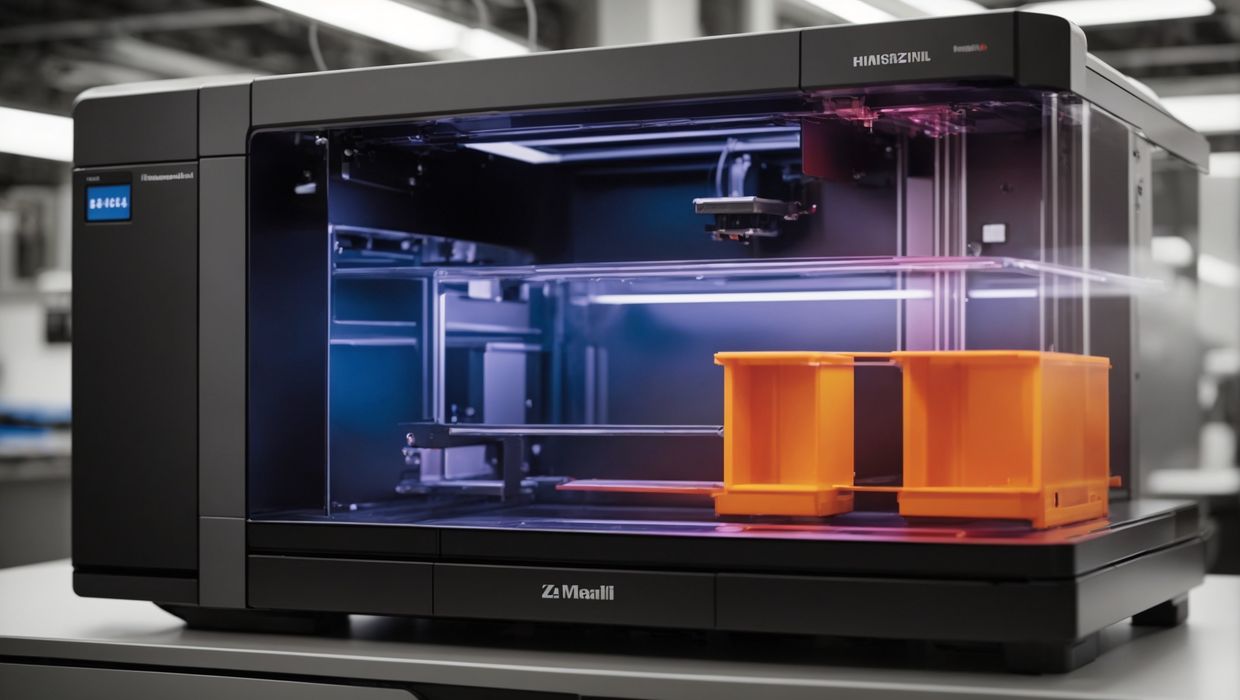
The latest 3D printers offer a slew of new features, but which ones are important?
Iāve been working with desktop 3D printers for more than 15 years, and the past year or so has been quite different ā and dramatic.
For literally a decade, desktop FFF 3D printers were rather primitive. They were often rough kits that required assembly to one degree or another, and they required considerable tuning and attention.
From the earliest machines that literally caught fire, the technology has slowly improved each year. In fact, the earliest desktop FFF machines would advertise that their motion system āhad end stopsā, or āa control panelā (many systems had none at all).
Times have changed indeed. Over the years weāve seen the gradual adoption of multiple features that are now de facto standards, such as:
- End stops
- Touch screen control panels
- Filament out sensor
- Power loss handling
- Swappable nozzles
- Spring steel magnetic print plate
- WiFi
Those, and a few more features, almost go without saying these days: you really canāt sell a FFF 3D printer today without the basic set of features.
However, innovation still happens, and new features continue to appear, particularly in the last year or so.
What are these advanced features? Which ones are important and should be considered when purchasing a machine? Letās take a look at what I consider todayās advanced FFF 3D printer features.
Active Heating
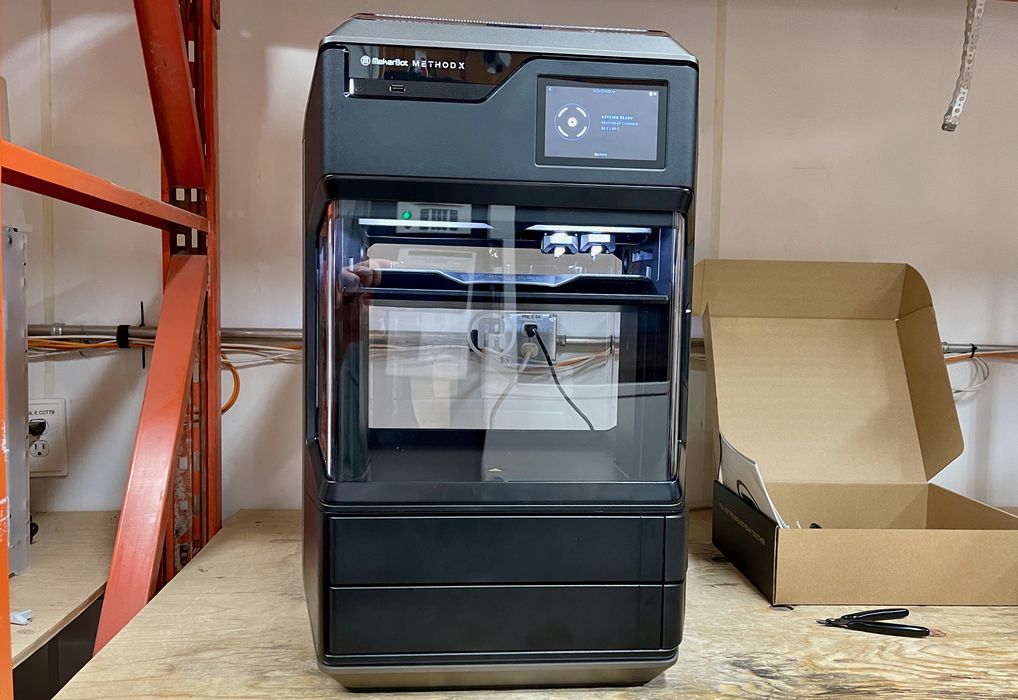
Enclosed 3D printers capture heat and reduce the thermal gradient between ambient and extrusion temperatures. In other words, they reduce the possibility warping. Most enclosures are passive, and simply retain stray heat from the hot end and print plate. However, āactivelyā heated print enclosures have dedicated hardware to warm up the chamber and keep it hot.
Flow Management
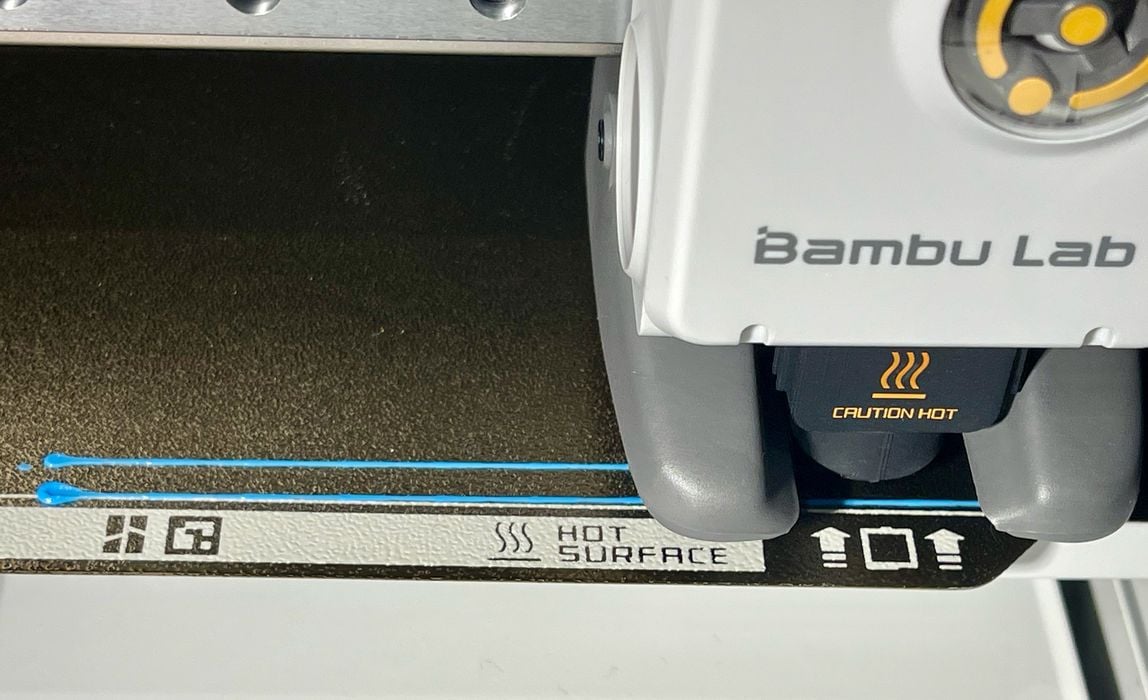
3D print jobs assume a constant and predictable amount of material is extruded from the nozzle, but that actually isnāt the case. There are situations where the filament isnāt consistently shaped, regions of density are encountered, etc. An advanced feature is to monitor the actual amount of material flowing from the nozzle and adapt dynamically to conditions. This can produce incredibly accurate prints and is quite desirable.
Vibration Compensation & Input Shaping
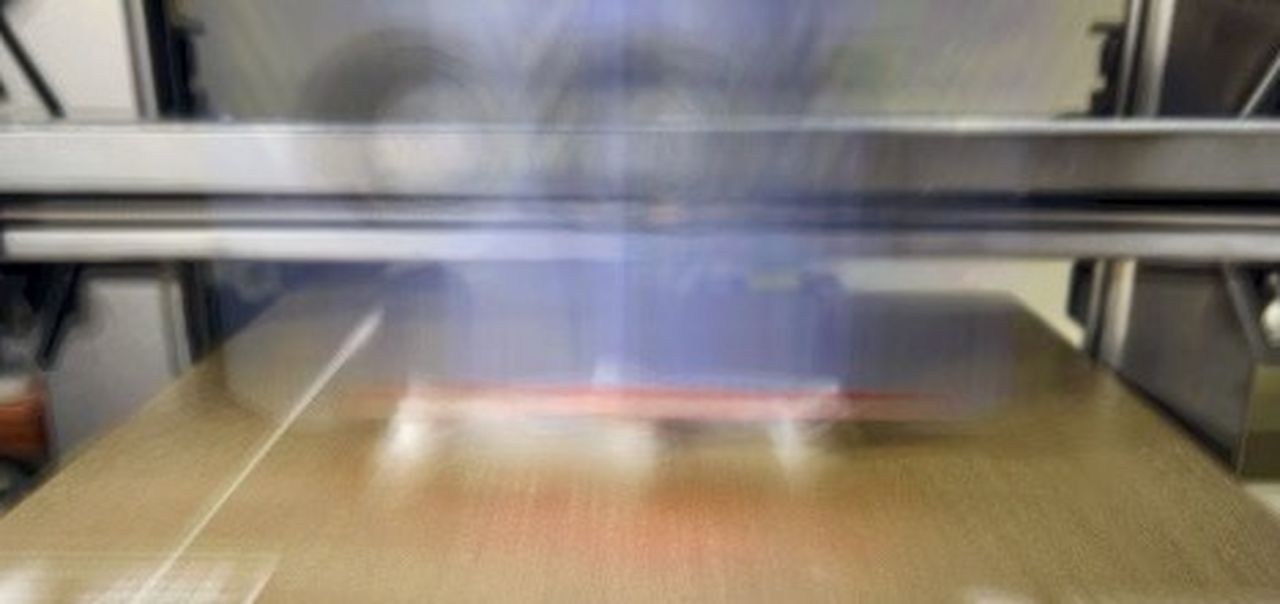
These two features, combined with a suitable motion system, can allow for high speed printing. The issues with moving at high speed are that the toolhead vibrates when changing direction at high speed, and those vibrations are reflected in the print quality. These features identify and are able to cancel these effects, leading to higher quality prints at high speeds.
Closed Loop
Closed loop systems involve components that provide feedback to the system about their current status. For example, if the 3D printerās controller requested a move of 5mm on the X-axis, did the machine actually move 5mm? Most systems simply donāt know and merely assume proper movement. A closed loop system reports the actual position and allows the controller to compensate if itās off. This makes for higher quality prints and more reliable operations.
Filament Type Detection
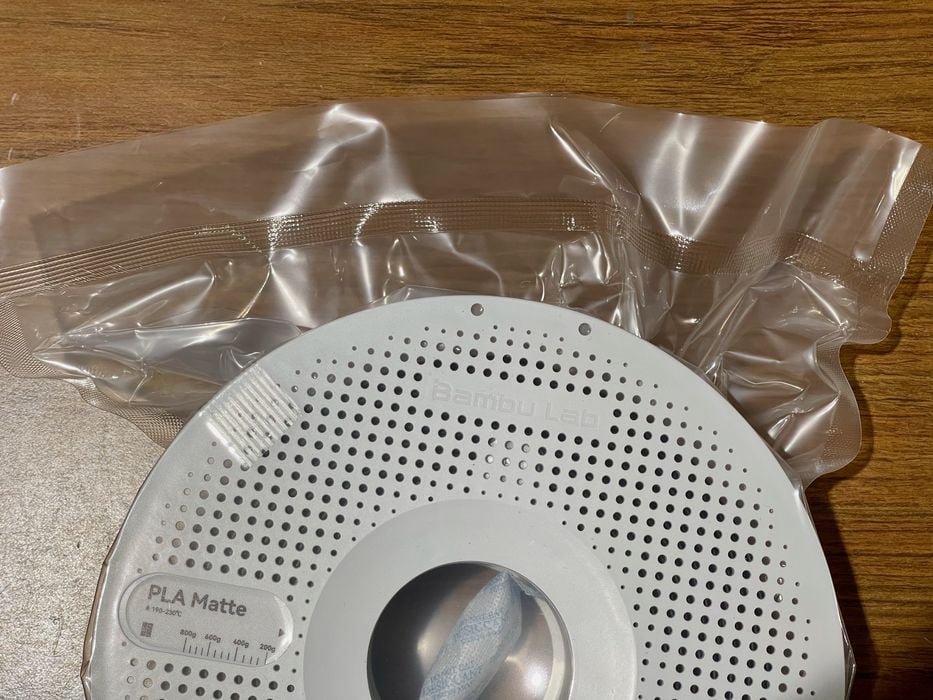
While there are no standards yet for this process, it is quite useful. For some manufacturers, itās possible to include RFID chips in the spools, and these allow the machines to identify the material type directly. If not, then the operator is responsible for ensuring the mounted spool matches the jobās requirements. Automated filament detection eliminates the possibility of mismatch.
Filament Odometer
Many 3D printers have filament out detection, but that only detects whether there is a filament or not. It doesnāt know if the filament is actually moving.
A filament odometer system observes the motion of the filament. This allows the 3D printerās controller to determine if the filament is moving too slowly, possibly due to a tangle or other filament issue. The odometer function increases the reliability of the printer.
High Flow Capacity
The combination of extruder and hot end will always have a maximum capacity: how big a volume of material can be extruded in a given time interval. This is measured in cubic mm per second, with typical machines being around 10, and advanced machines in the 20ās or even 30ās.
The idea here is that high speed printing requires more material to be extruded each second. While itās possible to run a machine with tiny layers at high speed, itās not really delivering any more material. Instead of toolhead movement speed, one should instead look for a high flow capacity.
High Temperature
For many years the only filament materials 3D printed by desktop equipment were PLA and ABS, then later PETG. Now there are dozens of unusual materials possible, and some of them have higher glass transition temperatures. In order to print them you require a high temperature capable 3D printer. These can be identified by looking at a couple of specifications, including: maximum hot end temperature; maximum plate temperature; all-metal hot end; chamber temperature.
LIDAR
There have been many different methods used for leveling the print plate by desktop 3D printers. Leveling is a process that measures the near-invisible contours of the supposedly flat build plate so that the machine can compensate for them.
Typically this has been done with a variety of sensors attached to the toolhead. Force sensors or touch sensors are most popular, with a few using magnetic approaches.
Now, however, the latest approach is to use LIDAR. LIDAR is a light-based radar system that can issue an array of light points and measure the distance to each very accurately. Some advanced desktop 3D printers are now starting to use LIDAR as their sensor for plate contours, and can create incredibly accurate and detailed maps that allow for even better first layers.
Thatās what I consider the key advanced features of todayās desktop FFF 3D printers. Do you have more that should be added to the list?
The “LIDAR” isn’t real LIDAR. LIDAR works by measuring the time it takes for light to travel out from the emitter and back to the receiver after bouncing off an object. The kind of sensor used by Bambu Lab is a laser triangulation sensor. They just decided to call it LIDAR because it sounded cooler. This has led to some people calling it a LieDAR.
What’s ironic is a laser triangulation sensor is the right tool for the job, as it’s commonly used to measure down to micrometer (micron) scales. LIDAR on the other hand is limited to around 10cm depth resolution due to the difficulties of very precisely timing the transit time of the light.