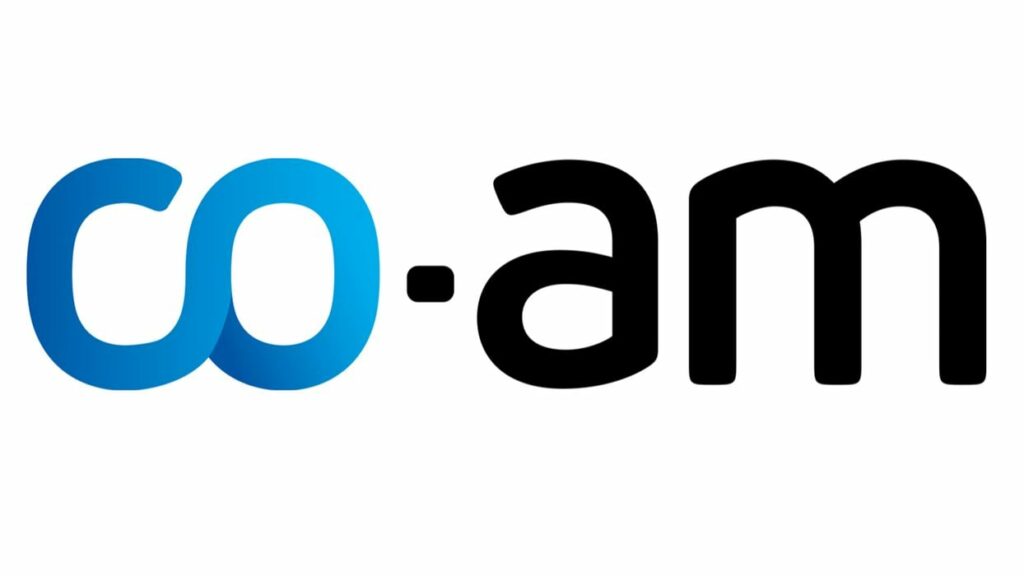
I had a chat with Materialise about their new CO-AM software platform.
Belgium-based Materialise is well-known in the additive manufacturing industry for their powerful software products that are used by many to prepare complex 3D print jobs for execution at scale. They also provide sophisticated 3D print services for industry, often taking on unique projects that no one else is able to handle, like our Design of the Week selection from last January.
While AM is an increasingly popular manufacturing method, it does have some significant challenges to overcome.
One of them is that many 3D printers are essentially standalone devices that donāt really integrate with the other steps in the manufacturing process. They print, but they donāt manufacture. For that there are usually multiple other steps involved, such as cleaning, polishing, painting, assembly and countless other options that depend on the specific product being produced.
Because additive devices are typically standalone, it means there are very often manual procedures required to carry the product through several steps of a workflow to completion. That might sound straightforward, but it gets more complicated when you confronted with multiple products, higher volumes, outsourced steps, multiple geographies, and so on.
Materialise recognized this complexity and their approach for simplifying the work effort is to offer CO-AM, a flexible workflow system specialized for this purpose.
The cloud-based CO-AM is based on software obtained from a prior corporate acquisition by Materialise, and offers a completely new experience.
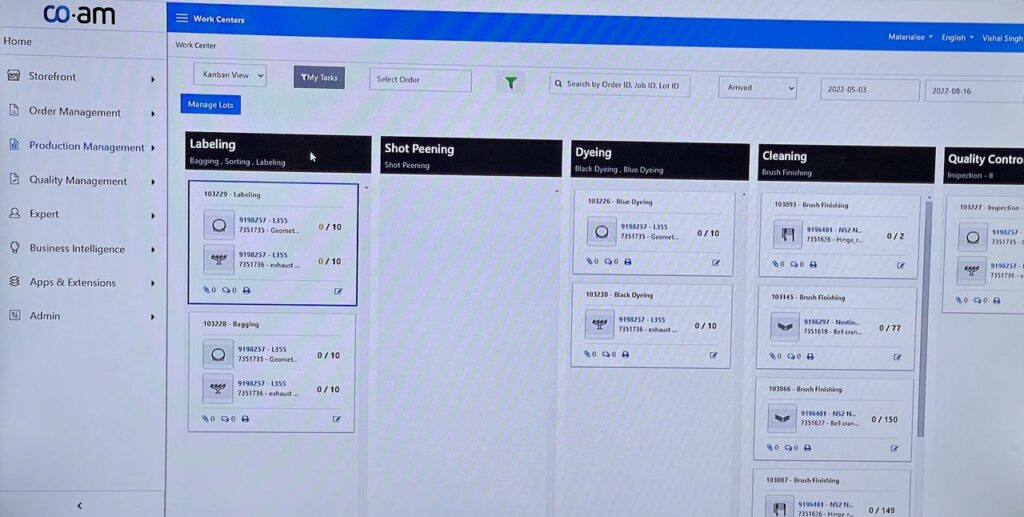
CO-AM users can set up any type of workflow required, as the system is highly customizable. Here you see one example of a workflow in CO-AM.
The idea is to create an environment that ties together the disparate parts of the manufacturing lifecycle that otherwise might get out of sync. Materialise told us it could be the āsingle source of truthā for a manufacturing operation.
Their strategy is to create an environment where customers have a complete ecosystem and ānever have to go outsideā.
This is accomplished through a series of apps and extensions. For example, they directly support EOS and Stratasys equipment, as well as external software service providers like CASTOR.
A manufacturer can then set up a specific customized workflow for their particular product manufacturing experience in CO-AM that includes all the steps required for product completion.
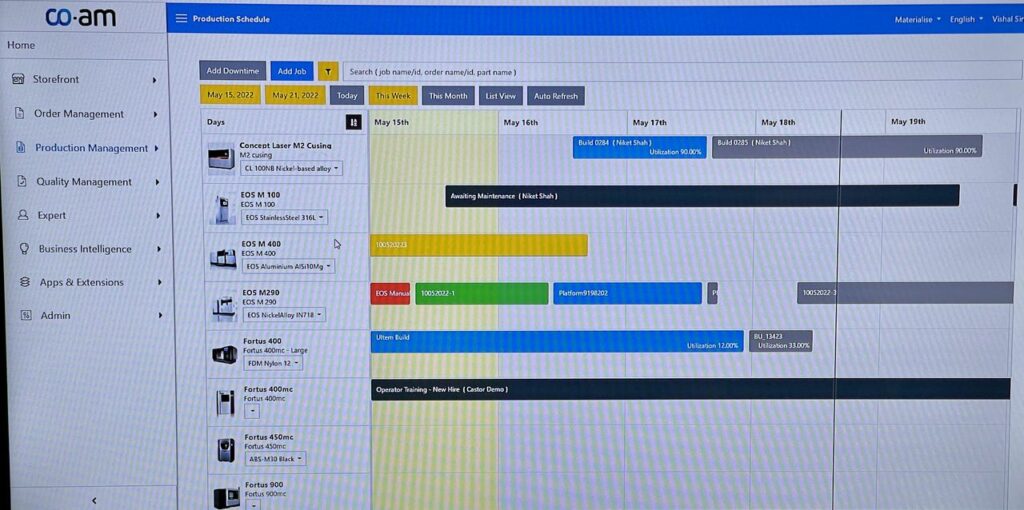
CO-AM visibly works by observing a ācardā that travels between workflow steps. Participants executing the steps can pick up their next piece of work easily and efficiently to get it done. Materialise said there is a QR code that travels with the part, which can be read by an iOS app to track the itemās progress.
The workflow typically starts with a part order and then queuing and scheduling of the various steps required to produce it, all the way to shipping.
One issue with CO-AM seems to be that it is focused around single machines at the moment. In other words, the workflow is directed at preparing work for specific machines, as opposed to dispatching work to a group of similar machines. In other words, it doesnāt seem to have āprint farmā capability. However, I suspect that Materialise is aware of this and might be developing a solution in the future, as this will increasingly be a scenario Iām sure theyād like to address.
Materialise provides a great deal of assistance for CO-AM users, including training and an onboarding process.
This is a very interesting product from Materialise that I am certain will be taken up by many of their clients.
Via Materialise