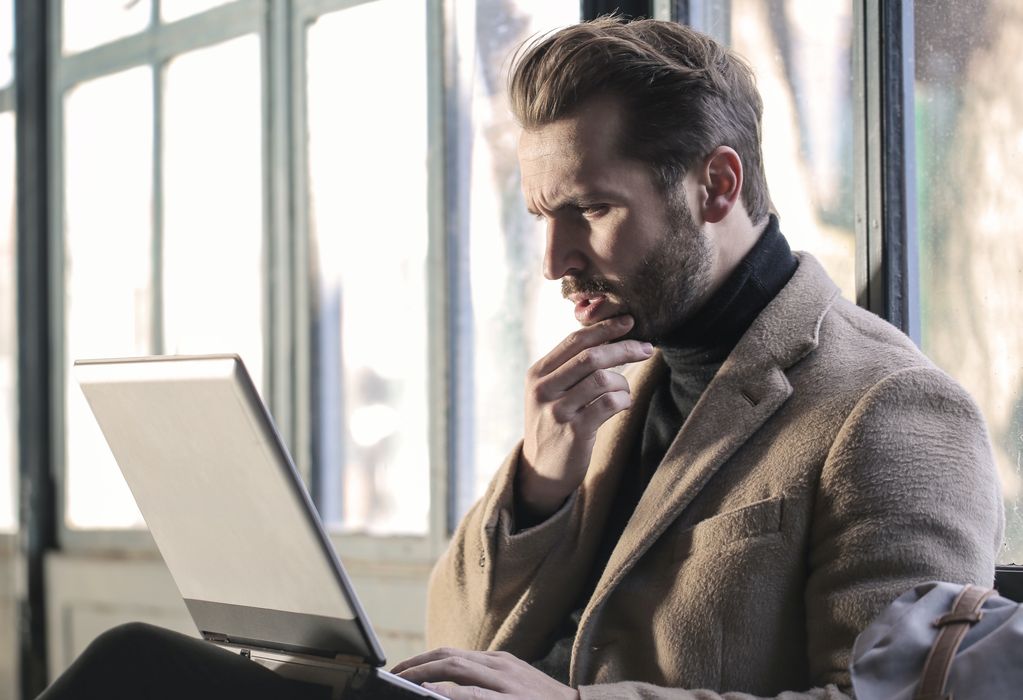
Many Asia-based desktop 3D printer manufacturers suffer from a key limitation that holds back their growth.
Donāt get me wrong here; there are plenty of incredibly powerful desktop 3D printers. The hardware has been refined over years of development by many companies and today theyāre used by hundreds of thousands of 3D printers operators, including me.
But all too often there is a familiar problem that appears on most machines: the interfaces and documentation.
Itās common to find instructions included with a machine that are so poorly translated that they cannot be properly understood. This is particularly problematic if the documentation is minimal, leaving operators mostly on their own.
Even worse is that the companiesā casual attitude towards communication with the operator extends from the documentation into the machine itself and its associated software. You will frequently find āunusualā terms and many times Iāve been confounded by what I see. The result is a bunch of trial and error experimentation to figure out what is being meant.
Machine interfaces tend to be very rudimentary and styling, if any is used, is near non-existent, aside from happy tunes that sometimes greet the operator upon system power-up. Those tunes are not helpful in any way.
All of these things are non-issues for competent 3D printer operators, who either are accustomed to the terrible interfaces or are technically able to figure them out. For many, these limitations are not significant and they do not detract from purchase decisions.
But I think these 3D printer manufacturers are missing something very important: these limitations directly constrain the potential buyers to those tech-savvy folks. Meanwhile, there are a thousand times as many people with less technical ability that did NOT buy these 3D printers, partially because they are so confounding to use.
I often wonder why some of these 3D printer manufacturers donāt simply hire competent UI designers to create smooth and friendly interfaces for operators, or at least clean up the documentation so that it is comprehensible by most people.
Actually, I do know the answer: itās the race to the bottom.
Desktop 3D printer manufacturers find themselves in a ārace to the bottomā, where the lowest price wins the race. This means successful companies very strongly focus on keeping costs down as low as possible in every conceivable aspect.
The lowest cost components that make the machine function will be used. The lowest cost manufacturing process will be used. Designs will be re-used wherever possible. This has to be done on each and every project, year after year. You get the idea.
Itās very likely these companies have unconsciously created internal company cultures of ālow-cost everythingā. Theyāve had to in order to survive this long in such a highly competitive market.
Because of that culture, I suspect many of them either ignore the UI aspects of their machines in order to save costs, or somehow donāt believe the interfaces are important. They could see resources spent on UI as wasteful.
I believe UI is important. I also believe many more people would purchase this type of equipment if it were friendlier to less technical buyers. Itās likely these manufacturers are ignoring a larger market because of their overly strong focus on lowering costs.
Imagine if a major desktop 3D printer manufacturer took on this challenge and devised a standard, easy-to-use UI system for their machine ā and used it on ALL of their machine, even new versions. Buyers would be familiar with that interface, and be more likely to purchase upgrades. Their experiences would be shared with others, who might be more attracted to the idea of desktop 3D printing.
As of this writing, I am not aware of any developments of this nature. However, the first major desktop 3D printer manufacturer that seriously focuses on a modern UI in their hardware, documentation, and software could break out of the race to the bottom and bring in many more 3D printer operators.