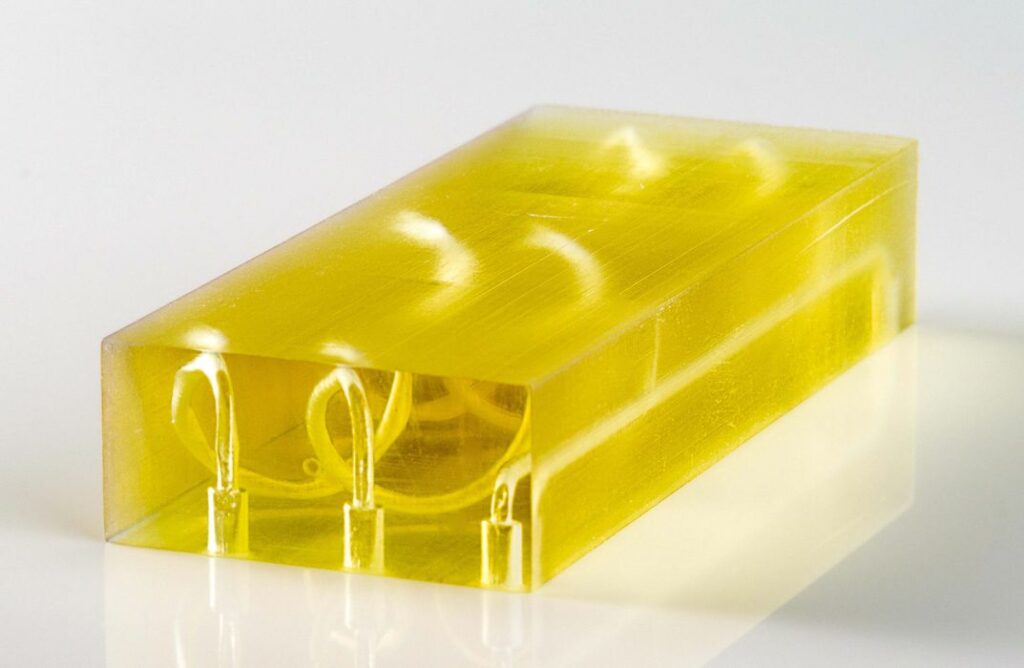
A new 3D printer resin offers the ability to 3D print certain fine structures in a way that was previously difficult.
Resin 3D printing has been around as long as 3D printing has existed, but the principles remain the same: energy is applied to a liquid photopolymer resin, which is selectively solidified when a region within the resin receives sufficient energy.
There are plenty of ways to deliver that energy, including by direct laser, masked SLA with LCD panels, DLP, etc.
But all of them suffer from a persistent problem: overcuring.
Overcuring occurs when energy happens to drift into 3D regions of the resin that were not intended to be solidified, but do so because they happened to get hit by enough energy to trigger polymerization.
How can this happen? It’s all because of those photons.
When the photons are released from their source in the 3D printer, they will continue traveling until stopped. Normally that is the resin itself, as the resin can absorb some photons, and that triggers the polymerization.
But what if you were 3D printing in transparent resin? By definition the photons travel through transparent material, at least a lot more than they do in opaque material.
This means that it is possible that stray photons may “leak” above the build plane in the 3D printer, and accumulate energy in other places where polymerization could occur.
Consider this diagram showing how this problem can occur:
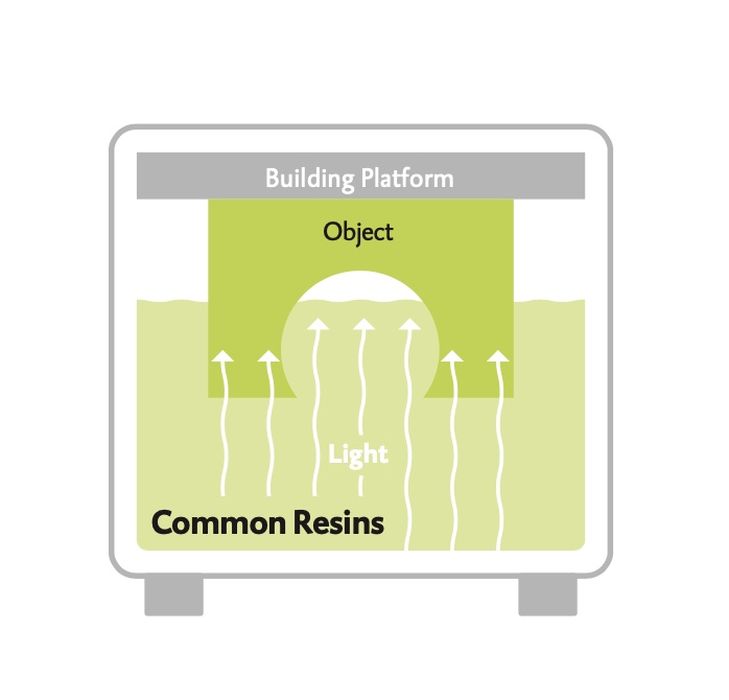
Notice that the energy travels up to the build plane, but in the voids can also travel farther up, where it could be absorbed and cause off-plane polymerization.
In today’s resin 3D printers and materials, operators attempt to overcome this by carefully tuning the exposure parameters to ensure the intended structure is built, but keep overcuring to a minimum.
Unfortunately there are some pathological geometries that are usually impossible to 3D print because of this problem, in spite of any tuning that’s taken place.
One of these geometries is tiny capillaries, where the cylindrical shape can be compromised.
This is where the new Moiin resin comes in. Their chemists have apparently designed the resin to have a slightly different energy absorption curve that will create a “cure depth barrier”. This is essentially a distance beyond which curing cannot occur, and that should eliminate many types of overcuring.
This diagram shows how it works:
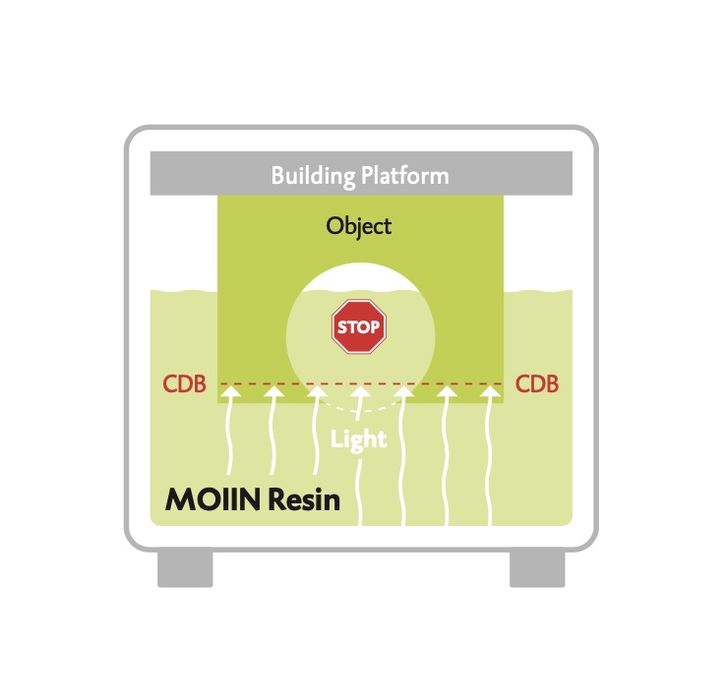
As you can see, a tiny capillary could indeed be 3D printed in resin using this material. DMG said the diameter could have an inner diameter of only 1mm, with a wall thickness of 0.1-0.2mm.
At top you can see a print sample using this new resin, made on an Asiga Max UV DLP resin 3D printer.
The availability of this new resin family could enable many new kinds of applications that make use of this geometric style.
Via Moiin