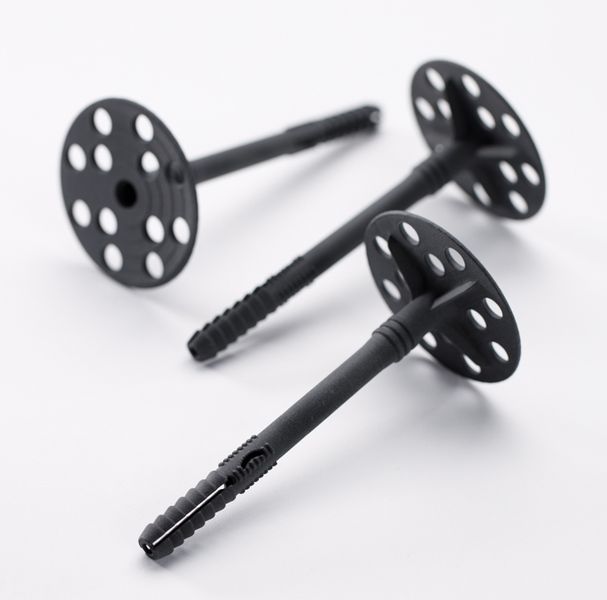
SPONSORED CONTENT
A manufacturer has discovered the possibilities enabled by low-cost SLS 3D printing.
SLS is a popular 3D printing process for manufacturers because it is able to produce relatively strong parts in very good quality. It can also do so in quantity because the process allows the possibility of stacking 3D prints vertically within the build chamber, unlike most other 3D print processes.
Because of this, many manufacturers use SLS to produce prototypes for their innovative products. The prototypes allow designers to physically examine their product ideas. They can even perform basic testing because the usual nylon materials used in SLS are strong enough for a number of applications, and thus can mimic the eventual production parts that are typically made with injection molding processes.
This is the situation at Rawlplugs, a manufacturer of wall plugs — also known as “anchors” in North America. These are small plastic devices that can be used to attach an object to a wall when there are no other means of doing so.
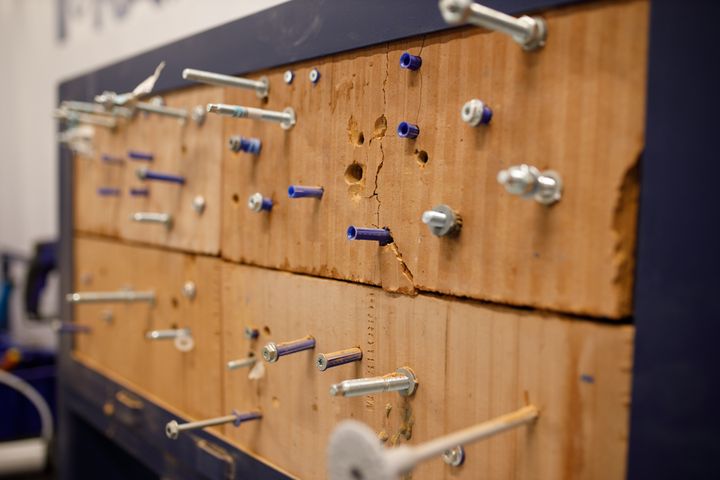
Fun fact: Rawlplugs was the company that first invented the concept well over 100 years ago. They were formed in 1887 in London and were tasked with attaching items to the walls of the reknowned British Museum. Their invention was the now-ubiquitous wall plug, or as I know them best, anchors.
Today in the 21st century Rawlplugs still makes wall plugs of many forms. They are considered a leader in this niche manufacturing space, and continue to develop products around the concept.
Their process is straightforward: 3D model a new concept, and then 3D print a prototype for testing. This is repeated until the prototype is deemed successful, whereupon it will be moved forward for production using injection molding.
3D printing is used for prototyping because it is far faster and less expensive than the older approach of using injection molding. Many companies use that approach, including Rawlplugs.
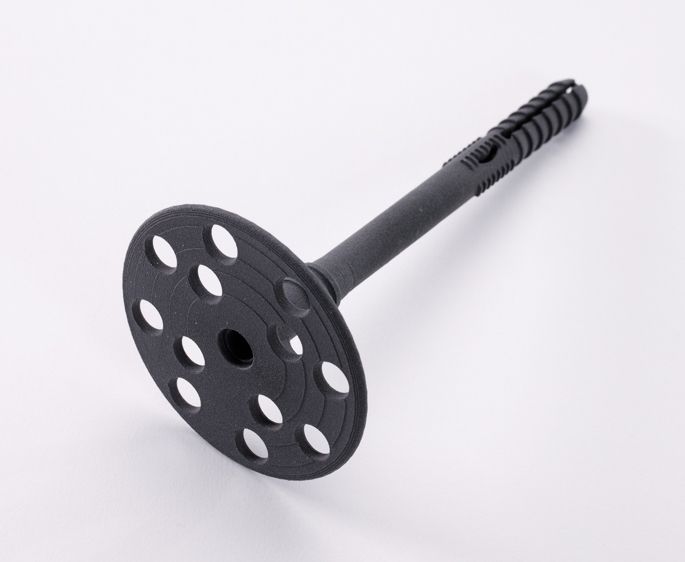
However, there’s an issue. Rawlplugs has been outsourcing their prototype 3D printing to external services, and while the 3D printing can be quick, the interaction with the service adds several days to the process. They say it takes about two weeks to obtain a prototype 3D print from their usual provider. This is likely due to several time-absorbing steps in the service usage process:
- Queuing time for 3D model inspection
- 3D model inspection and tweaking
- Queuing time for 3D printing
- The actual 3D printing
- Queuing time for post-processing
- Post-processing
- Packaging
- Shipment time
- Delivery and movement from the mail room to the design studio
Many of these steps could be literally eliminated if Rawlplugs simply used their own 3D printer.
But they could not.
The reason they were unable to use their own SLS 3D printer was cost: typical commercial SLS 3D printers are quite expense and with large build volumes. These machines are designed for production, and they make financial sense to own only if you have sufficient print frequency to keep them busy 24/7.
For a design studio doing occasional prototype 3D prints, that’s not really the case. Thus these options were priced out of the market for Rawlplugs and many other light users of SLS 3D printing.
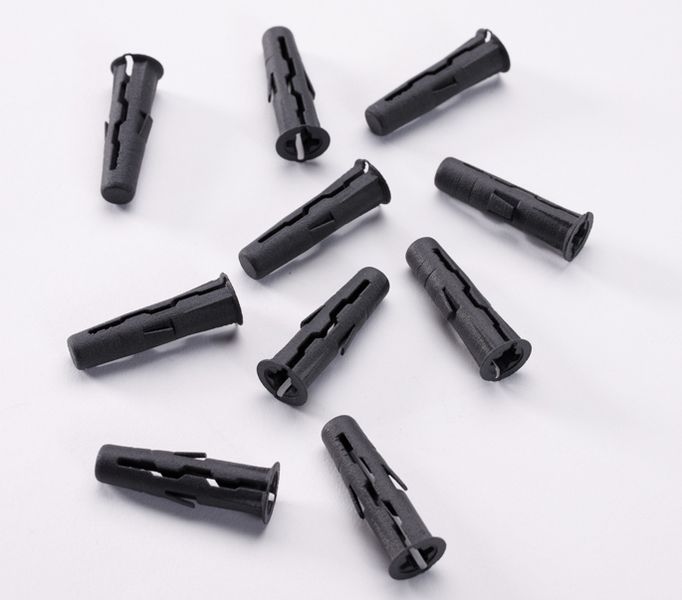
Enter Sinterit, which produces a small-volume, low-cost SLS 3D printer. Their flagship 3D printer, the LISA Pro, can be acquired and operated for vastly less cost than typical SLS 3D printers.
According to Dominika Zarowna, Designer Engineer at Rawplug:
“When I first came on board as a new hire, we used to outsource the printing to third parties.
This often took a considerable amount of time. What we needed was a 3D printer of our own, in
order to reduce the waiting times to a minimum. At the same time, we were on the lookout for
new technologies. Given the price and quality requirements, Lisa PRO was the only real choice
on the market.”
Sinterit believes the operating cost of their equipment is about 10% of the typical cost of traditional SLS equipment, and this opens up the possibility for lower-use operations such as Rawlplugs to directly own and operate their own equipment.
But is the device fast enough to overcome the delays incurred when using an external 3D print service? Zarowna explains:
“Lisa PRO is not quite the quickest 3D printer, but for us, that is not a big concern, because we reduced the waiting time for prints from 2 weeks to 2 days. We have additionally worked out a system, where we start printing on a Friday afternoon and the prints are already waiting for us on Monday when we come to work.”
This scenario is likely the same in many small manufacturing businesses, who now have the option to operate their own SLS 3D printing prototyping equipment.
Via Sinterit