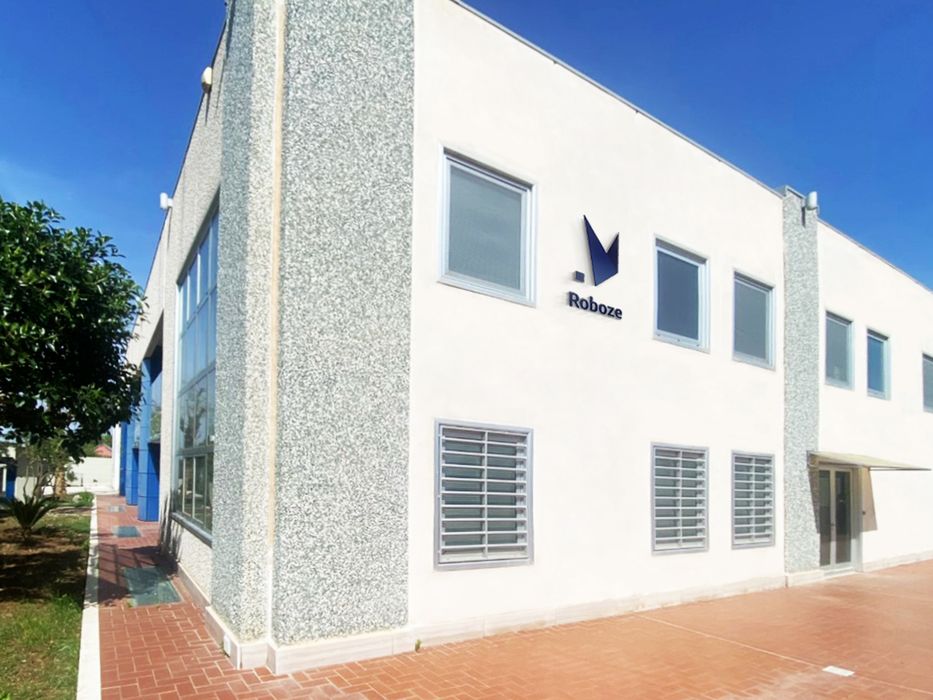
Roboze announced the opening of a new materials lab.
The lab is designed to develop what the company calls āSuper Materialsā.
The lab is located in Bari, the same city as their headquarters. It is a rather large facility of 2000sm (21,500sf), and adds to their existing space in the area. Itās expected to house up to 40 technicians to work on materials science.
Roboze is an Italian company that produce 3D printers focusing on the high temperature materials zone. These materials by definition are more heat resistant than typical 3D printing materials, and thus can be used in end-use applications in some cases.
Roboze explains their strategy:
āToday Roboze strengthens its commitment and invests in a facility that will host new materials science, chemistry and nanotechnology laboratories. The goal is to rapidly advance in the development of alternative materials to petroleum-based super polymers by favoring the use of bio-based reinforcing matrices and fibers. The challenge lies in finding new materials and technologies that can, on the one hand, reduce the generation of carbon dioxide (responsible for the greenhouse effect), and on the other hand achieve the properties of the super polymers available today in the replacement of metal parts.ā
The use of 3D printed parts instead of metal parts is a growing phenomenon. Metal parts are heat resistant, but are quite heavy compared to polymer parts. However, early 3D printed polymer parts didnāt have much thermal resistance and would collapse if used in many applications. The advent of high temperature materials allowed some operators to 3D print parts that could literally substitute for metal parts, so long as the operational thermal environment was below the softening level of the high temperature material.
For many manufacturers, this is an incredible opportunity: 3D print parts locally and avoid supply chain problems, and save weight on the parts at the same time. Lower weight is becoming a critical factor in machine design due to the increasing focus on energy use and electrification.
This all sounds good, but thereās a problem: there just arenāt that many high temperature 3D printable materials on the market. Youāll hear about PEKK, ULTEM and PEEK, but very few others. Most 3D printable high temperature materials are simply composites and remixes of the above.
In addition, there are few if any eco-friendly high temperature 3D printable materials. While of modest interest now, this factor will become increasingly important in the near future, and someone had better develop more eco-friendly high temperature materials soon.
It seems to me ā and Roboze, apparently ā that more types of high temperature materials are required if this concept is to grow in the manufacturing space. Manufacturers wonāt 3D print a part unless they can use the right material, so by broadening the choices, more printing will take place.
Roboze CEO and founder Alessio Lorusso said:
āWe have a formidable team of scientists and engineers. We constantly question the status quo of what is thought feasible and what seems futuristic, giving a precise date to this second category. Our new laboratories will allow us to rapidly speed up all developments and will give us much more opportunities to invent what no one thought possible. Our challenge in Roboze is to create 3D printing technology and super materials for a paradigm shift in today’s production model, producing high-performance parts in a sustainable way, just in time and on demand, eliminating dependence on metals and oil.ā
This is a very strategic move by Roboze, as they will not only power up their own product sales, but also encourage others in and outside of the 3D print industry to take up high temperature 3D printing.
Via Roboze