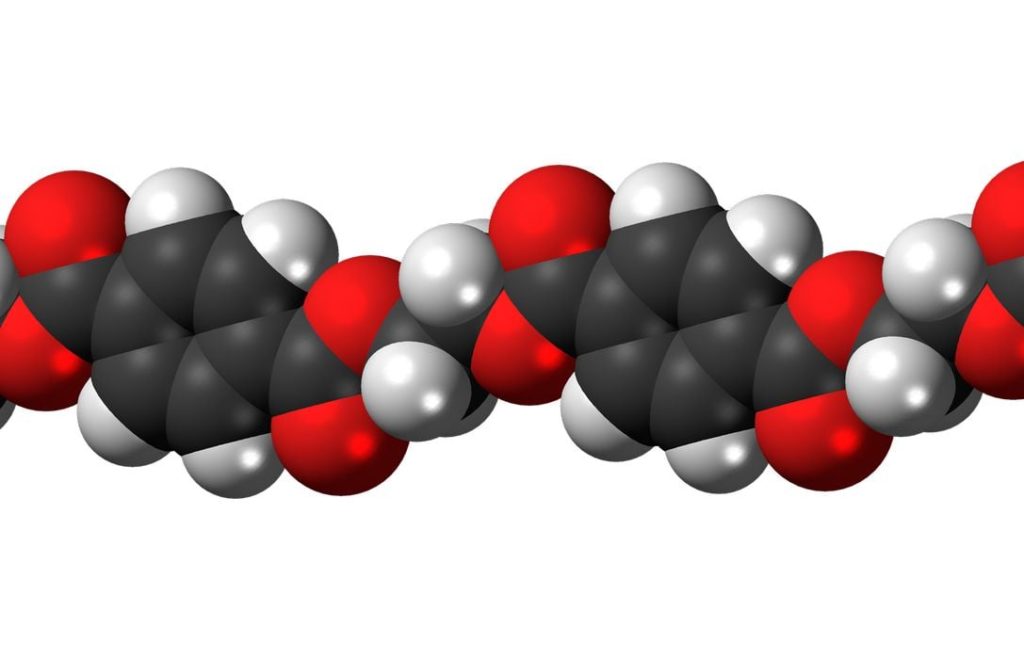
Researchers have made a technical breakthrough that could eventually change the use of recycled material for 3D printing.
Many 3D printing processes use thermoplastic materials, which can be softened by heat and reformed into new geometries. That’s literally what happens when a hot nozzle extrudes filament onto a print.
The problem is that most of the thermoplastic 3D prints end up in the landfill, even though in theory they could be re-softened and reused.
Some enterprises have developed 3D printer filaments made from recycled materials, but this has been quite problematic.
The reason for the recycling challenge is that random plastic parts are almost certainly made from different thermoplastics. Certainly there are different colors in the mix, but also the chemistry can be different: does that PETG drink bottle have exactly the same chemical mix as this other PETG bottle?
That’s the problem: while it is possible to collect thermoplastic waste, it is infeasible to recycle it because there’s a mix of chemistries. The outcome would be not only unpredictable, but also inconsistent.
Because of this there are hardly any large-scale recycled filament products on the market.
The few recycled filament operations solve this issue by obtaining their raw materials from very specific sources. For example, one operation collects drink bottles ONLY made by a specific bottling company. That mostly guarantees the scraps are the same material. Prusa Research’s recent foray into recycled material makes use of scraps from their own production line, which of course will be identical in chemistry.
But as for the 99.9999999% remainder of the thermoplastic waste, it’s a dog’s breakfast of chemicals.
If only there was a way to actually break down arbitrary polymers into base substances that could be recombined into desired materials.
It seems that fantasy might be coming true: researchers at ETH Zurich have developed a process that appears to do this. Their process is able to break down polymers into “molecular building blocks”, or monomers, of which represent over 90% recovery.
This “depolymerization” process has been successfully used to recover monomers representing 92% of a polymethacrylate sample. The process involves heating the sample to 120C, which creates radical molecules that cause the depolymerization to occur. Apparently it may also be possible to speed up the reaction through the use of a catalyst material.
The process is said to be expensive, but that it could through scale and further research be made commercially viable.
There is one issue: the process apparently will not work on many of today’s most common polymers. The researchers suggest that switching chemical production to slightly different chemistries would permit this process to work on a widespread basis, which is the likely long-term outcome of this research. It is possible future research might uncover a method of depolymerizing current materials, but there isn’t one yet.
When that happens we would expect to see proper plastic recycling plants appear in major centers, which would then accept all manner of scrap plastic. The monomers produced at the recycling plant could then be sent to chemical companies for use in creating new, fresh polymers, including 3D printing materials.
When that day comes we’ll be able to see a recycling symbol on our box of filament and know that it actually means something.
Via Phys.org