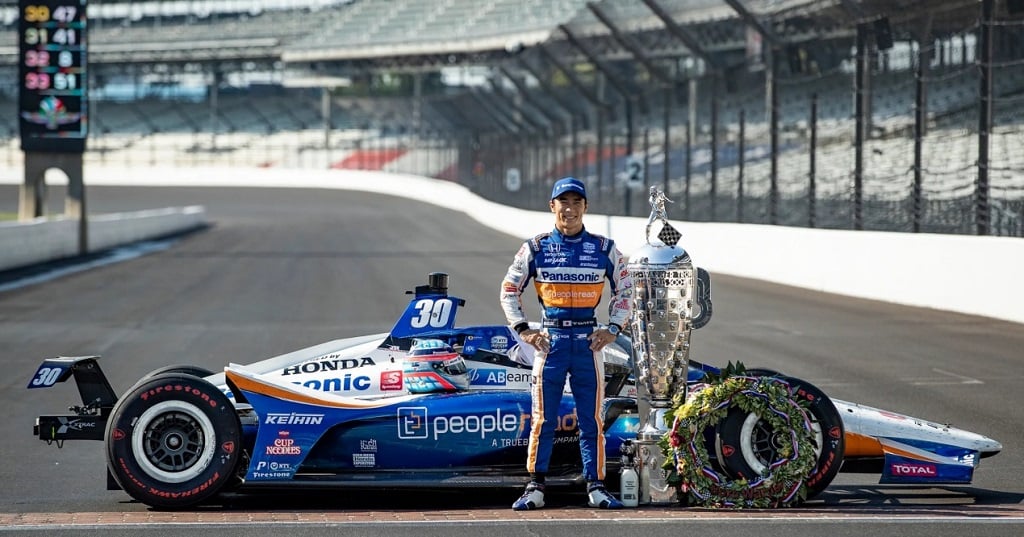
SPONSORED CONTENT
When it comes to racing, most of the focus is on speed — but work with SLS 3D printing is also helping critical braking components keep their cool for a winning IndyCar team.
Takuma Sato knows a thing or two about what it takes to win. He’s one of only 20 drivers to win the Indy 500 multiple times, racing to victory in both 2017 and 2020. This year’s victory came as Sato raced for Rahal Letterman Lanigan Racing (RLL) in a spirited and socially distanced edition of the popular race. In the last laps, one of Sato’s RLL teammates was involved in a crash that disrupted normal conditions. The driver was fortunately uninjured and the final five laps continued, with Sato’s victory declared “under caution” due to the less-than-pristine conditions of the track.
3D Printing On The Racetrack
Between the crash and the overall intensity of a close and hard-fought win, Sato’s skill came into the forefront — as did the conditions of his own car.
A race car is a sleek and specialized automobile, requiring significant modifications from a daily-use street car. Every component is carefully thought out and tested for constant performance as well as considerable regard for safety.
For years now, 3D printing has been in play among racing teams. The technology allows for the fast development of customized parts and new modifications. Many of these remain in the prototype or fit test stage, as the quickly 3D printed parts serve as a stepping stone to a final part. Some, though, are race-ready performance parts and pit use parts.
RLL Puts The Brakes On To Get Ahead
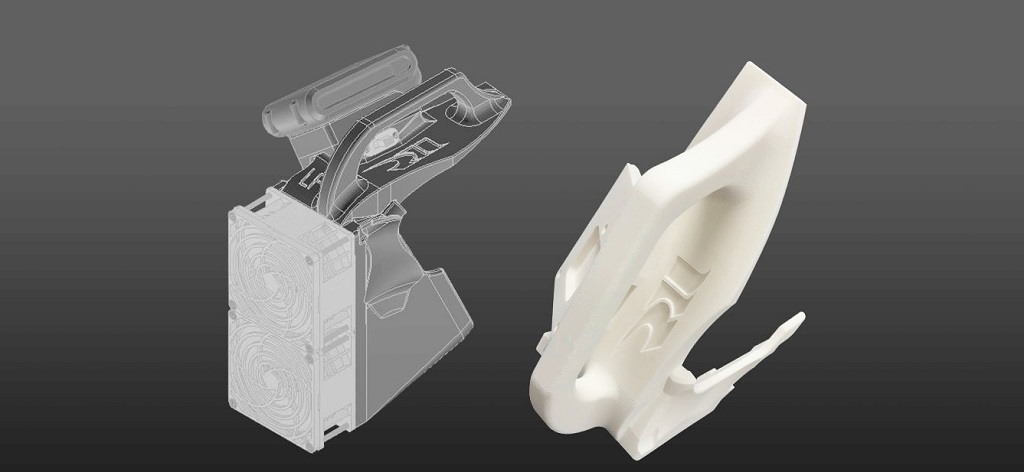
IndyCar racing is, unsurprisingly, demanding on vehicle components. Among those that are significantly taxed is the brake system.
Race cars on the track can reach high temperatures — extremely high temperatures. At 900°C or higher, the system has to be cooled down before the next application of brakes for best effectiveness. Heat dissipation in the brake system runs forced air through ducts into the rotors and calipers.
When the car stops, though, the brakes can heat soak. This can see those high temperatures come into play and ignite surrounding equipment. For best chances at winning, it’s generally best that a car not be on fire, so keeping the brakes cool during a pit stop is necessary to maintain the brake system’s integrity and keep the car safely operational.
This necessitates some specificity in the brake system, like easy-to-install and -remove fans. Pit stops must be a perfect, speedy symphony to minimize the stop and maximize time on the track, so that ease of placement is a must.
3D Printing For A Demanding System
The RLL team turned to 3D printing to create exactly what they needed.
The XYZprinting MfgPro230 xS system with sPro12W material offered the team exactly the accuracy, reliability, and durability the race track demands.
While the parts needed for the brake cooling system are larger than the MfgPro230 xS print bed, dimensional accuracy allowed for the team to create an interlocking assembly of parts. That assembly featured large pieces, inserts and electromechanical features that came together for a complicated design that ultimately the team would not have been able to manufacture.
Further, the sPro12W material is PA-12, providing the high strength required for a performance environment. These parts could also be colored to comply with series rules for this trackside application.
“Using XYZprinting’s Selective Laser Sintering technology we were able to improve the performance and capability of a critical trackside brake cooling system. The robust materials were easy work with and tough enough to build a brake cooling system that can endure a full season,” said Tom German, RLL Director of Engineering.
Ultimately, it seems, the RLL team has found a solution to make complex, high-performance parts that fit their specific needs.
Other companies, like HARBEC, TrySight, and Azoth, have also seen great success in meeting their manufacturing needs with the MfgPro230 xS as the SLS system can offer a fast return on investment and new capabilities for digital inventory.
Via XYZprinting