma Additive Solutions to integrate complementary data and to provide deep insights into the 3D printing process. Phase3D technology, particularly Project Fringe, adds height mapping, a form of topographic layer data, and Sigma Additive Solutions provides thermal data from the melt pool, the area of the melted material during the metal 3D printing process.
Phase3Dâs Project Fringe is a proprietary structured light technology that measures any powder-based AM process. The real-time data creates detailed measurements for where and when a print anomaly occurs. Project Fringe presents data in 3D â enabling users to see a multitude of print anomalies in real time. The solution allows customers to be confident about their part quality, or stop the 3D printing process if a defect has been detected â saving machine time and money.
âWe are excited to offer Project Fringe, our flagship hardware/software inspection technology, to Materialise customers through this collaboration. Real time inspection using rapid height measurement technology can reduce the cost per part in 3D printing,â said Niall OâDowd, Founder, and CEO of Phase3D.
âMaterialise Process Control uses artificial intelligence to automate quality control, helping our customers save significant time and money,â said Bart Van der Schueren, CTO of Materialise. âThrough collaborations with partners like Phase3D and Sigma Additive Solutions, AM users benefit from a technology-agnostic innovation that offers unparalleled insights into their 3D printing process for continuous improvement.â
Materialise Process Control is available as part of CO-AM, Materialiseâs end-to-end software platform for 3D printing, and as a standalone software solution. As an open software solution, partners will be able to add their software and monitoring technology.
Read the rest of this story at VoxelMatters