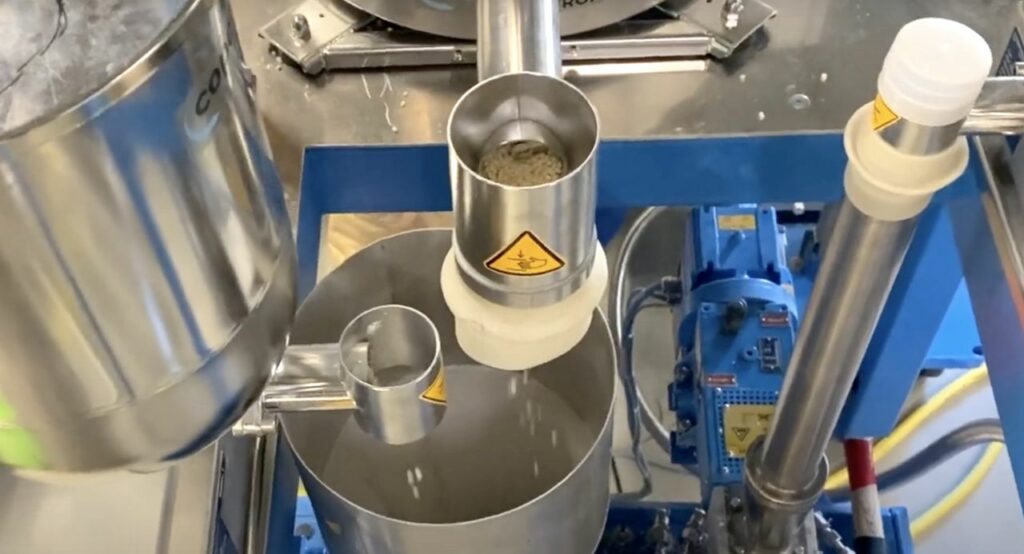
Helian Polymers is launching a new set of materials that could be the way forward for eco-conscious 3D print operations.
If you havenāt heard of Helian Polymers, you have more than likely used some of their products. Their most notable spin-off is colorFabb, producers of outstanding quality 3D printer filaments.
The company has much experience exploring new areas of materials technology, and their latest step is to launch something called āPHAradoxā.
PHAradox is a new brand of materials that are all built on the base material PHA. PHA, or Polyhydroxyalkanoate, is a natural class of polymers that is both biodegradable and recyclable, and is made from biological materials ā not oil.
PHAradox explains:
āThe main feedstock used in the production of PHAs are sugars and vegetable oils. However, in the last few years several methods have been developed in which waste water streams, plastic waste, renewable methane as well as carbon dioxide are used as feedstock.ā
Amazingly, PHA is produced naturally by emissions from bacteria fermenting material. However, PHAradox uses more industrial technology to mimic this process.
PHA has appeared occasionally in some filament products, but never in such variety.
PHAradox has produced dozens of formulations of PHA, each with different properties and for different applications. They have rigid crystalline types, as well as flexible PHA. By combining with additives, PHAradox should be able to produce a complete line of materials for almost every situation. PHAradox explains:
āPHAs have a potentially large design space and resulting application options, if properly applied. And this is where PHAradox comes in. By blending different PHA polymers, and by possibly adding some sustainable fillers or fibers, PHAradox finetunes its PHA formulations to match perfectly with the customer needs. This way PHAs compounds are created that are, for example, both high strength and tough or low crystalline but stiff.
This ability to customize PHA blends, together with extensive processing guidance, makes PHAradox able to solve a wide range of material challenges with a PHA solution.ā
To me the best part of PHA materials is that they produce no microplastics. Most other plastics mechanically break down into sand-like particles that accumulate in the environment and seep out nasty chemicals over long periods of time. PHA, on the other hand, is simply eaten up by bacteria as it has always been throughout history.
This is how most plastics should be going forward, and the 3D print industry is no exception. The vast majority of 3D prints donāt require eternal life, and having them naturally decompose is clearly what we should be doing.
As of today, PHAradox produces a wide variety of pellet and resin products for industry. Some of these could ultimately be transformed into filament form and thus usable on many desktop 3D printers, and Iām hoping PHAradox or others may undertake this step.
The new PHAradox materials will be made into filaments suitable for use in 3D printing in addition to other industrial applications, and currently colorFabb has made several filament options.
Iām very pleased to see the introduction of PHAradox, as it may eventually cause a shift from todayās ABS/PLA/PETG materials to a world of PHA.
Via PHAradox