There are countless 3D printing processes, but I like to divide the metal ones into two categories.
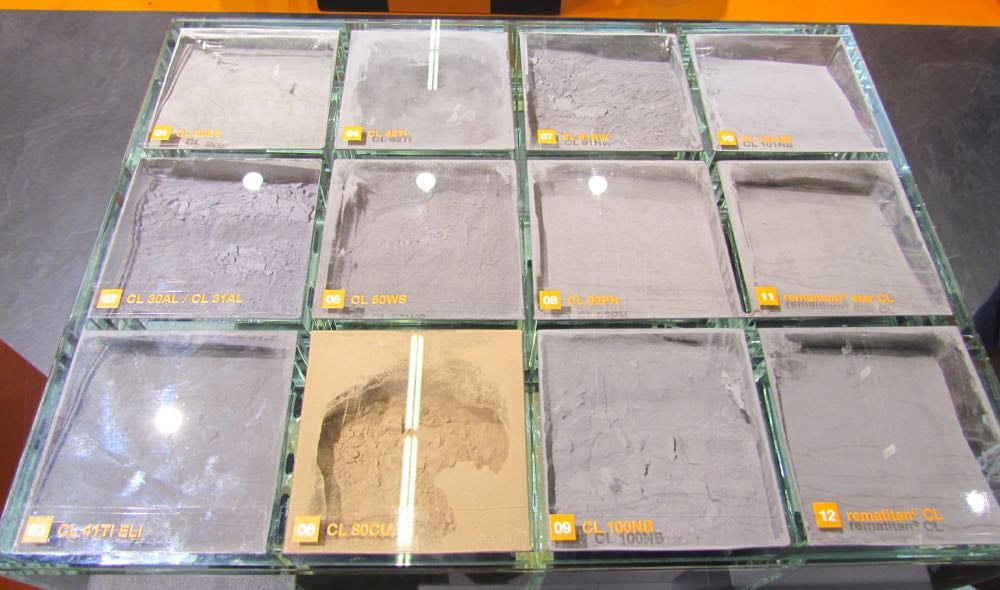
Those categories would be “dangerous” and “less dangerous”.
Why do so? It seems to me there are really two types because the material differs significantly. One uses fine metal powder, while the other does not.
Metal powder is perhaps the premiere material for high quality 3D printing. Companies such as EOS, 3D Systems, Trumpf and several others use either laser or electron beam systems (DLMS or EBM) to selectively fuse layers of metal powder to form solid metal objects.
But using powder poses all kinds of challenges.
Metal powders can be quite toxic if inhaled, and the powder used in these systems is quite small in order to achieve good quality, high resolution metal parts. The small size of the particles means they can get airborne.
Certain metal powders are also explosive. Did you know that the Space Shuttle’s solid rocket boosters were fueled by aluminum powder? Think about that when observing an aluminum 3D print job, and be thankful that the build chamber is evacuated of oxygen.
The powders can also be dramatically affected by exposure to the environment. Humidity and oxygen can result in corrupted parts that are of no value for production.
These effects dramatically complicate any system that uses metal powder. To be clear, these challenges have been overcome through the use of sophisticated machine and accessory designs, but that also means the equipment carries a higher cost to own and operate.
Meanwhile, there is the less dangerous category of metal 3D printing where other processes are used.
One style uses wire extrusion instead of powder. The wire is melted as it exits the extruder and is immediately deposited on a surface. Because the wire is solid and not in powder form, it’s much easier to handle. Sometimes this is called Direct Energy Deposition, or DED.
Another style is “cold” metal 3D printing. This style involves depositing metal powder with a binder of some sort, with example processes from companies like Desktop Metal and XJET, as well as BASF’s Ultrafuse metal filament. All of these processes require post processing in a sintering furnace, but it’s far safer and less complex than using powder directly.
Finally, there are a couple of unique metal printing processes. One is from Spee3D, which blasts metal particles at a target at supersonic speed. The kinetic energy forces the molecules to bond without the use of heat, and is somewhat safer than the PBF approaches.
Another is Fabrisonic’s ultrasonic approach, where thin sheets of metal are agitated so that the molecules naturally bond with each other, layer by layer. Again, no heat is involved.
With several “safer” processes for metal 3D printing available, why would companies use the more complex PBF processes?
The reason is that the PBF processes still provide better quality metal output, often at better resolution than other processes. DED and Spee3D have somewhat lower potential resolution, while the cold processes require the object to shrink during post processing heat treatments, making dimensional accuracy more challenging.
Every 3D printing process has its advantages and disadvantages; none of these processes are wrong. It’s just that some may fit the application better than others.
In the future we will certainly see entirely new metal 3D printing processes that could replace some or all of the above.