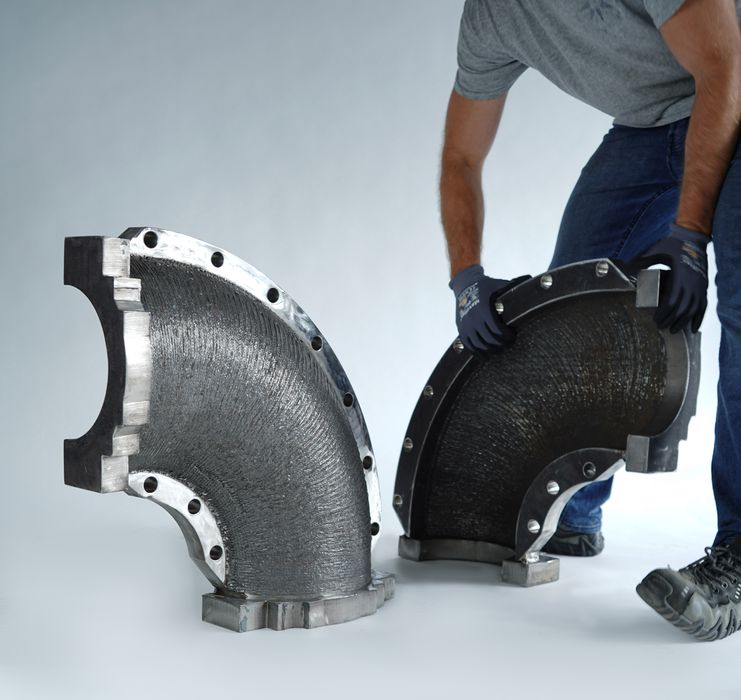
MX3D produced a large metal part that opens a path for a very intriguing future.
If you haven’t heard of MX3D, they manufacture a WAAM metal 3D printer. “WAAM” stands for Wire Arc Additive Manufacturing, a process where a welding wire is pushed into a metal arc, which melts the wire. By moving this melt point around in 3D space, it’s possible to gradually build up a solid metal object.
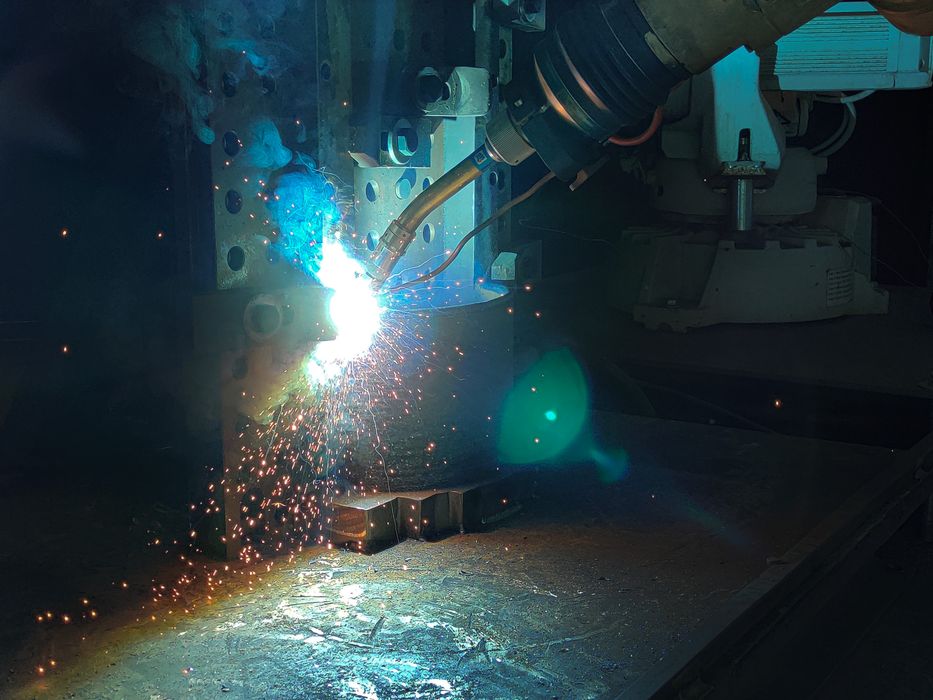
In the past they’ve undertaken some interesting projects, the most notable is certainly their production of a temporary metal bridge over a canal in Amsterdam.
Note that their technology is able to produce rather large objects. This is due to their use of a robotic arm to wield the toolhead, and thus the object volume is limited only by the robot’s reach.
The new part, pictured at top, is a standard clamp used in the oil & gas industry. It’s used at industrial facilities to patch holes in piping or reinforce pipes before they break. In this way a site can stave off maintenance a bit longer, and thus save money.
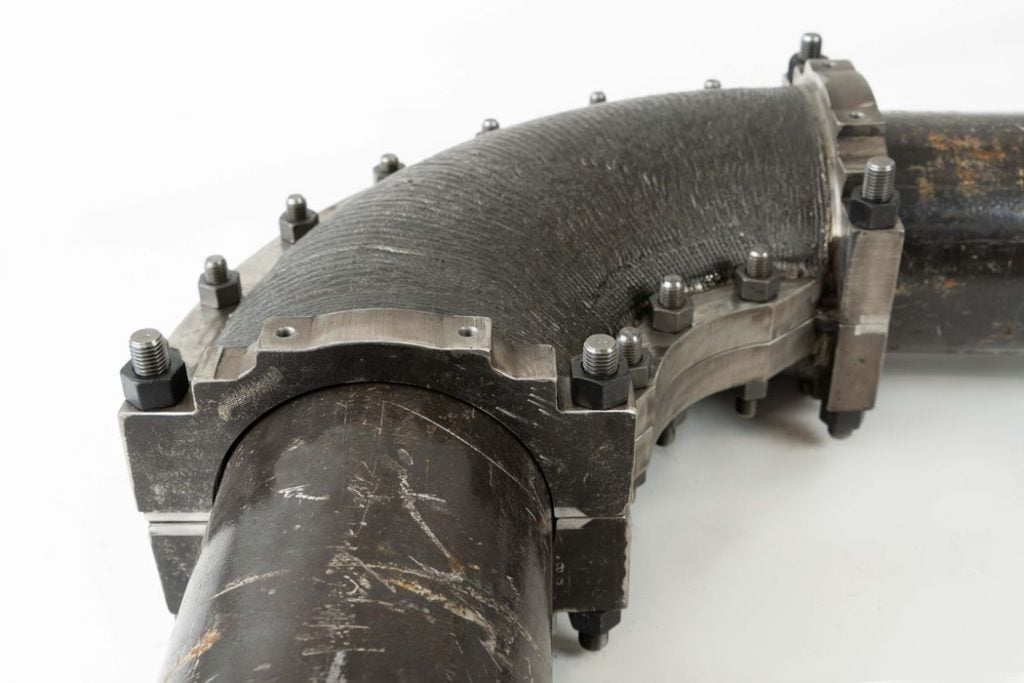
The important thing to know about this part is that it has successfully undergone significant testing by the Belgium Welding Institute, and supported by Lloyd’s Register. MX3D explains:
“The consortium managed to reach a high level of assurance for the WAAM clamp. BWI tested the materials and confirmed the printed material complied with key TEAM Industries requirements for this material. The MX3D M1 Metal AM System, facility and procedures were qualified by Lloyds Register. TiaT performed non-destructive testing, such as Ultrasonic Testing (UT), Penetrant Testing (PT), Radiographic Testing (RT), showing no relevant defects. TEAM Industries has performed a pressure test, which ran until the maximum pressure of the test installation (i.e. > 60 Bar) without any failure.”
In other words, they’ve managed to certify their materials and process to enable production of this type of part for the oil & gas industry.
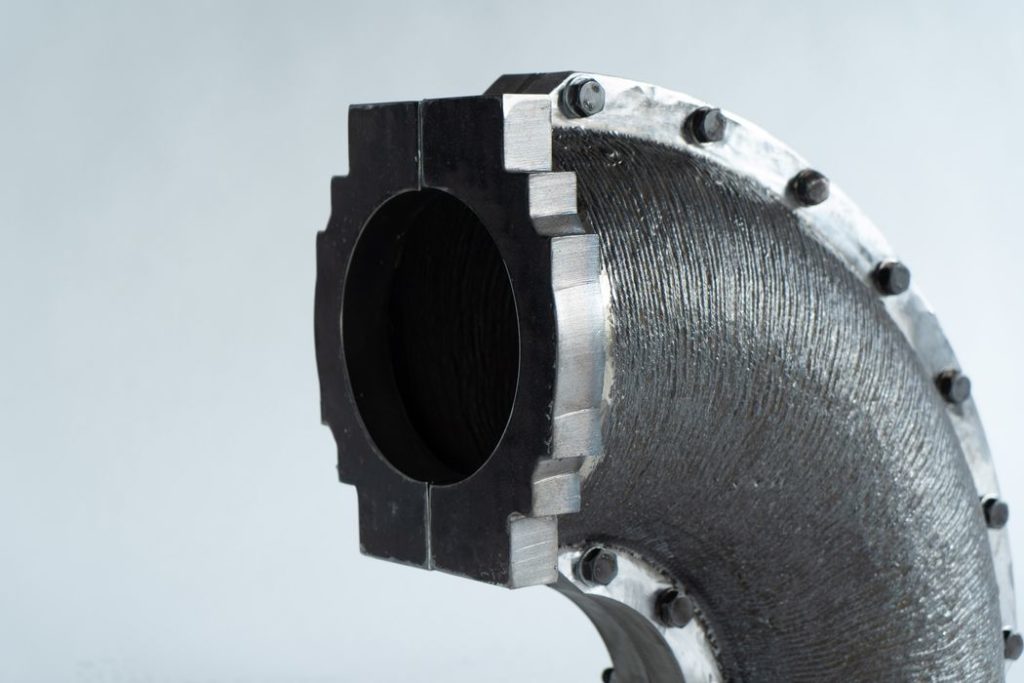
Why is this so important? It’s because of the need for speedy repairs. Should a pipe blow a hole, a plant could be shut down for weeks while replacement parts are procured and delivered. The idea here is to use a form of digital inventory to reproduce the part — in this case a clamp — very rapidly, and perhaps even on site at the plant itself. Because the MX3D system is a hybrid, there is decreased need for additional manual work to complete the part.
MX3D uses a hybrid approach where the majority of the part is produced additively, while a second stage of CNC milling shaves off a minimum of material to finalize the fitting surfaces of the part to perfection.
This means that, in theory, on site MX3D equipment could produce this replacement part — and perhaps others — virtually on demand. The savings to be had by preventing days or weeks of downtime at such a plant are enormous, and could easily justify the acquisition of MX3D equipment several times over.
It seems that MX3D has found a way to leverage their technology into the vast market of the oil & gas industry. There are a great many plants requiring this type of part around the world, and MX3D may be hoping most of them will eventually be equipped with their WAAM gear.
Via MX3D