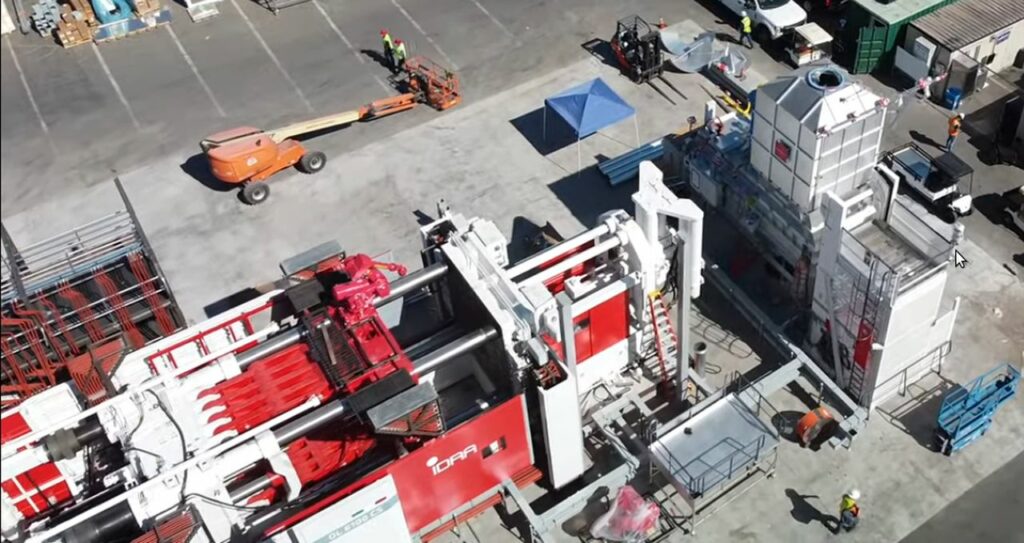
Automaker Tesla could use a new 3D printable steel alloy to build electric vehicles in the future.
Of all the automakers, it would appear that Tesla is certainly among the most innovative. The company has spent considerable effort attempting to streamline manufacturing with a goal of reducing costs and increasing factory throughput.
One of their many manufacturing innovations is the use of something called a āGiga Pressā. This is a massively-scaled casting machine.
The idea is to cast a few very large parts instead of making dozens or hundreds of smaller parts and then assembling them. This concept dramatically reduces the amount of work required to build vehicles simply by eliminating many parts. It also simplifies maintenance, reduces parts administration work, and increases vehicle reliability.
With all those benefits, one might ask why automakers havenāt done this previously.
There is a reason: cooling. When very hot liquid metal enters the casting machine and forms the desired shape, it must cool down, and that takes a bit of time. This is normally not an issue, as small parts have a low volume to surface area ratio, and they cool quickly.
However, when you scale up the parts that ratio changes and it takes far longer for the parts to cool down. If they arenāt sufficiently cooled, they can distort when pulled from the casting machine. But leaving the parts in the machine longer means there is far lower throughput and the process becomes uneconomical.
As a result, casting has been left to smaller parts until now.
The Gigacasting approach is to actively cool the part as fast as possible. This is done by including cooling channels within the casting die. These channels can carry cooling fluid, that increases the cooling rate of the part and thus increases part throughput through the Giga Press.
Readers will certainly realize that such dies could be 3D printed: embedding complex channels that follow the surface path of the die could easily be drawn up in CAD and reproduced using metal 3D printers.
However, there was an additional problem: the die itself has to be made from extremely hard tool steel to withstand repeating use.
Now it turns out that a special tool steel has been developed for just this purpose.
According to a report from MIT, this new metal was developed using an advanced materials simulation and prediction approach called āCALPHADā. MIT explains:
āThe team began designing the new metal using CALPHAD, a method for calculating the properties of materials. Using thermodynamic material models, the team could predict what new materials would do in different conditions.ā
Researcher Florian Hengsbach explained:
āThis was very successful. Weāve designed a very promising tool steel, with superior performance regarding thermal conductivity, hardness, and toughness, which can actually be printed.ā
Apparently the formulation of the new steel alloy is in the process of being patented, making commercialization just a matter of time.
The result of this new materials development will certainly be expanded using of Gigacasting approaches by automakers and other manufacturers of large industrial products.
As for whether Tesla will use the material, MIT said:
āTalks with Tesla are underway.ā
Via MIT