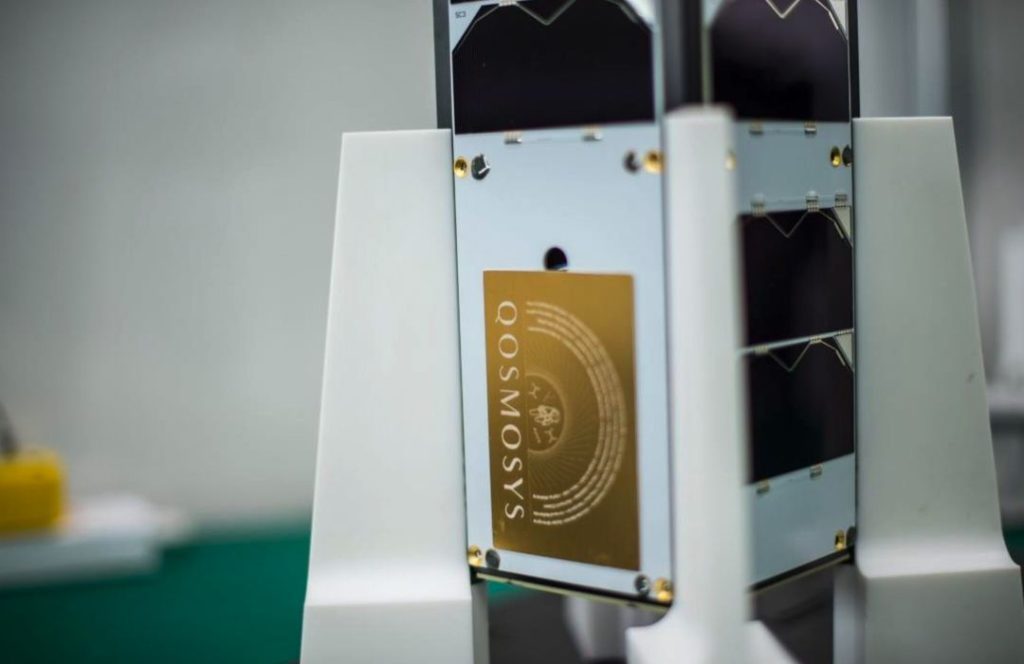
If you think 3D printing mechanical parts is tricky, try making parts for space applications.
That was the challenge facing project āGodspeedā by Qosmosys. Qosmosys is a Singapore-based satellite service provider that was to build the Zeus-1 microsatellite.
Qosmosys worked with NuSpace, a builder of micro satellites, to build the satellite hardware. One part of Zeus-1 was 3D printed, with the help of Creatz3D. Creatz3D is a Singapore-based provider of industrial 3D printing services.
3D Printing a Unique Geometry Holder for a Space Mission
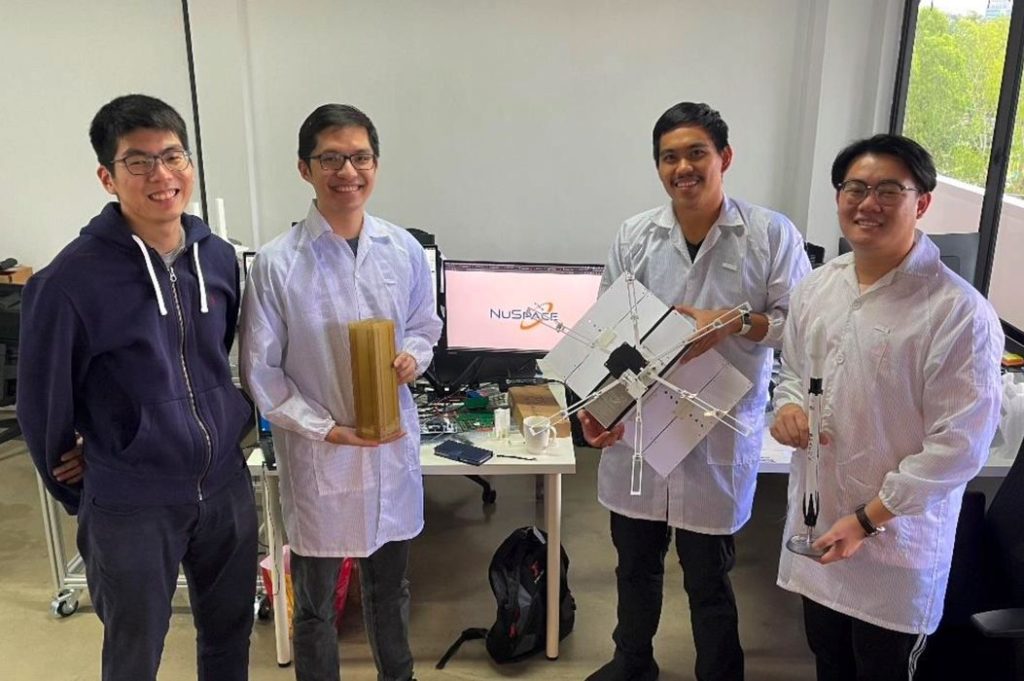
They had to 3D print a part used to hold 50 custom-made artworks that would be placed in orbit. Making such a holder is a tricky job because of the very unique geometry of each item. Even worse, developing the holder was challenging because of the coordination of all the artists.
Normally such a part would be made with CNC machining, but with the number of artists participating, it was not really feasible due to the lead times of CNC machining. Thus, the group turned to 3D printing as the answer, which could be produced in only a couple of days.
Challenges of 3D Printing Parts for Space Applications
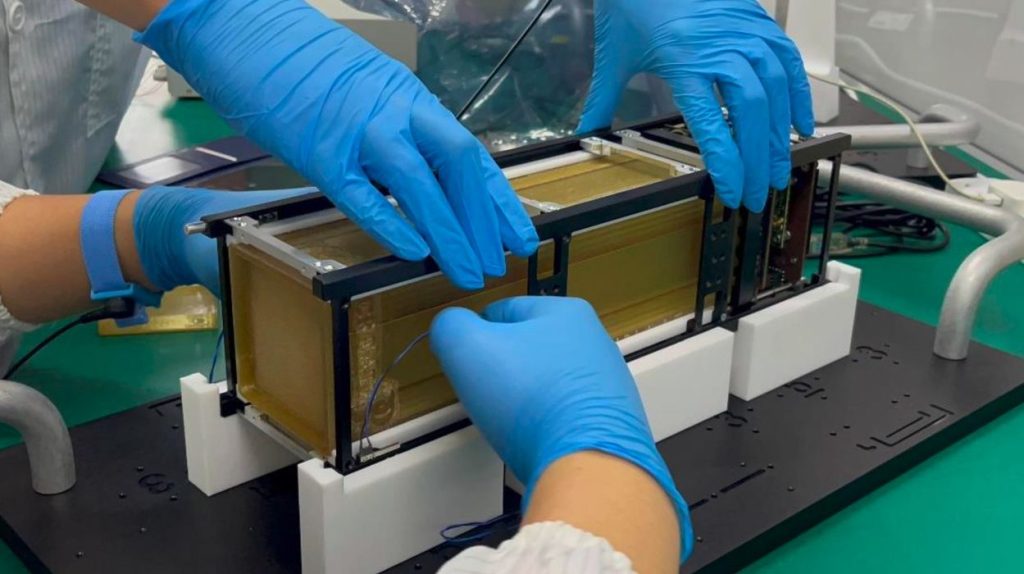
But that wasnāt the whole story. There were multiple issues to overcome simply because this part would be exposed to the space environment.
Outgassing is a phenomenon not seen in ground applications. The vacuum of outer space causes any gases within the part to be released. These can contaminate neighboring parts, and potentially compromise the spacecraft.
To solve this problem, Creatz3D recommended using Stratasys ANTERO 800NA material, which has extremely low outgassing properties, even in the extreme temperatures of space.
Weight Savings with 3D Printing for Space Missions
Weight is another issue, as the cost to launch mere grams is significant. 3D printing this holder with an unusual geometry allowed the team to save around 50% of the mass, a significant weight saving.
Itās the rule that the design of a part should withstand the conditions of its use, and thatās particularly important in space applications, where there are basically no opportunities to swap out or repair a part. It has to work the first time.
3D printing is a technology that can allow this to happen, and it seems to be true on this project: Zeus-1 was successfully launched on a SpaceX rideshare mission and deployed into orbit last month.