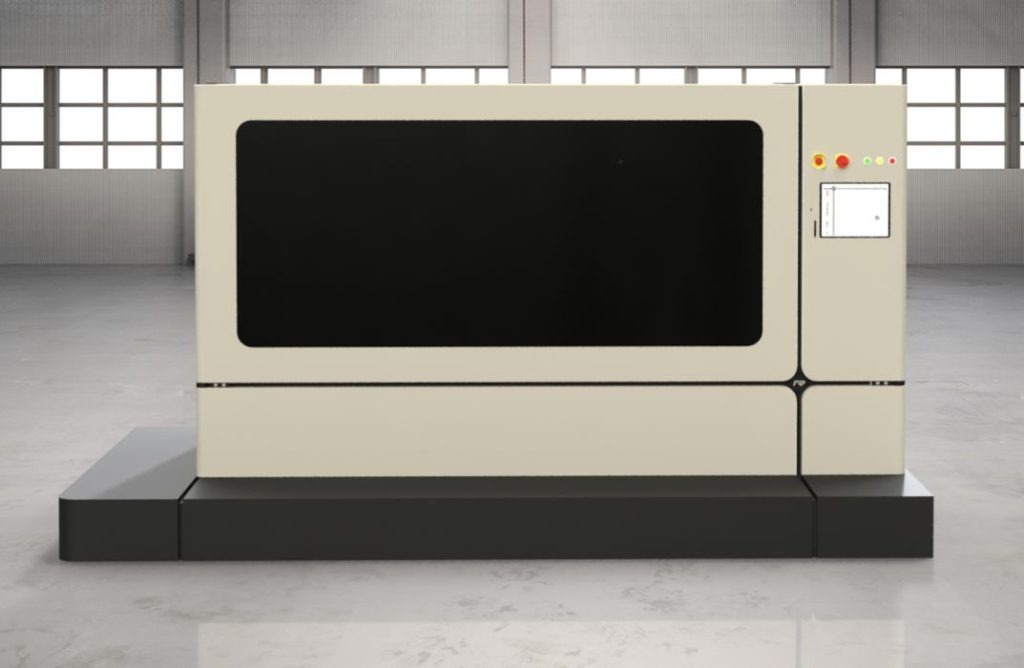
Raplas has a broad product set including both resin and powder-based 3D printers.
While not as well-known as some other larger players in the production 3D printer manufacturing space, UK-based Raplas has quite a wide selection of equipment and materials. They offer both polymer and metal 3D printing solutions.
The company’s history, however, is based on resin 3D printing, where their current set of products are positioned. Their present resin equipment includes a series of machines that offer different build areas:
- PR450 (450 x 450 mm)
- PR700 (700 x 700 mm)
- PR800 (800 x 700 mm)
- PR1600 (1600 x 800 mm)
- PR2400 (2400 x 800 mm)
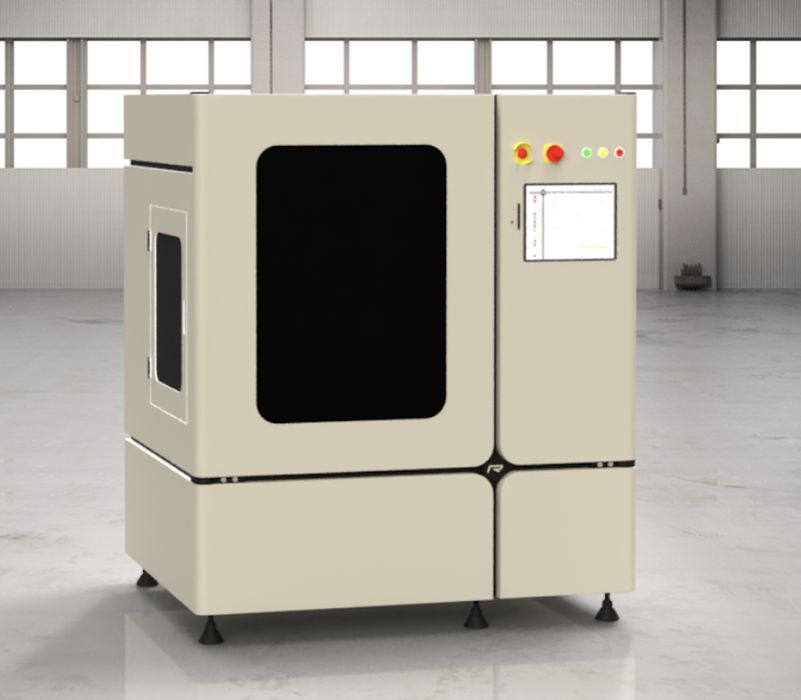
All of these machines include powerful features, including:
- Solid granite and metal build frame for rigidity
- Large doors for easy access to prints after completion
- Materialise MAGICS software included
- Factory-style touchscreen interface with EPO switch
The laser system on these machines is quite interesting. Rather than using the typical “fire the laser through the bottom of the resin tank” approach, the Raplas machines fire the laser from above to strike the flat surface of the resin. Of course, this means the machines must be perfectly level when operating.
To print a second layer, the Z-axis moves down a small amount, and a recoater arm pushes liquid resin over for curing. This results in a print speed that’s somewhat faster than typical resin machines, but not quite as fast as others using continuous printing approaches. One big benefit, however, is that there is no tank to wear out: the prints are easily peeled off the build plate at job conclusion.
Something I noticed in the company’s video is that they seem to have perfected support structures. In the video you can see the operator easily peeling off supports as if they were “breakaway” supports made from a different material. However, the supports are made from the same resin, and Raplas must have very carefully tuned the exposure settings to ensure the supports are very delicately attached to the print. That makes for easy removal as well as limiting surface effects on the print.
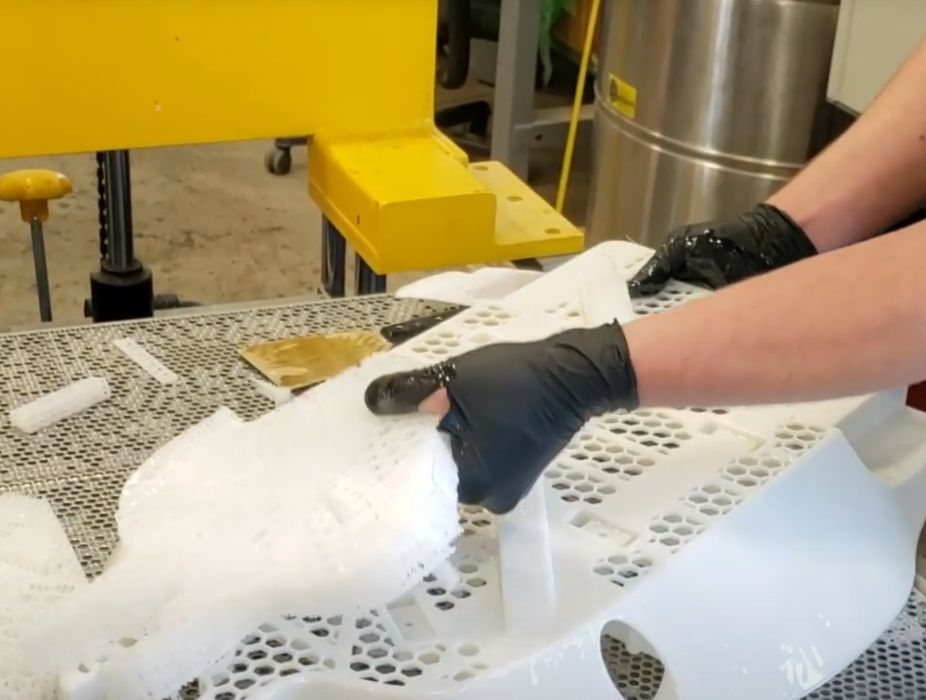
All of these machines are targeted at production environments, where quantities of parts are made job after job. One feature that should aid this process on some models is a removable resin tank. This would facilitate very easy material swaps.
In fact, material swaps should be vastly simpler on this style of equipment than typical resin gear where one has to clean out any trace of prior materials. In Raplas’ technology, no parts touch the resin other than the tank: there is no build plate dipping into the resin that must be cleaned.
It seems that the company has significantly refined their resin 3D printing process over the years.
Meanwhile, the company is also developing two new lines of 3D printers.
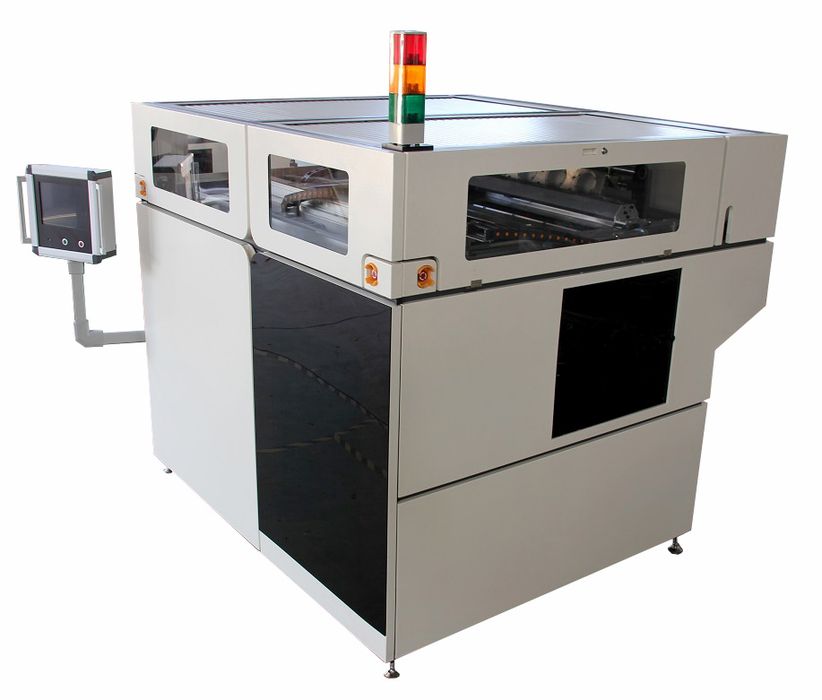
One is a powder-based solution, the PP850 and PP850+. The process uses a liquid binder to fuse together parts from powder. Raplas said the machine should be able to handle several very different materials, including:
- Sand
- Ceramics
- Cerabeads
- Inert powders
- Metal Powders
Speaking of metal, they are also developing a new metal 3D printer, the PM300. There are no specifications for this device, but it will surely inherit many of the learnings the company has gained from previous machines.
Via Raplas