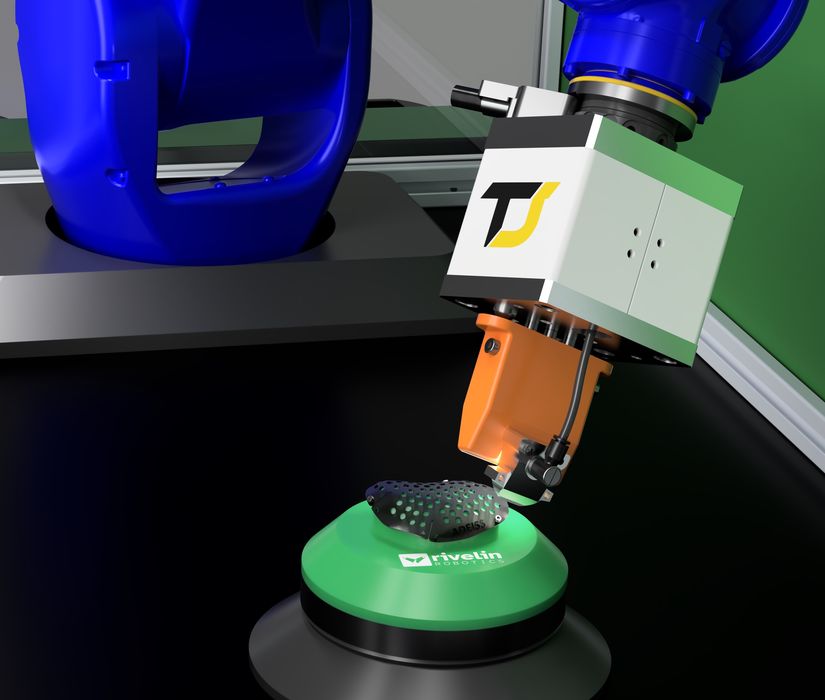
Rivelen Robotics provides a very interesting metal post processing solution for production.
Post processing is the bane of 3D printing. While everyone initially believes the parts ājust come out of the machineā, this is in fact almost never the case. There is almost always some kind of post processing involved.
That could be dusting off stray powder, finishing rough surfaces, painting or removing support structures required during printing, as is required by several 3D printing processes.
The support removal problem is challenging because it is the least possible that can be automated: the difficulty depends on the geometry of the parts being printed.
For polymer parts there has been a revolutionary solution: soluble support materials. These have finally become mature, and they make support removal almost trivial: just drop the part into a tub of solvent (sometimes plain water), and the supports dissolve away. This creates huge labor savings over the manual work that would otherwise have been spent removing supports.
Meanwhile, no such magic solution exists for metal 3D printing.
In most metal 3D printing processes, the metal parts are literally fused to a metal build plate. The parts must first be sawn off the plate, usually with a wire EDM device or similar. Then the big work begins with removal of the metal support structures.
These can be quite complex and extensive, as they are used not only for support reasons, but also to maintain part shape during the extreme thermal changes during printing. They can also be used to manage heat in the part during printing by channeling away excess heat. One way or another, thereās often plenty of support material to remove.
Traditionally this has been done manually. In metal 3D print workshops youāll often see a variety of manually-operated subtractive tools to slice, carve, smooth and drill freshly 3D printed metal parts.
While the manual approach works, there are two big issues. One is that there is a lot of skilled manual labor involved, but another is consistency.
When parts are finished manually there can be slight differences in each unit. One finisher might grind down a surface a fraction of a millimeter more than the next shift does, for example. This makes it challenging to maintain highly consistent production line, particularly if the required tolerances are tight.
Thatās where Rivelen Robotics comes in. They produce an automated system for metal support removal that, as you may suspect, uses a robotic approach.
Rivelen Robotics explains how it works:
āFor support removal and targeted finishing, Rivelin has developed NetShape Robots, an enclosed microfactory that combines an industrial robot ā equipped with an array of tools, state-of-the-art sensors and processes to ensure dexterity ā driven by the powerful NetShape control software which uses both machine learning and traditional deterministic control theory to optimise the quality and repeatability of support removal and finishing.
The result is an automated support removal solution that reduces defects by 90%, results in a 10-fold reduction in operational costs, and eliminates human risk and variability.ā
The idea here is that by using a robot to perform the support removal, it can be done very consistently between jobs. The robotās motion system is precise and will move to the same locations each time. Once set up for a given part, the NetShape Robots should be able to produce near-identical parts each time.
And thereās less manual labor required, too.
With other companies introducing highly automated and intelligent solutions for polymer print post processing, it seems clear that metal print post processing should follow a similar path.
Via Rivelen Robotics