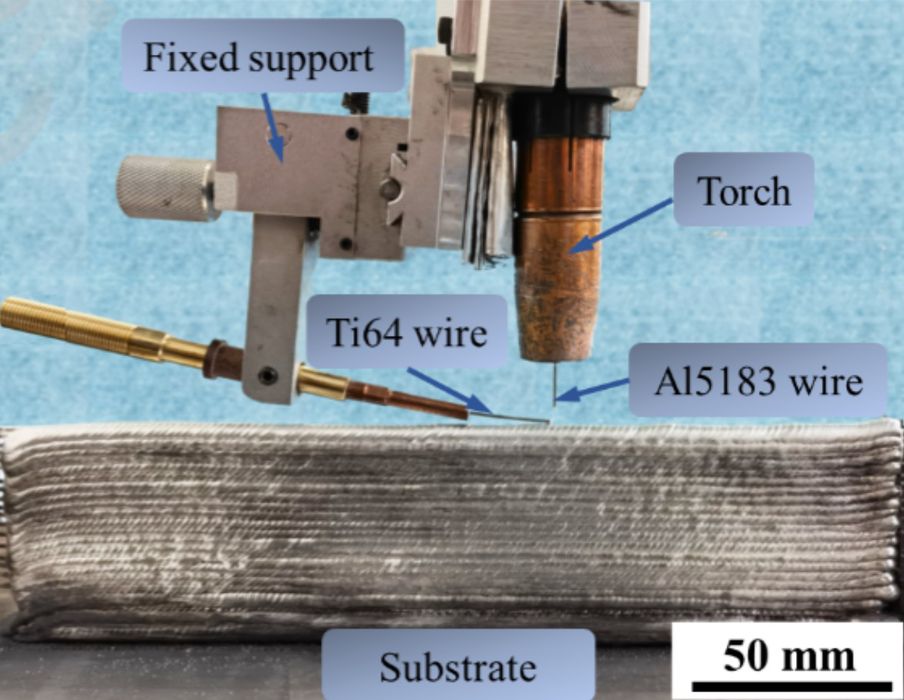
Chinese researchers have developed a way to reinforce 3D printed aluminum with titanium wire.
Reinforcing materials is not a new approach to 3D printing. Many of the most common polymers used in 3D printing are quite fragile, and for many years that prevented their use in end-use scenarios.
That began to change when more interesting high temperature engineering materials began to emerge, but also when reinforced composite materials showed up.
The most common form of composite 3D print materials use chopped carbon fiber. The fibers are mixed with the polymer and indeed greatly strengthen the part. Some companies, like Roboze, say that these parts are sufficiently strong to be able to substitute for metal parts in many low-thermal situations.
However, chopped carbon fiber is nowhere near as strong as continuous carbon fiber. A few companies, including Markforged and Anisoprint, have developed 3D printers that can lay down continuous strands of carbon fiber during polymer printing to make incredibly strong parts.
Take note that all of these reinforcing methods are being used on polymer materials. Iāve never heard of reinforcing metal materials, as the typical approach is to try different metal alloys to increase part strength.
Now it seems there is actually a way to use continuous metals in a similar composite manner.
The researchers used a WAAM system as their base.
The WAAM approach involves extruding a solid welding wire into a laser or electrical arc that instantly melts the material. The printhead moves around in 3D space to gradually build up the object. This technology is well-understood in the 3D print space, being used by companies like Meltio and MX3D.
The modification by the researchers was to include a second wire feed. They chose aluminum as their base material, and titanium as the secondary reinforcing material. Note that titanium has a vastly higher melting temperature than aluminum.
The temperature difference allowed for true 3D printing of the aluminum, but embedding a strand of titanium in the aluminum structure, layer by layer.
The researchers found that the bonding between the metals was sufficient, and in all the parts produced by this method were found to be 120% stronger. Thatās quite a significant jump.
Aluminum is a popular material because it takes less heat to melt, but at the same time it is no where near as strong as other commonly used additive metals, such as stainless steel, and of course, titanium.
This new approach seems to enable the production of lightweight aluminum parts that are notably stronger than pure aluminum parts ā all while not requiring significant heat increases.
This is a new approach that we have not yet seen in any commercial metal 3D printer, but it would seem like an interesting possibility for a startup or a company already offering WAAM such as those mentioned above.
Via ScienceDirect (Hat tip to Benjamin)