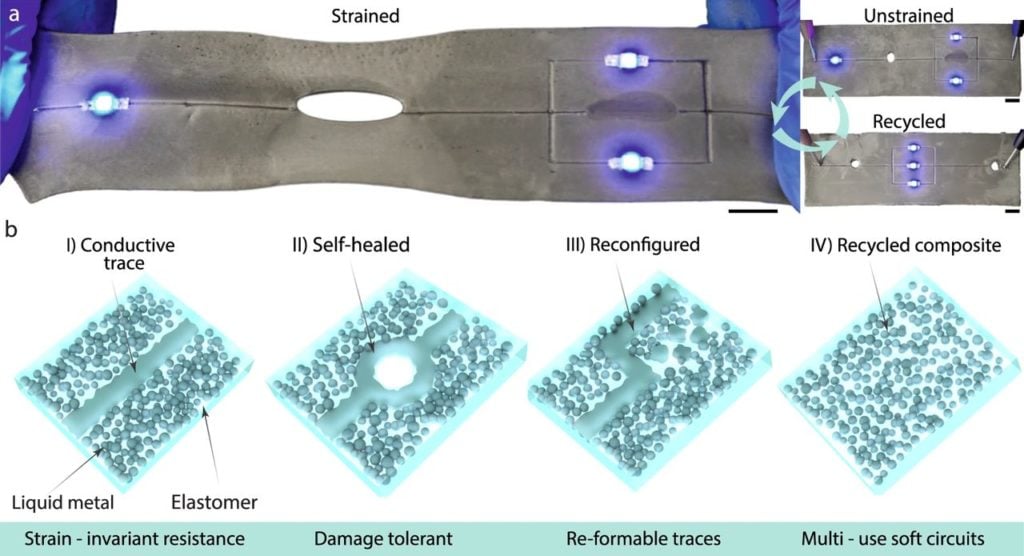
Researchers have developed an unusual material that could be of great use in 3D printing.
A team at Virginia Tech developed a composite metal material that is not only conductive and flexible, but also stretchable, recyclable and even self-repairing.
In their paper, āSelf-healing liquid metal composite for reconfigurable and recyclable soft electronicsā, they explain the finding:
āHere we show a liquid metal-elastomer-plasticizer composite for soft electronics with robust circuitry that is self-healing, reconfigurable, and ultimately recyclable. This is achieved through an embossing technique for on-demand formation of conductive liquid metal networks which can be reprocessed to rewire or completely recycle the soft electronic composite. These skin-like electronics stretch to 1200% strain with minimal change in electrical resistance, sustain numerous damage events under load without losing electrical conductivity, and are recycled to generate new devices at the end of life. These soft composites with adaptive liquid metal microstructures can find broad use for soft electronics and robotics with improved lifetime and recyclability.ā
This is a notable discovery, and one that could be highly leveraged in 3D printing applications.
There are, as the researchers point out, increasing demands for flexible products. Largely driven by the growth in wearable electronics, weāll see more and more flexible products in the future.
As I read through their paper it seemed to me that there could be a relationship between this new composite material and certain types of additive manufacturing applications.
A recent trend in the industry has been to 3D print highly unusual robotic end effectors. These are the āhandsā of industrial robots and must constantly adapt to handle different objects as their role in a manufacturing process evolves. The idea of 3D printing here is to very quickly produce new end effectors on demand at the factory, vastly shortening the wait before innovations can be implemented.
In fact, having such a capability on hand at a factory can trigger innovation that might not have occurred otherwise. Plant workers are often the first to realize new ways of working, and putting the power to change in their hands can often be quite profitable.
Today these 3D printed end effectors are typically made from a single material. It might be rigid material, or flexible, depending on the specific application.
However, what if these end effectors could be made with conductive traces embedded within them? Could this new composite material be integrated into a multi-material 3D printer to allow this to happen?
The new composite material would allow inclusion in flexible application, including grippers that bend while activated. The self-repairing capability could also be of significant use for equipment that might wear over time.
If that is possible, then the end effectors could become vastly more sophisticated, as they could receive signals from the robotic system to trigger new types of activities. Simple sensors could be designed for more complex robotic workflows.
Iām not sure I can even envision all the possibilities here, but the ability to electrify flexible 3D prints could be quite important.
Via Nature