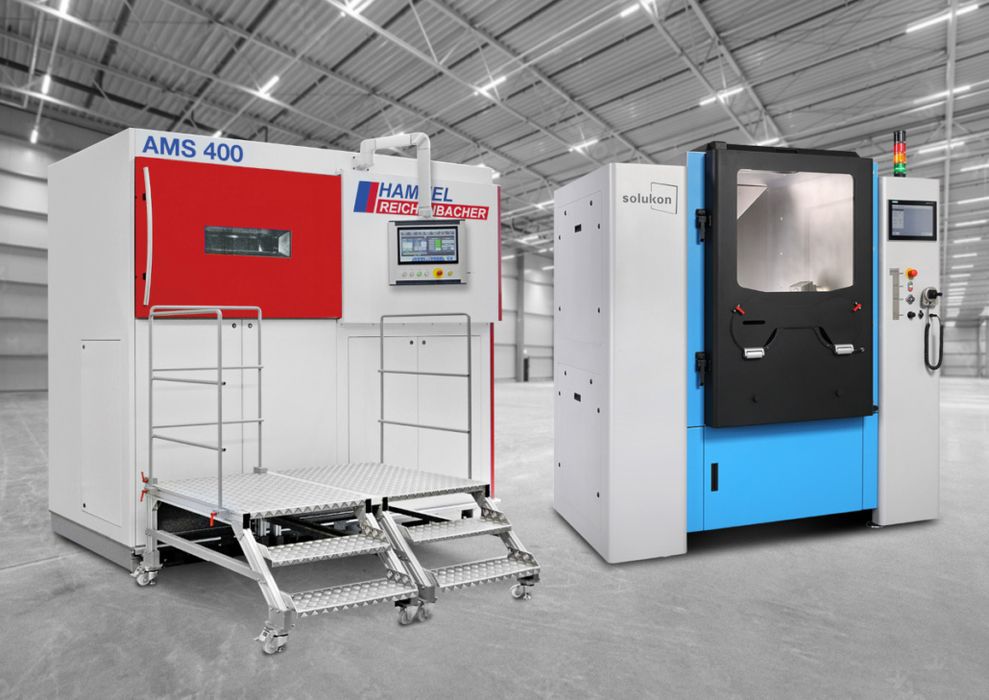
A new partnership has resulted in a significant optimization of powder-based 3D printing.
The partnership is between Solukon and Reichenbacher Hamuel GmbH. Reichenbacher Hamuel produces hybrid LPBF metal 3D printers, while Solukon produces depowdering equipment.
Depowdering is an essential part of the metal 3D printing lifecycle, as the nature of the LBPF process produces much powder for removal. At the end of print jobs, the completed parts are essentially buried within a rectangular chamber of loose powder.
That powder provided support for the part during printing, but afterwards it must be removed. Typically this is done by vacuuming out the powder, where it is then sent for cleaning and then possible reuse in future print jobs.
The vacuum process is almost always done manually by an operator, who will guide the vacuum toolhead through the larger areas of loose powder.
After the initial powder is removed for reuse, the dusty printed parts are then placed in the Solukon device for final powder removal. Solukonās system is quite interesting in that it carefully rotates the part in all axes to coax out any powder left in crevices. This is important for all parts, and critical for medical parts requiring certification.
The new partnership has resulted in a major simplification of this process. The concept is to rotate the entire build box upside down, causing the major portion of the loose powder to fall out. There it is recovered and handled in the same way vacuumed powder would have been processed.
This leaves the build box containing the metal parts ready for final depowdering. The build box in this case has sides that are removed, leaving it a straightforward process for the operator to slide the parts into the Solukon box for final depowdering.
Thera are some manual steps in the process, but there is far less work for the operator as no tedious vacuuming is required. The result should be a way to enable an operator to handle far more 3D printers, and thatās something highly desirable in rapidly expanding production facilities.
This is a good approach, but one that requires some changes in the 3D printer. Thatās been done by Reichenbacher Hamuel, but has not been done by other 3D printer manufacturers.
Organizations wishing to simplify their operator labor might consider acquiring this equipment pair. It may be that the time saved could make a substantial financial difference over longer periods.
What might help in this situation is a standard build box design or even dimensions, which would allow post processing equipment manufacturers to address more 3D printer models.
In the meantime, other LPBF operators are faced with more manual effort simply because there are no accepted standards in this area.
Via Solukon and Reichenbacher Hamuel