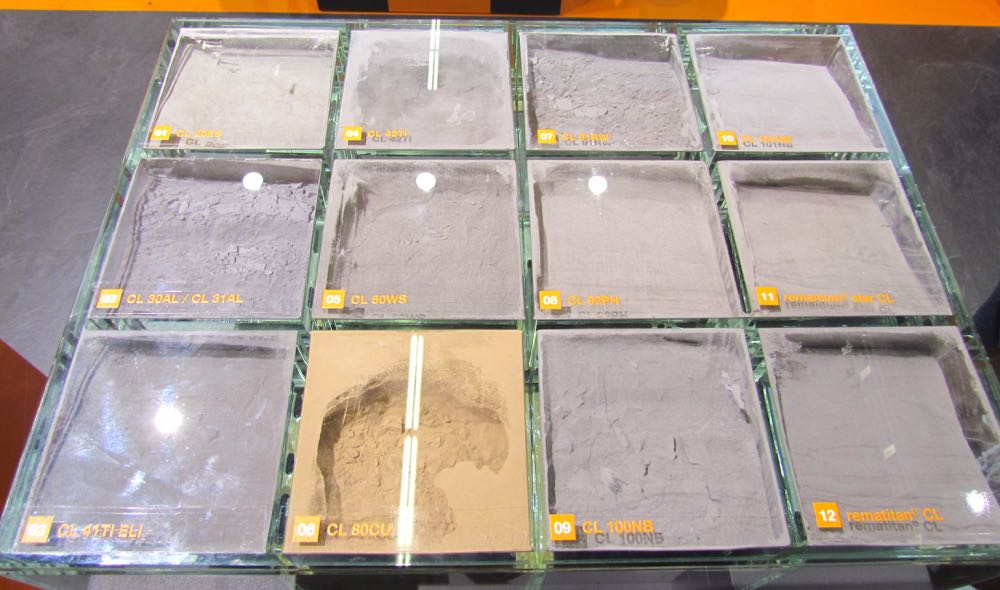
What you need to know when selecting, storing and using metal powders for additive manufacturing applications.
As a technology, metal 3D printing has seen remarkable growth in recent years, with new tools and new materials being added all the time. The majority of metal 3D printing processes use metal powders as feedstock, although there are some exceptions. Hence, as metal additive manufacturing (AM) becomes more common, the metal powder market will grow along with it.
In 2021, the global metal powder market was valued at $6.75 billion and projected to grow to $10.79 billion by 2029. While the COVID-19 pandemic had a negative impact on overall demand—as it did for so many industries—it’s not unreasonable to expect the market to rebound if 3D printing can relieve issues in the global supply chain.
In any case, given how crucial metal powders are to metal AM, it’s worth taking a closer look at what makes them different from other bulk materials and what to keep in mind when selecting, storing and using them for additive manufacturing.
Let’s start with the basics.
A Brief Primer on Powder Metallurgy
The process of converting raw metals into fine powders and then working those powders into solid objects dates all the way back to the Incas and ancient Egyptians, who both used powdered metals to produce jewellery and other valuable artifacts. In the 19th century, Russian rubles were made from platinum powder that was sintered to create coins, but the mass production of metal powders didn’t really take off until the introduction of incandescent lightbulbs and the tungsten wires therein.
While there are a variety of ways to produce metal powders, the most common are the so-called sponge iron process and atomization via water or gas. The sponge iron process involves mixing magnetite ore with coke and lime and then reducing it via a retort inside a kiln, which creates an iron “cake” and slag. Once separated from the slag, the cake is then crushed and annealed into powder. The resulting particles are highly porous, hence the term ‘sponge’ iron.
Atomization, on the other hand, involves forcing a molten metal stream through a nozzle and introducing turbulence into the resulting flow via inert gas supplied just before the stream leaves the nozzle (gas atomization) or via high-speed streams of atomized water, that both breaks the stream into drops and cools them (water atomization).
Gas Atomized Powders Versus Water Atomized Powders for Additive Manufacturing
Gas atomized powders tend to be spherical, which improves their flowability and therefore makes them desirable for metal additive manufacturing. Water atomized powders tend to be more irregular in shape, but there have been recent efforts to improve their morphology to make them more amendable to AM processes.
Gas atomized powders also have higher purity levels compared to water atomized powders, as the use of inert gases in processing minimizes the risk of contamination. It should be noted, however, that impurities in water atomized powders can be removed in post processing, e.g., through sieving and washing. Nevertheless, in applications where ensuring low oxygen content is critical, gas atomized powders are generally the better option.
The one caveat to add is that gas atomized powders are generally more expensive to produce, due to the complexity of processing involved. According to Koushik Viswanathan, assistant professor of mechanical engineering at the Indian Institute of Science (IISc), “Gas atomized powders can be from 2x to 30x more expensive for common materials.” As water atomized powders are most cost-effective, they can be an attractive option for less demanding applications or more cost-sensitive projects.
Metal Powders in Additive Manufacturing Versus Other Manufacturing Processes
Historically, metal powders were processed into solid objects via powder compaction, where the powder is pressed into a die to form a desired shape and then sintered to make it into one solid piece. If you’ve worked with processes of this kind—including die pressing, powder forging, hot isostatic pressing (HIP) or metal injection molding (MIM)—you’re already well acquainted with many of the important properties of the metal powders used in metal AM.
However, as Ryan Dehoff, director of the Manufacturing Demonstration Facility at Oakridge National Laboratories (ORNL) explains, there are some important differences between the powders used for these processes: “AM technologies typically use a narrow range of powder size distributions that meet flowability requirements for the process, size ranges for proper melting and specific chemistries based on process.”
Ankit Saharan, head of metals technology at EOS agrees, adding: “Metal powders for AM, specifically L-PBF [laser powder bed fusion] or DMLS [direct metal laser sintering] are different from MIM powders in the sense that MIM powder tends to be much finer and not necessarily spherical in shape. Metal AM powders have historically been preferred to have spherical morphology, although some advances in this process suggest that we might be able to process non-spherical powder like flakes (chips) or water atomized powder through AM processes as well.”
Viswanathan notes that when powder is being “rolled on” by a spreading blade for powder bed fusion (PBF), flowability is particularly important. “Perfect spherical shapes are strongly preferred to prevent powder sticking,” he explains. “Think of walking on a layer of ball bearings versus sand. On the other hand, a process like directed energy deposition (DED), where powder is delivered via a carrier gas, is more tolerant of randomly shaped particles. The same is true of processes such as MIM, where flowability is often not a primary concern because the material is being squeezed anyway.”
Important Factors to Consider When Selecting Metal Powders for Additive Manufacturing
The most crucial consideration when it comes to powder selection for metal AM is, not surprisingly, chemical composition. “Chemistry is likely the dominant factor, but this is usually derived from the end application target,” says Dehoff.
“Conformance to chemical composition of the metal powder is crucial,” adds Saharan. “Especially in applications where material properties and mechanical performance is critical, like aerospace and medical. This would include the oxygen content in the material, which would affect the aging of the powder in this process.” Viswanathan also cites the presence of nitrogen being a concern in some cases, depending on AM process.
Beyond chemistry, Dehoff and Saharan both noted the importance of powder cleanliness (i.e., free of contaminates and surface oxides), powder uniformity (consistent particle size distribution results in uniform melting and minimized porosity in the final product) and powder consistency. With regard to this last attribute, “Batch-to-batch variation during production can lead to variations in the end performance of the printed component,” explains Dehoff. “These variations are traditionally very difficult to track down and eliminate.”
Other factors to consider are powder flowability and spreadability. The former is important if you’re using a top-fed or gravity-fed machine, while the latter matters for uniform powder layers. Both derive from the other factors cited above but, as Saharan points out, one must nevertheless be careful to distinguish spreadability from flowability, as these are very distinct features.
Viswanathan points out that although flowability is often cited as a primary consideration because of how common PBF is, “mileage may vary depending on which AM process you’re considering.”
Finally, there’s the ever-present question of material cost. As with more traditional manufacturing processes, striking a balance between material performance and cost is not easy, especially for cost-sensitive applications. “A metal powder that can be atomized is not enough,” says Saharan. “It also needs to be processed at high enough speeds inside the machine to make a profitable business case.”
To sum up, there are seven important factors that need to be considered when selecting metal powders for additive manufacturing applications:
- Chemistry
- Cleanliness
- Uniformity
- Consistency
- Flowability
- Spreadability
- Cost
Refractory Metals & Additive Manufacturing
One of the often-touted advantages metal AM has over subtractive processes such as milling and turning is its ability to work with metals that are difficult to machine (DTM). These include higher grades of steels, such as stainless steels and hardened steels, as well as non-ferrous metals such as titanium, tungsten and various nickel-based alloys. While it’s true that DTM metals are easier to work with when producing workpieces additively rather than subtractively, refractory metals with high melting points, such as molybdenum and tungsten, present their own challenges.
For one thing, refractories are difficult to atomize to begin with, as Viswanathan explains: “The resulting powders are often not particularly spherical in shape because atomization (via jet breakup into droplets) is not very efficient, so powders from these metals are difficult to obtain via atomization in general.”
“The refractories, due to their high melting point, have a higher transition temperature than what most machines can accommodate today, which makes these materials very brittle under the current processing conditions,” explains Saharan. “As a result, these material processes tend to suffer from microcracking and lack-of-fusion defects, especially in bulky parts.”
Dehoff notes that ORNL has dedicated significant resources to improving the printing process for tungsten, molybdenum and other refractories. “It is difficult to put enough energy into the material in order to melt it,” he says. “If you can get the material melted, cracking during solidification or upon cooling can be a major issue.”
Because refractory metals require very high energy densities—even compared to DTM metals like titanium and certain steels—the powder ages more aggressively. This is due to the larger heat affected zones (HAZ): non-melted areas that undergo changes in material properties due to their exposure to high temperatures. Viswanathan notes that, for this reason, tungsten powders—specifically tungsten carbide—are more common in powder metallurgy applications where the cooling rate can be more accurately controlled in a furnace, such as making cutting tool inserts.
“The other challenge is the speed of the process is very slow, owing to their high melting points,” says Saharan. “This tends to make the parts from these processes non-commercially viable in many cases.”
Read the rest of this story at ENGINEERING.com