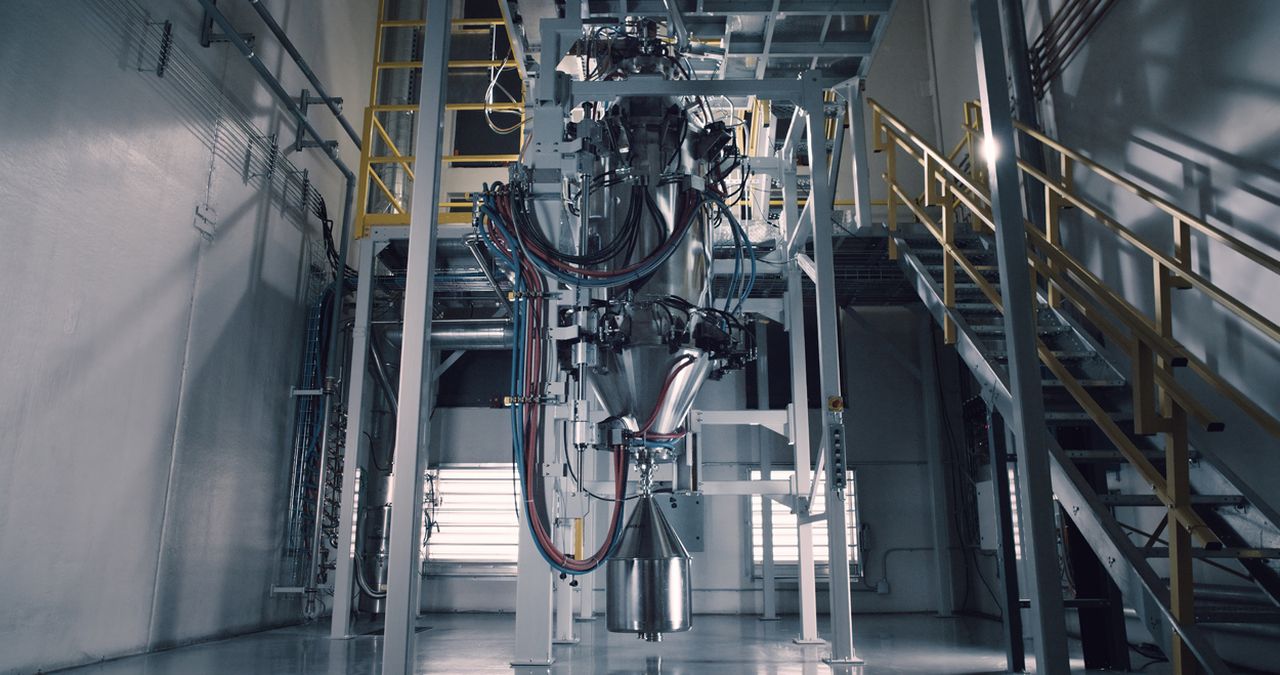
There’s a shift in manufacturing happening due to world events, but are we seeing a corresponding change in additive manufacturing?
The pandemic messed up many things, and it’s only in recent months that things are coming back to “a normal state”. It’s a little different than what it was before, but at least it seems to be a sustainable course.
However, one event is causing change: the Ukraine conflict. This has gone on since February of last year, and it seems as though it will last for quite a bit longer.
If one follows the reports from the conflict, you’d see lists of massive quantities of military equipment being destroyed daily. According to today’s report from the Ukrainian side, Russia has lost over 4600 tanks, almost 9000 armored vehicles, and 6300 artillery systems. That is an enormous number of items. The Ukrainian losses are not published, but one can surmise they are also significant.
The West has been supplying Ukraine with significant weaponry, mostly leftover items that would otherwise have to be disposed of with expensive procedures. New or old, however, the equipment must be replaced.
In some cases, the movement of equipment has triggered new acquisitions by various countries. Out with the old, in with the new.
That “new” equipment must be manufactured, and no doubt some of the components will be produced using additive manufacturing processes.
This is an entirely slow process, however, so I’ve been watching for many months to see signs of this in the 3D print community.
Yesterday I finally saw something that matches this pattern: 6K Additive announced a new deal with the US military.
The company now has a “blanket purchase agreement” with the US Army Development Command to produce “strategic high-performance metal powders”. This was the conclusion of a competitive bid process by the military.
The US Army will use 6K Additive’s proprietary UniMelt microwave-based system to produce quantities of metal powder. They will use the powder to support the development of prototypes and small volume production.
The UniMelt system is able to process scrap metal into high quality powder for use in LPBF additive manufacturing systems. That feature allows the military to easily source material that is not only domestically sourced, but is also entirely traceable.
6K Additive lists some of the benefits of this arrangement:
- Reducing the risk of dependence on foreign supply: As there is constrained domestic availability of strategic metals such as superalloys, the ability to utilize materials from the nation’s boneyards and machine shops, such as end of life components, shop scrap, or used powders and convert them into high-quality materials, provides the US military with a secure domestic supply of critical metals.
- A closed-loop enhanced security: Of crucial concern is the quality and consistency of foreign-sourced materials. Recycling previously qualified DoD parts, shop scrap, and used powders creates a closed loop for material with the quality being known and traceable. Unexpected performance anomalies due to questionable sourcing can be prevented.
- Advanced systems faster to the field: High quality recycled materials will help the DoD develop and adopt advanced additive manufacturing, metal injection molding, and powder forging processes more quickly, allowing them to create parts with novel functionality, reduce engineering cycles and accelerate “make-to-fly” cycles. This translates to enhanced lethality with reduced costs.
- Managing costs while maximizing quality: Using already certified scrap as raw material dramatically reduces the material cost of goods for manufactured parts and ensures they meet the desired specification.
Is this the big AM breakthrough that will help fill the manufacturing gap created by the conflict? Not quite, but it’s a good start.
Via 6K Additive