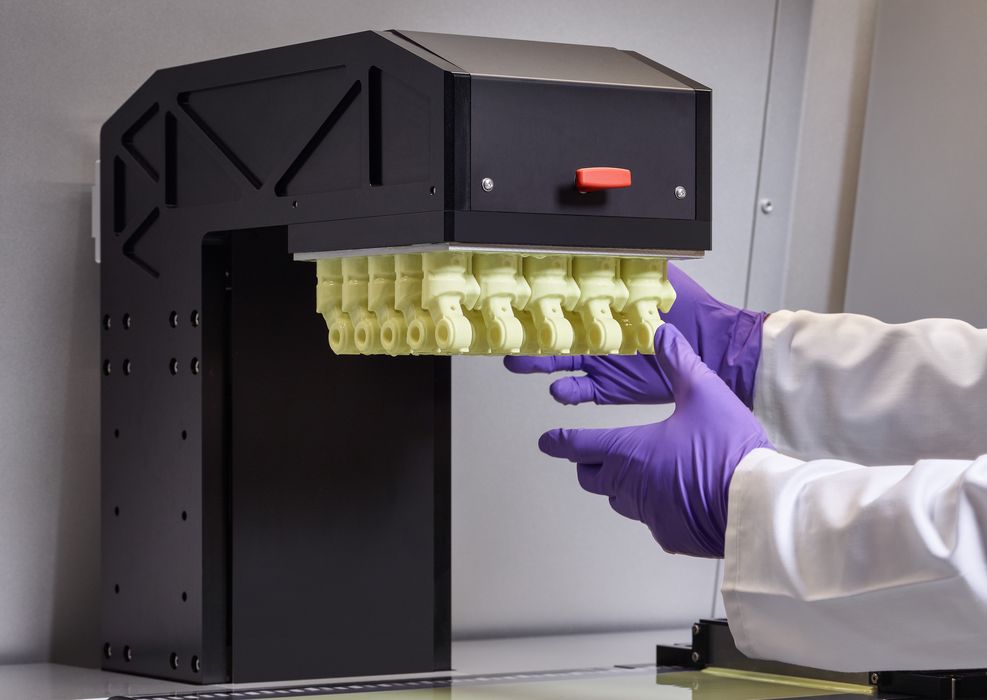
Admatec announced a new furnace that could enable their clients to take on additional production of 3D printed ceramics.
Ceramics are an unusual material for 3D printing, with relatively few options available for companies wishing to acquire equipment. However, ceramics offer notable advantages over the more commonly available plastic and metal 3D print materials. Extremely high heat resistance, lack of electrical conductivity, dimensional stability regardless of temperature and chemical invulnerability are all desirable engineering properties for a variety of applications.
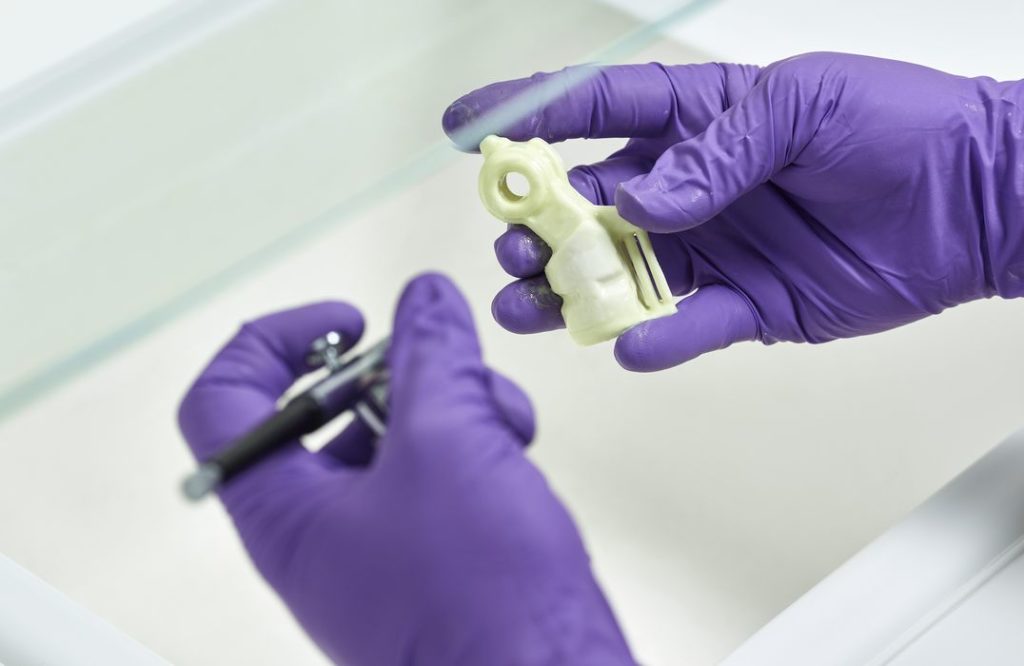
Admatec is one of the few companies producing ceramic-capable 3D printers. Their printing process involves a mix of liquid photopolymer and ceramic particles, which are selectively cured using a DLP projection light engine. While their initial products were relatively small, their current flagship 3D printer is the Admaflex300.
This device boasts a very large (for ceramics) build volume of 260 x 220 x 500 mm. At that size this device is not only able to 3D print large single objects, but more importantly many smaller objects within the same print job. Due to the nature of their printing process each layer takes the same amount of time to execute, regardless of the amount of material used or number of objects.
By the way, the āflexā in the Admaflex 300 name indicates that the device can actually be used for 3D printing either ceramics or metals.
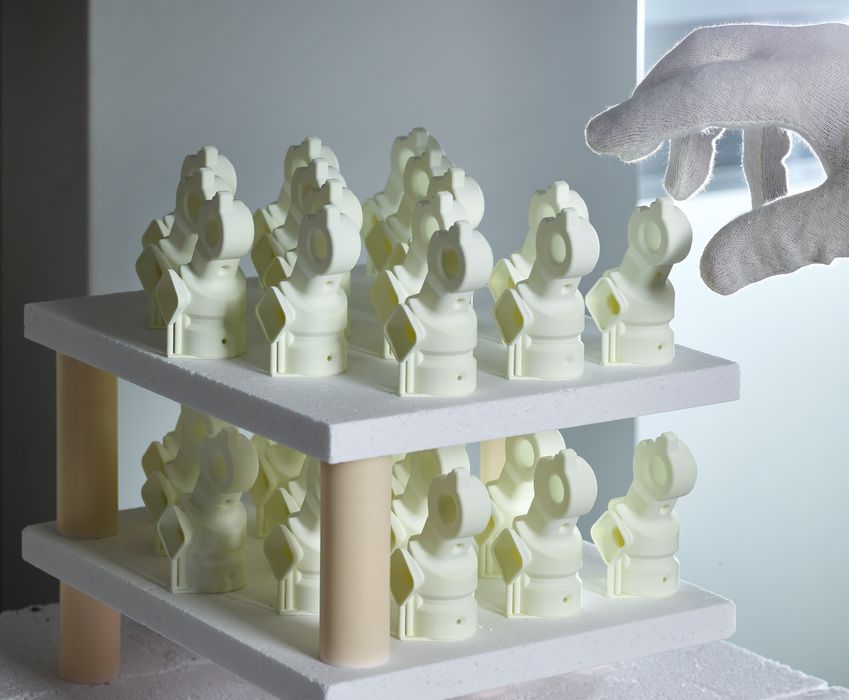
The large build volume means the Admaflex 300 can be used for serial production. Admatec explains:
āThe Admaflex 300 has an integrated high-volume material handling system with automatic vision controlled dosing to enable 3D printing of large components. It is designed to effectively handle materials with high viscosity, normally associated with ceramic slurries, enabling high reliability and speeds for continuous high-throughput and high volume production.ā
But hold on a moment ā thereās another step to the process to complete the printing process.
After initial printing, the Admaflex 300 has produced āgreenā parts. These are fragile parts that are a mix of ceramic parties and binder. Two additional steps are required to finalize the part: remove the binder and sinter the remaining ceramic particles together into a solid object. Because of the binder removal, the parts do shrink slightly, but this is known in advance and part sizes are adjusted to ensure the final part has the desired dimensions.
These steps are done in a sintering furnace, which can raise the temperatures to levels that can achieve those two steps. Admatec does market sintering furnaces to accompany their printers, the furnace volumes were tuned to their smaller equipment.
The company has now made available much larger volume sintering furnace options with volumes of 400 x 400 x 400 mm. The furnaces have a maximum temperature of 1700C.
This should accommodate the output from the large Admaflex 300 easily. The result is that the two machines involved in the ceramic process can be matched in capacity, and thus itās far easier to implement a true production line for 3D printed ceramics. Admatec explains:
āAll recent improvements in 3D printing, materials and processes, in combination with specially designed integrated debinding and sintering furnaces, currently allow to produce a set of 3D printed technical ceramic parts, from CAD design till sintered end-use part, in less than 7 days.ā
This is quite an interesting development, as it opens the door for more economic volume production of 3D printed ceramics. It may be that companies experimenting with smaller devices eventually land on a product design that sells well, leading to the need for production capacity. It looks like Admatec has that covered.
Via Admatec