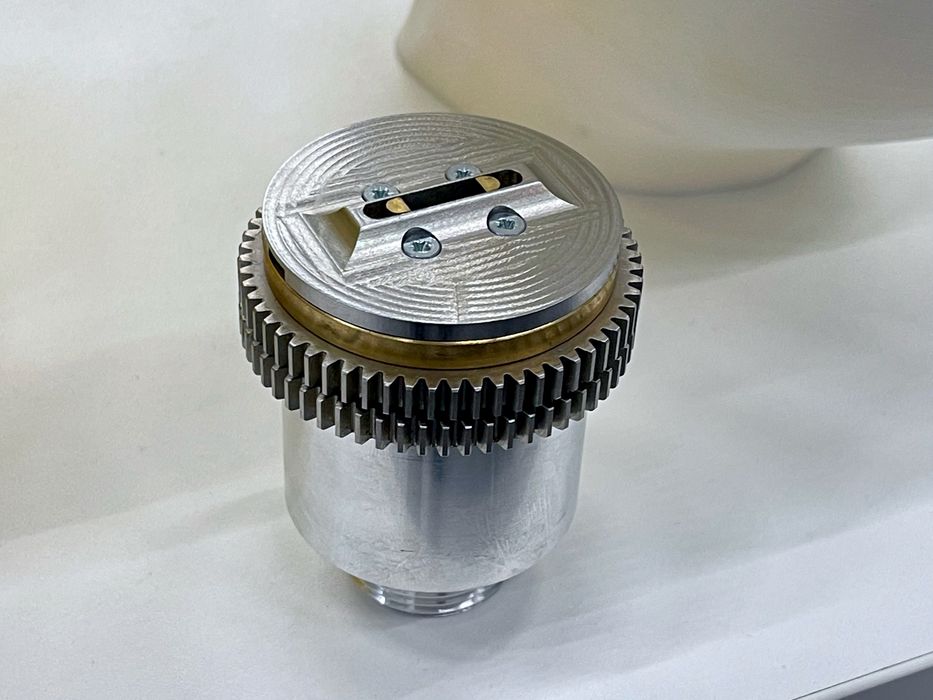
Sculpman’s variable nozzle is among the most interesting technologies we saw at Formnext.
Sculpman is a Belgian startup company that launched recently in 2019. They’ve developed a technology that seems quite intriguing, and it actually works.
The problem they’re solving is the speed of printing problem that plagues FFF devices. It goes like this: use a fine nozzle because some portions of the print will require good resolution. But then the entire print takes a long time because everything, including the portions that don’t require high resolution, are printed with the tiny nozzle.
It’s possible on some equipment to swap nozzles. The idea there is to use a “fat” nozzle for larger items requiring less resolution. However, those systems again print the entire object coarsely and there’s no opportunity for high resolution.
More advanced systems that involve multiple toolheads or tool changing tech try to use nozzles with different diameters on different tools. That works, but it’s expensive because there’s more hardware involved. It also is limited to a few different nozzle choices, usually only two.
Enter Sculpman, which has developed a “variable” nozzle. By variable, I mean it can change its orifice to ANY size. And it can do so during the print job dynamically!
There’s a catch though: the orifice is no longer a circular area. Instead it’s a rectangular area, as you can see in this image of the nozzle open and closed.
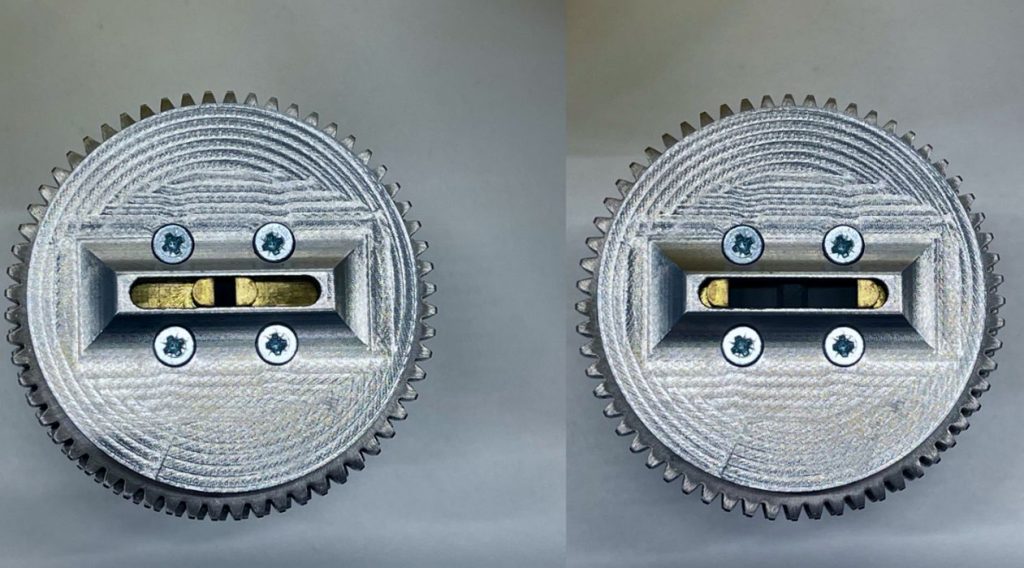
This particular unit is able to vary between 10mm and 0mm. Yes, zero: it can completely close and almost block all leaks. This would be obviously quite useful for travel moves, where no retractions would be required.
There’s another feature of this nozzle: it can rotate. Much like a calligraphy pen, this nozzle can vary the extrusion width also through rotation. This would be necessary in certain extrusion scenarios, for example printing a vase where the walls must be of equal width on all directions.
To open and close the nozzle, the unit must twist to open the diaphragm.

The advantages of such a system are immense. Consider the problem of laying down a good first layer: you could rapidly extrude centimeter-wide swaths and have it done in seconds.
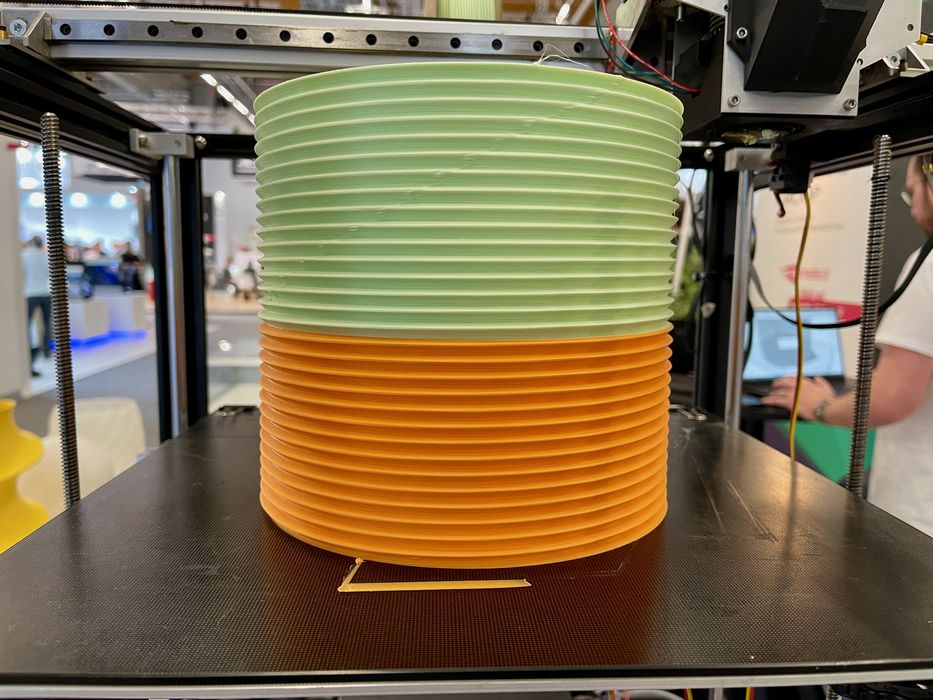
Interior walls could be made enormously wide, making them far stronger that typical “thin” prints. Meanwhile, exterior portions would receive ultra-fine treatment with a very narrow opening.
Print speeds are dramatically sped up, as we were shown large prints, such as a life-size head model, which were printed in only four hours. It’s apparently possible to tune the print to be even faster.
Sculpman representatives told us the concept could be made larger than the prototype shown to us. It’s apparently theoretically possible to have an opening as wide as 40mm.
One big complication with this concept is that the slicing software has to be a heck of a lot smarter than most tools today. The software would have to generate unique GCODE to adapt to the shape and control the variable nozzle appropriately. However, it seems that Sculpman has been able to achieve this, as we saw several prints leveraging the technology.
In fact, the system really requires a six-axis control system, with the additional motors being used to control the nozzle’s orientation and opening width.
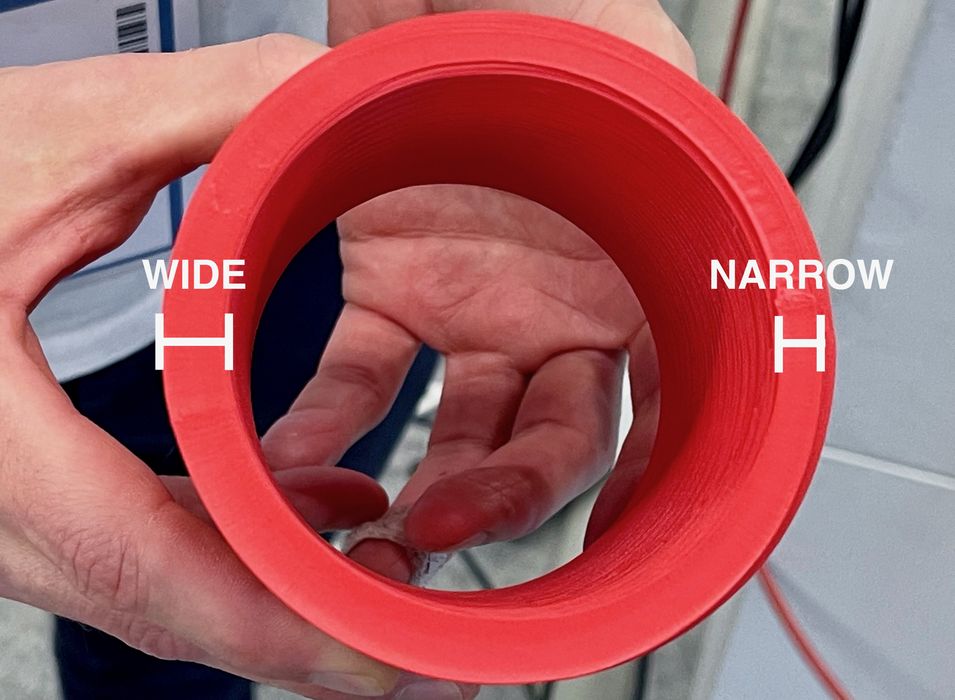
Here is a vase print showing the concept in action. It’s a bit hard to see, so I’ve annotated the image to show that on one side the extrusion is wide, while on the other it’s much narrower. This thing actually works.
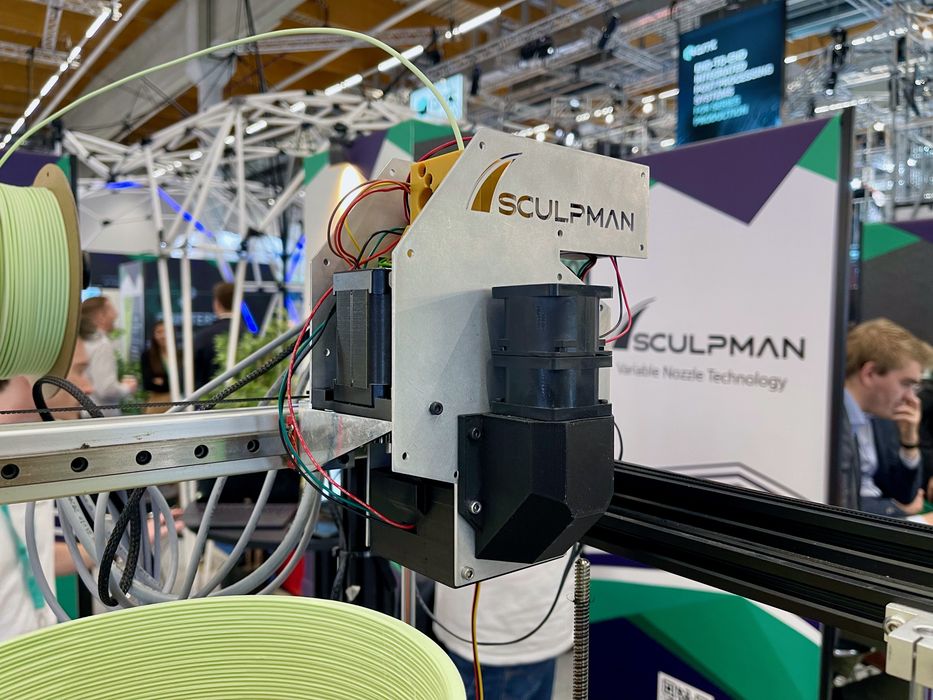
Sculpman does not intend on building 3D printers with this advanced nozzle, but instead wishes to work with OEMs to integrate their tech into other 3D printers. So far, I haven’t seen any takers, but perhaps that’s not surprising due to the complexity.
One unnamed OEM I spoke to regarding this technology was skeptical, asking “What happens when it jams? Would my team be able to fix it? How long would that take?” This take brings us back to reality: while a technology can be very cool, it also has to work effectively in the real world, and that’s quite another story.
Nevertheless, I’m hopeful that Sculpman is able to bring this product to market, as it would most definitely increase the power of 3D printers.
Via Sculpman