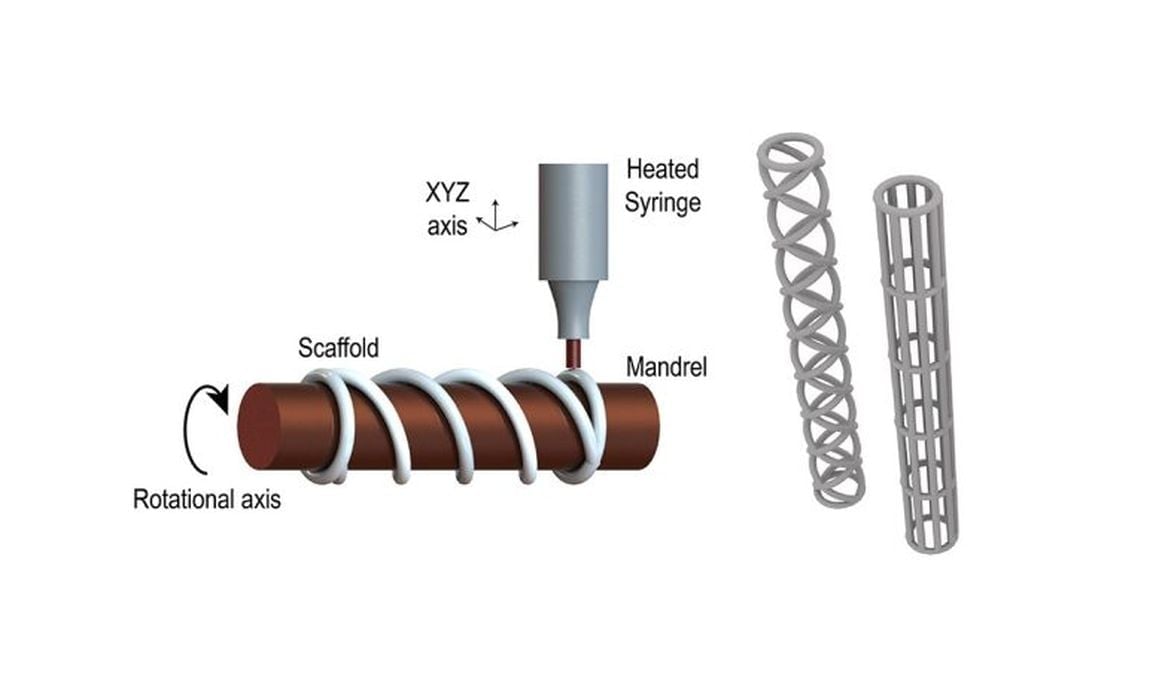
The study led by MERLN Institute for Technology-Inspired Regenerative Medicine at Maastricht University presented a rotating four axis extrusion system for diamond and rectangular pore designs.
Many tubular tissues such as blood vessels and trachea can suffer long-segmental defects through trauma and disease. With current limitations in the use of autologous grafts, the need for a synthetic substitute is of continuous interest as a possible alternative.
Fabrication of these tubular organs is commonly done with techniques such as electrospinning and melt electrowetting using a rotational collector. Now a new method called melt-spinning and developed by MERLN researchers, based on a rotating 4-axis extrusion AM system could prove more efficient.
Current additive manufacturing (AM) systems do not commonly implement the use of a rotational axis, which limits their application for the fabrication of tubular scaffolds. InĀ a new studyĀ from the Department of Complex Tissue Regeneration, MERLN Institute for Technology-Inspired Regenerative Medicine, at Maastricht University and the Advanced Polymer Materials Group, University Politehnica of Bucharest, researchers developed a four-axis extrusion-based AM system similar to fused deposition modeling (FDM) has been developed to create tubular hollow scaffolds. The new additive process was dubbed āmelt-spinningā.
A rectangular and a diamond pore design were further investigated for mechanical characterization, as a standard and a biomimicry pore geometry respectively. Three-point bending analyses revealed that the diamond pore design is more resistant to luminal collapse compared to the rectangular design. This data showed that by changing the scaffold pore design, a wide range of mechanical properties could be obtained.
Furthermore, full control over scaffold design and geometry can be achieved with the developed 4-axis extrusion-based system, which has not been reported with other techniques. This flexibility allows the manufacturing of scaffolds for diverse tubular tissue regeneration applications by designing suitable deposition patterns to match their mechanical prerequisites.
AM techniques, such as fused deposition modeling (FDM), bioplotting and other extrusion-based technologies, are suitable for increasing the mechanical integrity of a scaffold by manufacturing fibers with hundreds of micrometers. The main limitation in creating a tubular construct with current extrusion-based setups is the designs and geometries that can be manufactured, since for these overhanging and hollow structures a support material is required.
This limitation is mainly caused by the fact that most systems use a layer-by-layer fabrication approach by subsequently depositing fibers to form an infill of each layer within the object contour and this process is repeated until the full 3D object is obtained. This deposition normally occurs in a flat substrate that moves in relation to the printhead in the X-Y plane and Z direction.
The implementation of a fourth axis in melt-spinning allows the possibility to create more complex tubular scaffold designs, as also described in the field of prosthetic implants. Other groups have implemented a fourth axis in their FDM system for biomedical applications, however often without communication between the rotational axis and the main system, which results in the creation of only helical designs.
In addition to that, tubular scaffolds are generally not completely characterized by their mechanical properties and behavior for axial, radial and bending deformations.
The aim of this study from MERLN was to show an extrusion-based AM technique similar to FDM with a synchronized fourth rotational axis that allows the fabrication of complex tubular geometries. In addition, the role of geometry in scaffold design and its influence on mechanical properties, such as radial compression, tensile strength and three-point bending was further studied.
Read the rest of this story at VoxelMatters