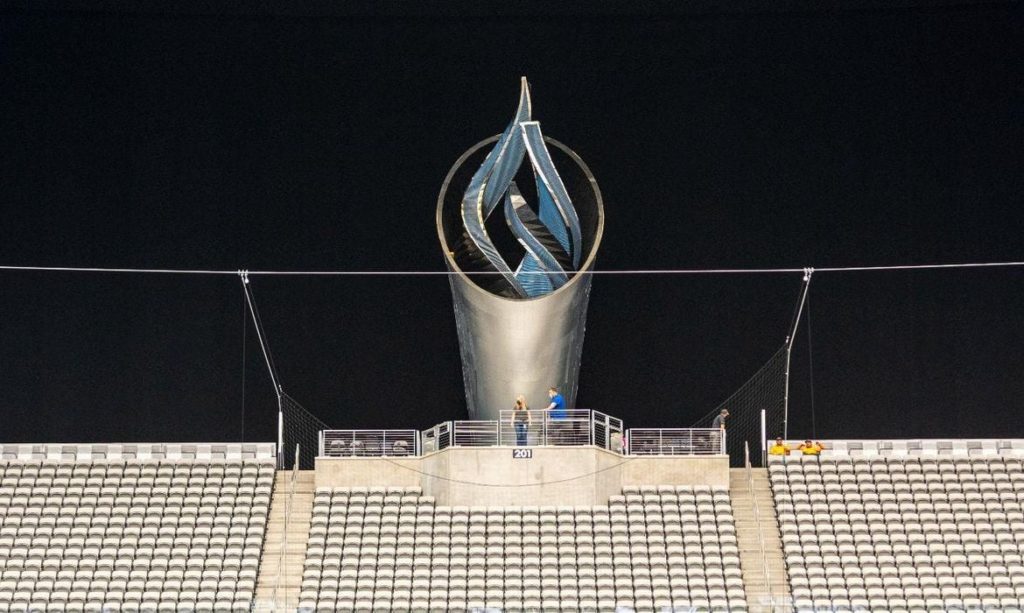
Using traditional fabrication methods just wouldn’t work, so this company took its additive manufacturing to a new level.
Allegiant Stadium is known as the Death Star to endearing fans of the Raiders NFL team, and rightfully so. The stadium is a massive, futuristic landmark on the Las Vegas skyline. Despite its futuristic design, the home of the Raiders stays true to the history of the football team with a memorial to its beloved coach and general manager, the late Al Davis.
The Al Davis memorial was part of the plan for the Raiders’ home in Vegas for some time, but it wasn’t until the team at Dimensional Innovations (DI) started on the design that things really took off.
A Massive Memorial
While the headline of “world’s largest” tends to get attention, it doesn’t give the enormity of this sculpture enough credit. The Al Davis memorial is 93 feet tall and is composed of 226 3D-printed subcomponents, each individually weighing on average 350 pounds. There are 5,580 printed layers of material (23 cubic yards) and the printed material cumulatively weighs 83,000 pounds installed.
It’s a massive structure.
When presented with the initial render, the team at DI knew that the size and shape of this structure would require some special engineering and structural calculations. While it wasn’t the most intuitive choice, the team landed on 3D printing as the solution to creating this massive piece of art.
The Al Davis Memorial isn’t just 3D printed, though. The upper 60 percent of the torch is clad in 1,148 unique aluminum panels, each custom machined to create a perfect symmetry for the tower. Altogether, assembled with the 3D-printed structure and aluminum exterior, the structure weighs 101,228 pounds.
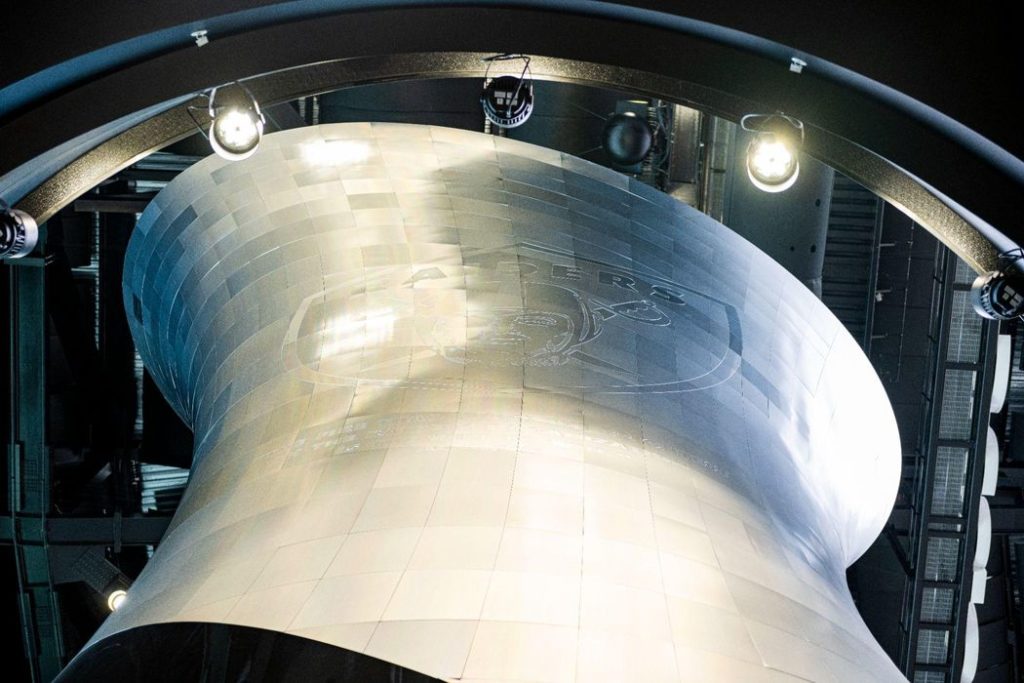
Why 3D Printing?
While additive manufacturing has gained in popularity and made advances in technical capabilities, most engineers and architects immediately wonder why 3D printing would be chosen for such a structure. Many might even think it was more of a marketing gimmick than a necessary fabrication method.
In fact, the engineering team at DI decided to use additive technologies because they made the most structural and economic sense.
“When we were approached about bringing the torch to life, there were certain constraints we had to work against (budget, appearance, weight, height and timeline),” said Brandon Wood, Innovation Lab manager. “After exhausting nearly every method of design and engineering, we determined that traditional building solutions wouldn’t work. That’s when we considered additive manufacturing as an alternative.”
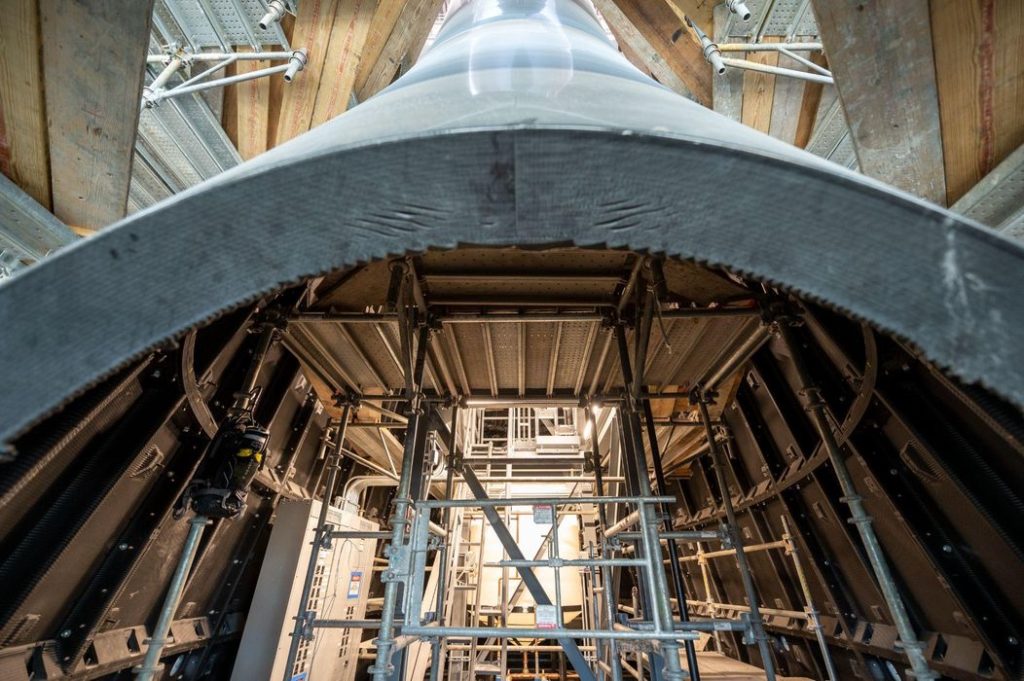
3D printing allowed the team to meet all its requirements, including being rated for fire resistance. That’s why they worked with Thermwood in Dale, Ind. to purchase one of the largest 3D printers in North America. Thermwood’s Large Scale Additive Manufacturing (LSAM) machines are designed to print using reinforced thermoplastic composite materials.
“After rigorous software development to get the machine to create something it wasn’t designed to create, we got to work building two of the massive printed parts every day,” Wood explained.
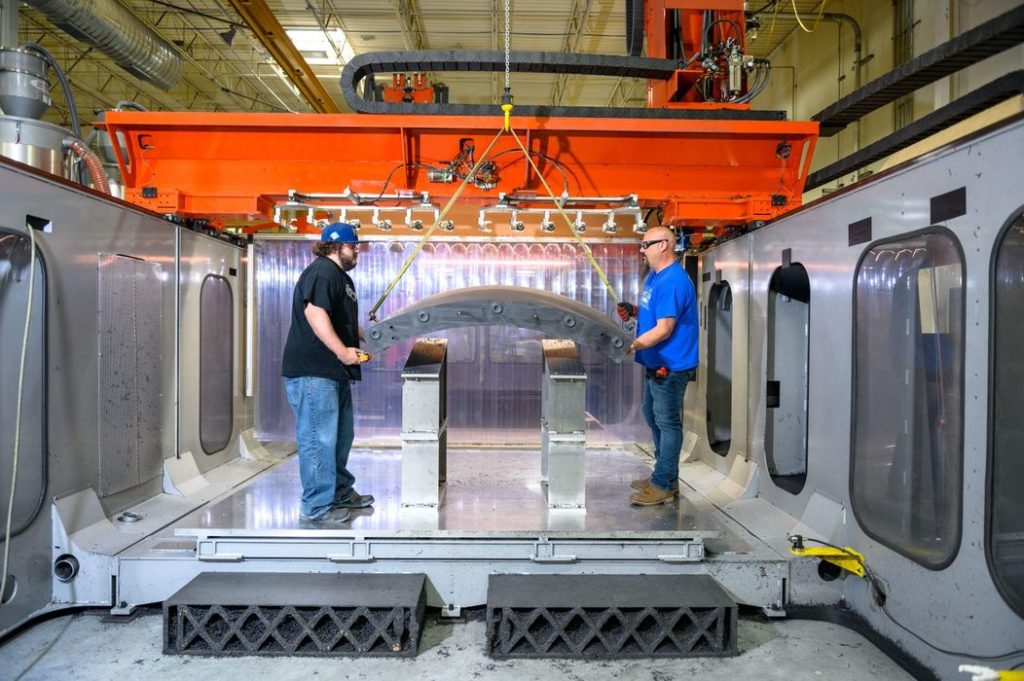
“The material choice was a critical one,” said Jared Nelson, senior design engineer at DI. “At first, we wanted to use ABS/CF because it was proven by testing and parts made by our machine OEM. ABS prints easier and is also less expensive than the material we ended up with, which is Polycarbonate reinforced with 20% Carbon Fiber by weight. ABS was eliminated because of the fire code requirements of Clark County, Nevada.”
Regardless of material, one of the challenges was staying within an ideal print temperature window due to the sheer size of the parts being produced. Just like delamination that can occur with more common-size 3D printers, a part that is too large or a print speed that is too slow can lead to layer times being too long—causing poor part strength due to layer adherence. On the opposite end of the spectrum, a part that is too small or a travel that is too fast could result in layer times being too short, resulting in sagging geometry or, in the case of LSAM, sending the machine into “hot hold.”
Ben Hansen, research and development engineer, explained, “At the time, almost all the parts being made using this new, large-scale style of FDM were either purely experimental or were more geared towards tooling. In other words, the final printed part would be the form or mold from which final parts would be made using more traditional methods.”
This is where the learning curve came in.
Read more at ENGINEERING.com