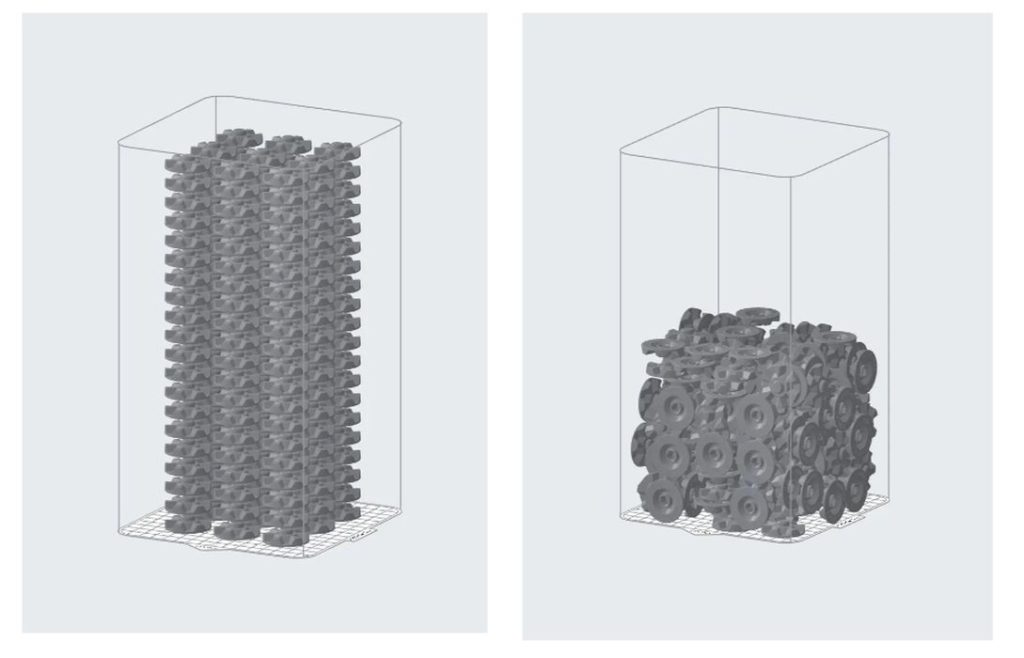
With the shift towards production from prototyping, 3D print software needs to follow a similar trajectory.
In the past few years there has been increasing emphasis on using 3D print technology for production manufacturing, rather than its more traditional role of prototyping.
Prototyping has been the mainstay application for 3D printing since its inception three decades ago, but only recently has a dramatic turn towards production occurred.
This shift has largely been due to the availability of 3D printable materials suitable for end-use products. Early 3D printers were able to use materials that were fragile or provided less ability to withstand production environments, and thus many engineers dismissed the technology as “not ready”.
Well, that changed with the emergence of proper engineering materials on the scene. First with metal 3D printers, and then with polymer 3D printers, there are now many choices on the market for 3D printing parts in dozens of advanced materials. 3D printer manufacturers are often seen integrating materials libraries into their software to facilitate easy use of the materials, and essentially push a transformation by manufacturers towards additive approaches.
So far it’s been clear there have been two changes: hardware has become production capable, and so has the selection of materials. But there’s another step required: software.
There are indeed many production-capable software suites on the market, but given that many 3D printer manufacturers produce their own software, production capability is not always guaranteed.
Indeed, many production 3D printer manufacturers of today have only recently become so, having “graduated” from smaller DIY or prototyping devices in the past. While their hardware has become production-ready, their software has to also become production-ready.
One excellent example of this transformation was seen from Formlabs recently. The company has long produced highly-competent desktop equipment suitable for prototyping and more recently production applications when organized into arrays with their Form Cell system.
However, Formlabs also introduced the Fuse 1, a very different 3D printer. Not only does this device use an entirely different 3D printing process, SLS, but it is a low-volume production machine. If you buy a Fuse 1, you probably want to run it as much as possible to support its acquisition cost.
Like all Formlabs equipment, the Fuse 1 uses the company’s very easy-to-use PreForm software. I’ve long said it is the easiest 3D print job preparation software I’ve ever used, and so it’s understandable that Formlabs would want their Fuse 1 clients to use it as well.
Last week Formlabs provided an interesting update to their PreForm software to make it much more attractive to production operators. A new packing function provides a way to dramatically increase throughput on the system.
“Packing” is a feature unique to powder-style 3D printing processes, where it is possible to produce parts in 3D space within the build chamber, rather than attached to a build plate: that’s what I would call “2D 3D Printing”.
SLS system operators have a goal of packing in as many parts into each job by Tetrising them together. Then the printer runs overnight and produces all the parts.
This has long been possible on the Fuse 1, as they always included a standard “array-style” packing function. A part would be geometrically repeated over all axes to fill the build volume.
But now PreForm has a much more advanced packing algorithm. Let’s take a look at an example.
At top you can see two build chamber setups. On the left is PreForm’s original packing algorithm, which is notably aligned along all axes. On the right is the same parts, except packed with the new PreForm packing algorithm.
Formlabs said this example has 108 parts being printable in 32:14, going down to only 26:35 in the denser-packed scenario.
Their algorithm doesn’t simply repeat the part in a pattern; instead it finds ways to rotate the parts so that they can fit in the tightest manner possible. This makes much more effective use of the build chamber.
Since the duration of a print job is proportional to the number of layers, these denser job packs print faster. Alternatively, more parts could be packed in above to fill the build chamber and achieve maximum part throughput.
Here’s another example:
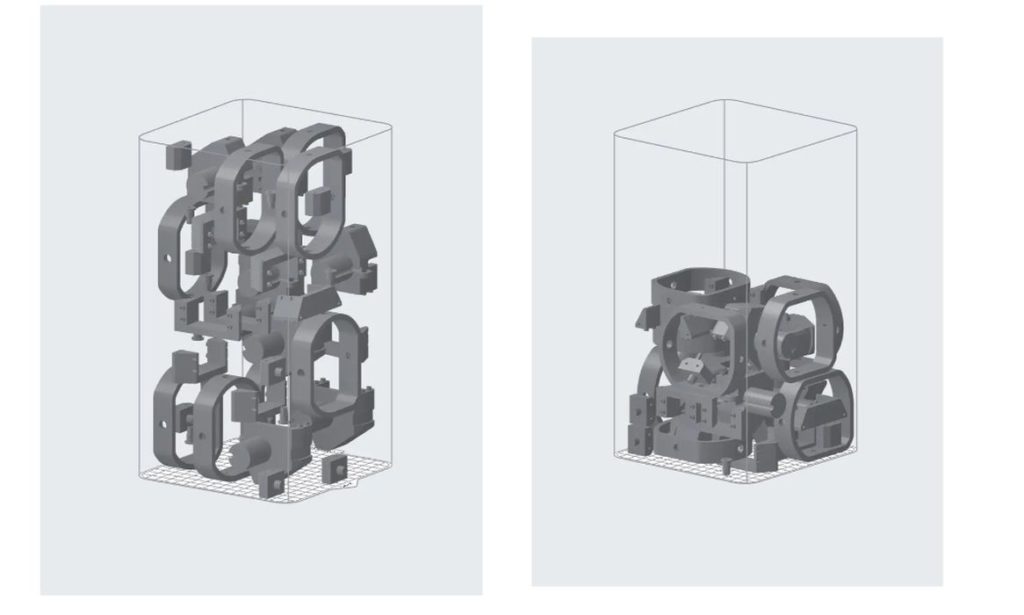
In this example, Formlabs said the print time decreased from 33:34 to 24:12. Formlabs said they typically see a reduction of about 29% in job print time, but there is also the matter of increasing part throughput, which will decrease the unit cost of every part produced. In other words, this software just made the cost of Fuse 1 printed parts less expensive.
There is also a corresponding saving in material, because less fresh powder becomes “used” powder, which has some restrictions on future reuse.
This impressive algorithm demonstrates the importance of software for production 3D printing. It’s not just about hardware and materials.
Via Formlabs